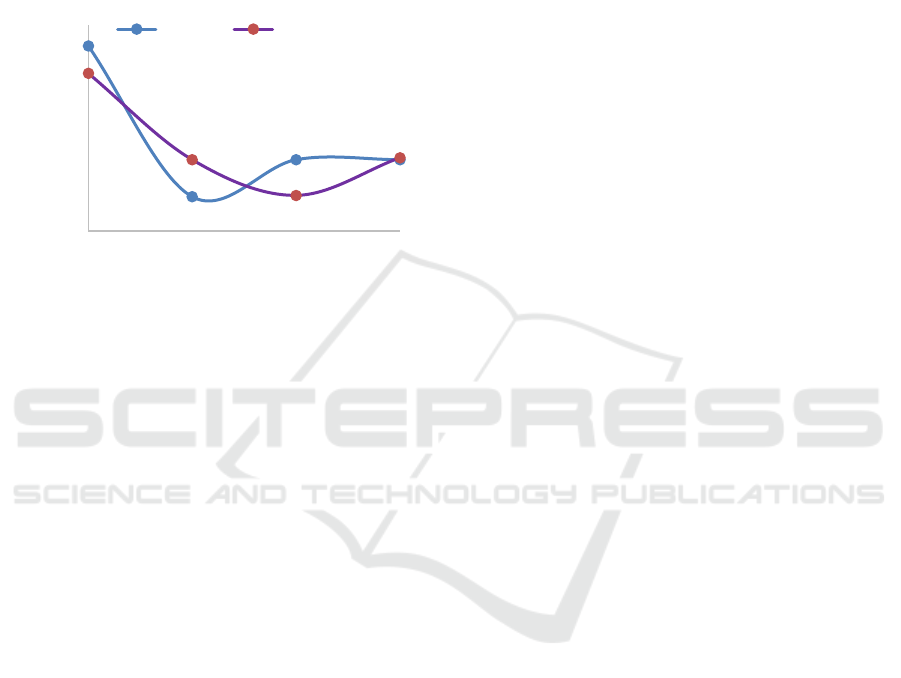
K
2
O was lower. But at temperature combustion at
650 the rendemen both of sample for 3 hours and 6
hours time of combustion are same at 15.7% of
rendemen. It is caused not due to potassium is lost or
evaporates, however, the decrease in K
2
O levels may
occur with increase temperature, because the amount
other alkaline components increases with increasing
temperature at the longer time (Perry, 1999).
Figure 4: Influence of Time and Temperature Combustion
versus levels of K2O.
4 CONCLUSIONS
The conclusions from this research are the highest
yield of K
2
O from kapok pods on the pyrolysis
combustion for 3 hours at 500˚C with levels of K
2
O
of 35.91%. Pyrolysis process time 6 hours is better,
because the ash was obtained in the form of oxide.
While the process time is 3 hours the resulting ash
still contain abundance elements of carbonate.
Increase the temperature of pyrolysis will also
improve the normality and pH, as well as increasing
the time of pyrolisis also will raise the pH and
normality. Potassium content in ash kapok pods can
be used as a source of alkaline solution.
REFERENCES
Abba, H. A. 2013. Review of Agro Waste Plastic
Composites Production. Journal of Minerals and
Materials Characterization and Engineering, 1, 271-
279.
Babayemi, J. O. 2010. Evaluation of the Composition and
Chemistry of Ash and Potash from Various Plant
Materials-A Review. Journal of Applied Sciences, 10:
1820-1824.
Bates, D. M. 2004. Malvales. CD Version: Encyclopaedia
Britannica.
Brown, S. H. 2017. Ceiba pentandra. Horticulture Agent.
Florida, South West Florida: University of Florida.
Chaiarrekij, S. A. 2011. Kapok 1: Characteristics of Kapok
Fibre as A Potential Pulp Source for Paper Making.
Journal of Bioresources , 7 (1), 475-488.
Chekuboyina, R. K. 2012. Physico-Chemical
Characterization and Antimicrobial Activity of Ceiba
Pentandra (Kapok) Seed Oil. Journal Alt med studs, 2-
9.
Green, R. H. 1999. Perry's Chemical Engineer's Handbook.
New York: McGraw-Hill Companies, Inc.
Haygreen, J., G. 1996. Hasil Hutan dan Ilmu Kayu, Suatu
Pengantar.Hadikusumo SA, Penerjemah. In
Terjemahan dari: Forest Products and Wood Science:
an Introduction. Yogyakarta: Gadjah Mada University
Pr.
Hendra D., Winarni, I. 2003. Sifat Fisis dan Kimia Briket
Arang Campuran Limbah Kayu Gergajian dan Sebetan
Kayu. Jurnal Penelitian Hasil Hutan, 21(3), 211-226.
Anigo, K., M., Dauda, B., M., D., Sallau, A., B., and
Chindo, I., E., 2013. Chemical Composition of Kapok
(Ceibapentandra) Seed and Physicochemical Properties
of its Oil. Nigerian Journal of Basic and Applied
Science, 21(2): 105-108.
Kapok Tree (Ceiba Pentandra). (2012, September 13).
Retrieved June 29, 2017, from http://www.rainforest-
alliance.org/species/kapok-tree.
Laird, D., A. 2009. Review of the pyrolysis platform for
coproducing bio-oil and biochar†. Biofpr (Biofuels,
bioproducts and biorefining), 1-16.
Misra, M., K. 1993. Wood Ash Composition As a Function
of Furnace Temperature. Biomass and Bioenergy, 4(2)
113.
Mojica, E., R. 2002. Fiber of Kapok (Ceiba pentandra) as
Component of A Metal Sensor for Lead in Water
Samples. Philippines Journal of Crop Science, 27 (2),
37-42.
Ningrum, N., P. 2013. Pemanfaatan Minyak Goreng Bekas
dan Abu Kulit Buah Kapuk Randu (Soda Qie) Sebagai
Bahan Baku Pembuatan Sabun Organik Berbasis
Teknologi Ramah Lingkungan. Journal Teknologi
Kimia dan Industri, 2 (2), 275-285.
Orwa, C., M. 2009. Agroforestree Database: a Tree
Reference and Selection Guide Version 4.0. Kenya:
World Agroforestry Centre.
Perry, R., H. 1999. Chemical Engineers Handbook Physical
and Chemical Data (Vol. 7). Mc Graw Hill Company
Purbasari, A., S. 2008. Pembuatan Pupuk Kalium-Fosfat
dari Abu Kulit Kapok dan Tepung Fosfat secara
Granulasi . Jurnal Ilmiah Bidang Ilmu Kerekayasaan ,
29-2.
Putra, I., T. 2014. Karakteristik Kimia Kulit Buah Kapok
Randu sebagai Bahan Energi Massa .
Putri, E., M. 2012. Biodiesel Production from Kapok Seed
Oil (Ceiba Pentandra) through The Transesterification
process by using cao as catalyst. Global Journal of
Researches in Engineering Chemical Engineering, 12
(2), 6-11.
Rainforest-alliance.org. (2018, September). Retrieved from
https://www.rainforest-alliance.org/species/kapok-tree.
5
10
15
20
25
30
35
500 550 600 650
3 hours 6 hours
Temperature of Combustion (˚C)
Amounts of K
2
O (%)
Pyrolisis of Kapok (Ceiba pentandra) Pods Wastes as Sources of Potassium Oxide (K2O)
233