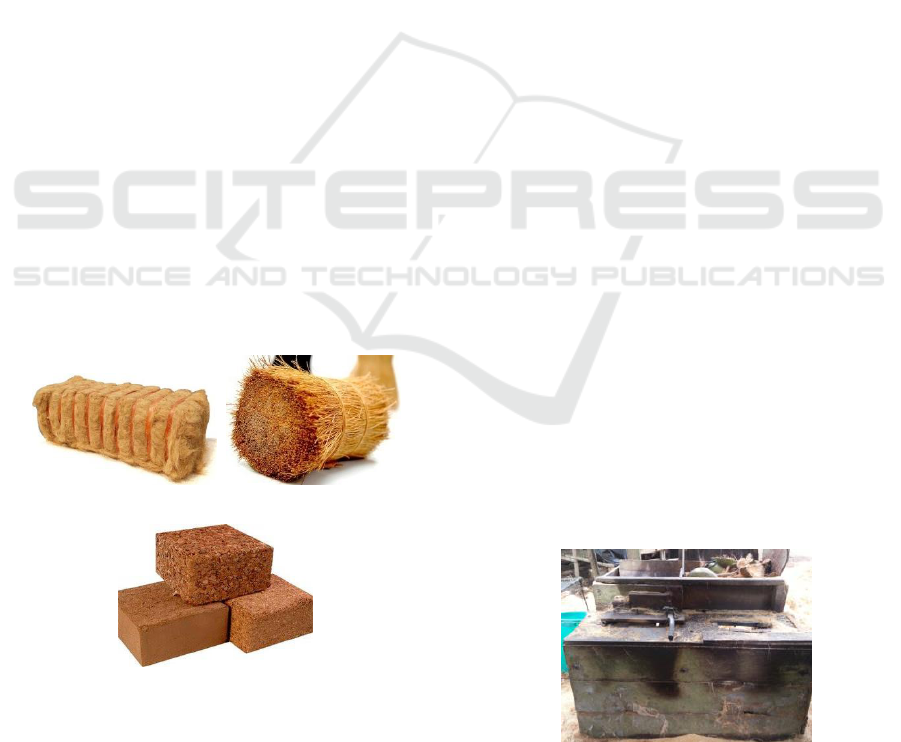
per kilogram. Coconut production in Indonesia
reaches fifteen billion pounds per year and which can
be processed only reach to 480 million grains or 3.2
percent, it is estimated that Indonesia loses Rp 13
Trillion per year from unprocessed coconut husk
(Nara, 2014). Therefore it is necessary to research the
development of coconut processing business, one of
which can be done with the design of work systems.
The design of work system aims to produce a
comfortable working system, safe, and healthy for
workers and produce output in accordance with the
desired. The design of the work system has three
variables, namely the use of the human body,
preparation and workplace conditions, as well as the
design of tools and equipment’s. The improvement of
the work system design should pay attention to
these three variables well (Niebel, 2007).
This study focuses on the improvement of two
aspects in the design of the work system, which are
the design of equipment and the use of the human
body to increase the production of one of the coconut
derivatives, namely coco bristle. One coconut can
produce 35% coconut husk. From this coconut husk
can be processed into coco fibre products i.e coconut
husk that has been decomposed into fibres.
This coco fibre products can be processed into
coco bristle and coco peat. Coco fibre can be
processed into tiles, coco charcoal, coir carpet which
called Mourzouks, coir belts, and others. While coco
bristle can be used to make products such as sofa,
motorseat, brush, doormat, etc. While coco peat is
generally used as a medium for planting and organic
fertilizer (Kavitha, 2015).
(a) (b)
(c)
Figure 1: (a) Coco Fiber (b) Coco Bristle (c) Coco Peat.
At the research location, coco bristle processing is
done by using machine called coco bristle machine.
This machine has two parts, where the first part serves
to destroy the outer coconut skin. The production
process is the operator pinning the tip of the coir then
put it into the machine so that the coconut outer shell
is destroyed and leaves the long fibers called coco
bristle. This step is done repeatedly for both sides. The
second part serves to destroy the tip of the coir that is
still there to get a clean coco bristle from the outer
skin. The steps taken are the operator holding the
finished coco bristle part and pinning the remaining
heads, and done repeatedly. Such parts may be
dangerous to the operator if the operator's hand is
drawn into it. The operator does not use any safety
device to protect his hand from the machine. This
shows that the design of the machine still does not pay
attention to the safety of the workers.
Research on coconut coir machine design has been
done before in (Widananto, 2015) and (Villa, 2016),
but there is no further research especially on the design
of coco bristle machine. Therefore, the improvement
of coco bristle engine design is expected to increase
the amount of production so that the company can
meet the demand while increasing the comfort and
security of the operator.
In this research there will be designing coco bristle
machine with anthropometry approach. The machine
will be designed to fit the worker's body dimensions
and will be designed to get a safer and more
convenient way of working.
2 METHODS
This research was conducted on a coconut processing
SME but the research object focused on coco fiber
making. The research procedures conducted in this
research are:
1. Preliminary Research
This stage is used to diagnose the problems found
in coco bristle making work stations. At this stage,
the data on the initial machine specifications are
also collected as the design basis.
Figure 2: Condition of Coco Bristle Initial Machine.
The Effect of Improvement on Work Facility of Coco Bristle Process to Occupational Health and Safety
359