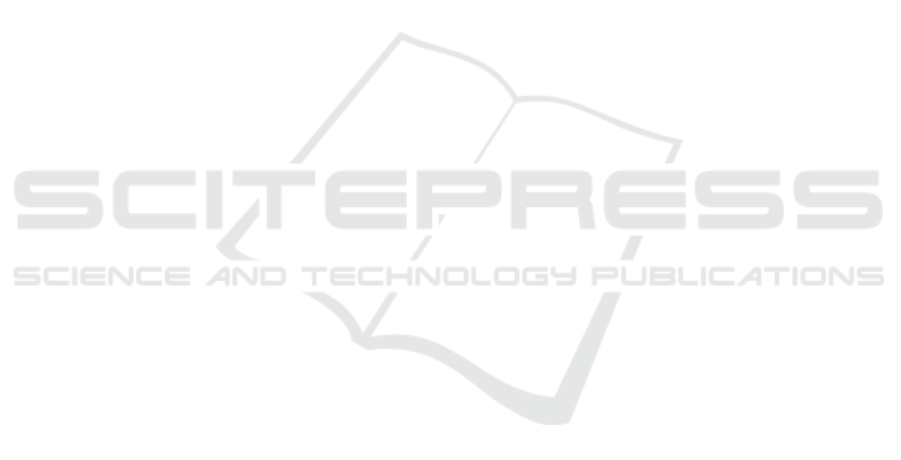
ACKNOWLEDGEMENTS
We thank the reviewers for helpful comments that
improved our work. This work was supported by a
grant of Ministry of Research and Inovation, CNCS-
UEFISCDI, project number PN-III-P1-1.1-TE-2016-
1317, within PNCDI III (2018-2020).
REFERENCES
AUTOSAR (2015a). Specification of Crypto Abstraction
Library, 4.2.2 edition.
AUTOSAR (2015b). Specification of Crypto Service Man-
ager, 4.2.2 edition.
AUTOSAR (2017). Specification of Secure Onboard Com-
munication, 4.3.1 edition.
Beaulieu, R., Treatman-Clark, S., Shors, D., Weeks,
B., Smith, J., and Wingers, L. (2015). The si-
mon and speck lightweight block ciphers. In 2015
52nd ACM/EDAC/IEEE Design Automation Confer-
ence (DAC), pages 1–6. IEEE.
Checkoway, S., McCoy, D., Kantor, B., Anderson, D.,
Shacham, H., Savage, S., Koscher, K., Czeskis, A.,
Roesner, F., Kohno, T., et al. (2011). Comprehensive
experimental analyses of automotive attack surfaces.
In USENIX Security Symposium. San Francisco.
Ergen, S. C. and Sangiovanni-Vincentelli, A. (2017). In-
travehicular energy-harvesting wireless networks: Re-
ducing costs and emissions. IEEE Vehicular Technol-
ogy Magazine, 12(4):77–85.
Ishtiaq Roufa, R. M., Mustafaa, H., Travis Taylora, S. O.,
Xua, W., Gruteserb, M., Trappeb, W., and Seskarb,
I. (2010). Security and privacy vulnerabilities of in-
car wireless networks: A tire pressure monitoring sys-
tem case study. In 19th USENIX Security Symposium,
Washington DC, pages 11–13.
Koscher, K., Czeskis, A., Roesner, F., Patel, S., Kohno,
T., Checkoway, S., McCoy, D., Kantor, B., Anderson,
D., Shacham, H., et al. (2010). Experimental security
analysis of a modern automobile. In Security and Pri-
vacy (SP), 2010 IEEE Symposium on, pages 447–462.
IEEE.
Krawczyk, H., Bellare, M., and Canetti, R. (1997). Hmac:
Keyed-hashing for message authentication. Technical
report.
Miller, C. and Valasek, C. (2014). A survey of remote auto-
motive attack surfaces. Black Hat USA.
Solomon, C. and Groza, B. (2015). Limon - lightweight
authentication for tire pressure monitoring sensors. In
1st Workshop on the Security of Cyber-Physical Sys-
tems (affiliated to ESORICS 2015).
Takahashi, J., Aragane, Y., Miyazawa, T., Fuji, H., Ya-
mashita, H., Hayakawa, K., Ukai, S., and Hayakawa,
H. (2017). Automotive attacks and countermea-
sures on lin-bus. Journal of Information Processing,
25:220–228.
Toth, A. (2014). Method and system for monitoring a
parameter of a tire of a vehicle. EP Patent App.
EP20,120,464,019.
van Zyl, P., Goethem, S. v., Jansen, S., Kanarchos, S., Rex-
eis, M., Hausberger, S., and Smokers, R. (2013). Study
on tyre pressure monitoring systems (tpms) as a means
to reduce light-commercial and heavy-duty vehicles
fuel consumption and CO2 emissions. Delft: TNO.
Xu, M., Xu, W., Walker, J., and Moore, B. (2013).
Lightweight secure communication protocols for in-
vehicle sensor networks. In Proceedings of the 2013
ACM workshop on Security, privacy & dependability
for cyber vehicles, pages 19–30. ACM.
Yan, C., Xu, W., and Liu, J. (2016). Can you trust au-
tonomous vehicles: Contactless attacks against sen-
sors of self-driving vehicle. DEF CON, 24.
Security for Low-end Automotive Sensors: A Tire-pressure and Rain-light Sensors Case Study
33