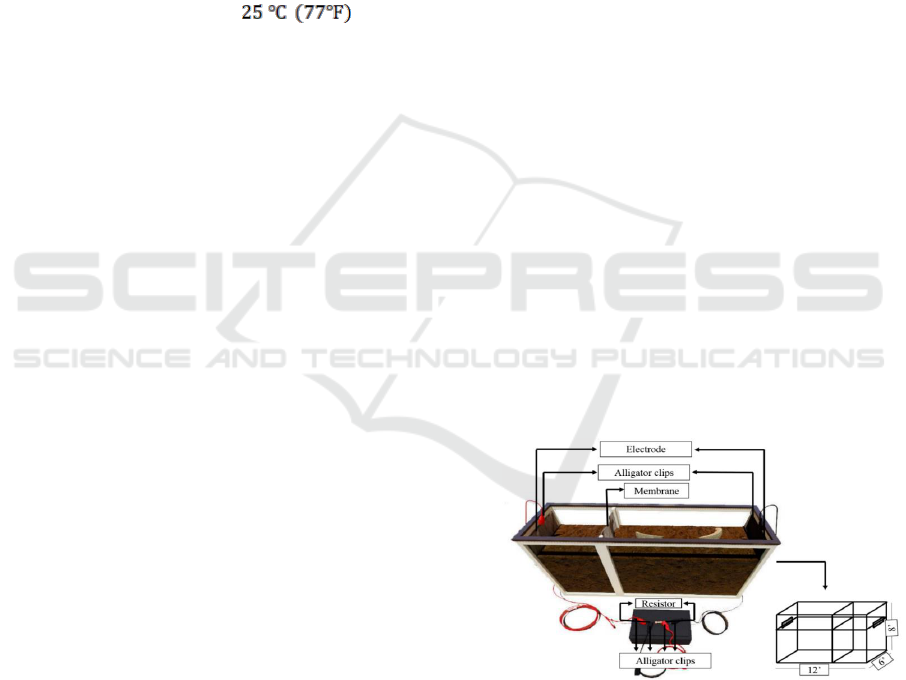
Fuel Cell (VBMFC) was born. In this set-up, solid
biodegradable waste is fed to earthworms, much like
in vermiculture. The worm castings then become a
prime nutrient source for bacteria to consume and
generate electricity with carefully-placed electrodes.
Desirable qualities for a VBMFC would be high
power generation, low internal resistance, and low
cost, much like in MFCs. Earthworm selection is
also to be considered. Commonly, Red wigglers
(Eisenia fetida) are thought to be the most adaptable
of all the vermicomposting worms, but comparing it
with other worms in terms of selected parameters
(e.g. size, time of maturity, incubation time, ideal
working temperature, etc.), the African nightcrawler
seems more capable. In laboratory tests, E. eugeniae
outperformed E. fetida at in tests
utilizing cattle manure as the feedstock. Also, some
assert that E. eugeniae also slightly sensitive to
handling and disturbance. It appears that it is not
usual for E. eugeniae to start roving after disturbance
or even clear reasons at all. That being said, E.
eugeniae appear to be the most popular choice
among vermicomposters due to its quick growth and
bigger size compared to E. fetida [5].
There are still some ongoing studies on ways to
collect electricity from different variants of MFC
like Plant-Microbial Fuel Cells (PMFCs) [6] and
Constructed-Wetland Microbial Fuel Cells
(CWMFCs). However, there are no studies that
explore VBMFCs for their power generation and
waste management capabilities. In terms of its
operation, it is similar to an MFC but differs on the
substrate. Conventionally, MFCs include a
membrane separator to segregate charges in the
anode and cathode compartments. However,
commercially available membranes are costly, and it
is generally attractive for MFC technology to be
low-cost. Thus, alternative materials are to be
sought. The objective of this study is to determine
the performance of cotton cloth and clay as
membrane separators in VBMFC using E. euginae
as decomposer. In addition, polarization curves will
be used to measure the optimal current, maximum
power, and internal resistance of the VBMFCs.
2 METHODOLOGY
2.1 VBMFC Design
The VBMFC assembly is shown in Figure 1.
Polycarbonate plastic was cut and assembled into a
rectangular vessel measuring 12 inches by 6 inches
with a height of 8 inches. The edges were then
sealed with hot glue and duct tape. Two carbon fiber
sheets measuring 6 inches by 8 inches each were
attached to the inner opposite sides of the vessel to
act as electrodes. Alligator clips were latched into
the top part of the carbon fiber to attach them to
copper wires. The other ends of the connecting wire
were connected to an external 2000 ohms resistor to
continuously polarize the set-up. The experimental
separators were attached as seen in Fig. 1. Two types
of separators were tested against a control: clay and
cotton cloth. Both types of separators were cut to the
size of the set-up cross-section and attached to the
containers. Moist loam soil was used to fill the
container. Triplicates were prepared for every
experimental set-up.
2.2 Experimental Set-up
E. euginae was obtained from a vermiculture farm in
Manila, Philippines. 50 adult worms were placed in
the anodic compartment for set-ups with separators,
and were scattered in the control set-ups (without
separator). Since the worms are sensitive to light, all
set-ups were covered with dark-colored cloth to
maintain a dark environment without suffocating the
worms. Good moisture was maintained by daily
spraying of distilled water, taking care not to flood
the set-ups.
The worms were fed starting on their second day
on the containers with fresh watermelon peels. They
were fed ad libitum, although care was exercised to
not let the watermelon peels decompose before they
were consumed. 5-g portions of peels were added in
every container until it is consumed.
Figure 1. Vermicultue-based microbial fuel cell
(VBMFC) assembly
2.3 Data Acquisition and Analysis
The voltage of the VBMFC set-ups were manually
measured everyday against a 2000-ohm resistance,
for 25 days, using a digital multimeter (RS Pro
RS14). From the gathered data, power can be
ICFEPP 2019 - International conference on Future Environment Pollution and Prevention
42