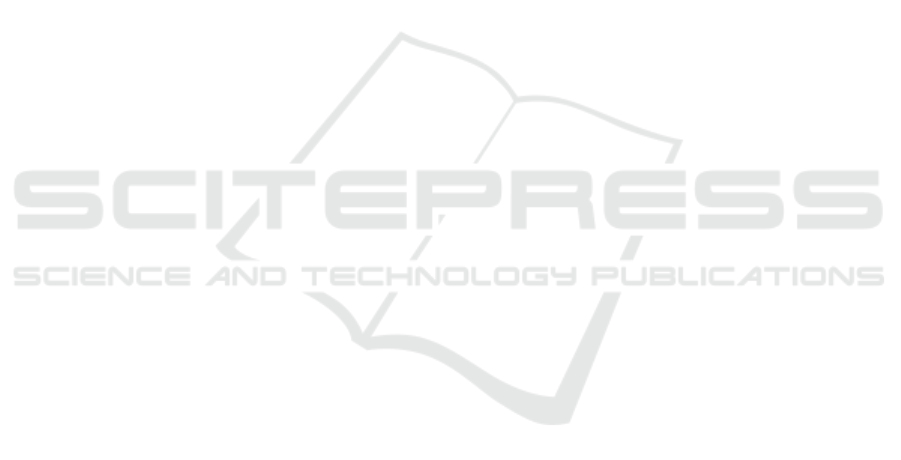
factors and the uncertain factors. The orthogonal
experiment method was used for analyzing the
uncertain factors. So the three uncertain factors are
studied and the levels of each factor are determined
for orthogonal experiment.
MBS model was used to simulate the railroad
freight car dynamic performance. The model was
validated by simulation and field test result
comparison. The operating condition are include
tangent track, R350m and R600m curves, they all
showed that the simulation model has a good
accuracy.
The worst operating conditions for Grade I
railroad and Grade III railroad were derived from
objective analysis. The variance analysis showed the
factors’ influence degree. Factor B is a very
significant factor for derailment coefficient, factor A
and factor C only have little effect on derailment
coefficient. But the three factors are very significant
factors for wheel unloading rate.
Based on the worst operating conditions and the
limit of derailment coefficient and wheel unloading
rate in China, we can simulate the different height of
combined center of gravity and get the permitted
height of combined center of gravity for railroad
cars can be increased to 2500mm in China.
Further work is underway to extend the MBS
modelling approach to deal with train simulation and
the braking and accelerating during operating. The
field test will be conducted to confirm the permitted
height of combined center of gravity for railroad
cars at last.
ACKNOWLEDGMENTS
This research was financially supported by the
National Key Research and Development Program
of China (Project No. 2018YFB1201402).
REFERENCES
AAR Open Top Loading Rules Manual (SECTION 1
General Rules for Loading All Commodities). (2010):
The Association of American Railroads.
Ahmed D. Shabana, Jalil R. Sany. (2001): A survey of rail
vehicle track simulations and flexible multibody
dynamics. Nonlinear Dynamics. Vol.26, pp.179-212.
Bangxing Shen, Changjun Wen. (2005): Experimental
design and engineering application. Beijing: Chinese
Metrology Press.
Chen Chao; Han Mei. (2012): Study of Railway Freight
Vehicle Body's Dynamic Model Based on Goods
Loading Technical Standards. International Workshop
on Information and Electronics Engineering, pp.3572-
3577.
Chengjun Zhang. (2009): Experimental Design and Data
Processing. Beijing: Chemistry Industry Press.
Field test about the permitted height of combined center of
gravity for double-deck container car. Beijing Jiaotong
University. 2007.
Field test about the permitted height of combined center of
gravity for tank car. Beijing Jiaotong University. 2008.
GB 50090-99. (1999): Code for design of railway line.
The ministry of China railways.
GB 5599-85. (1985): Railway vehicles-specification for
evaluation the dynamic performance and accreditation
test.1st ed. Beijing: National Bureau of Standard.
Haibo He. (1996): The relationship between height of
combined center of gravity of loaded car and operating
safety. Doctor Degree thesis. Beijing: Northern
Jiaotong University.
H.Г., Г.П., Lusheng Chen. (1965): Theory and methods of
loading and securing of railroad freight. Beijing:
China railway publishing house.
Hongnian Yan. (1991): Study of increasing the height of
combined center of gravity of loaded car. Doctor
Degree thesis. Beijing: Northern Jiaotong University.
Jenkins H.H. (1974): The effect of track and vehicle
parameters on wheel/rail vertical dynamic forces.
Railway Engineering Journal. Vol.3, pp.2-16.
Khajeh, MAZ; Shokrollahi, H. (2015): Study on the effect
of sol-gel parameters using the Taguchi technique to
achieve the optimal crystallite size and magnetic
properties of cobalt ferrite powders. Journal of sol-gel
science and technology. Vol.76, pp.271-278.
Mei Han, Yanling Wang, Liang Pang. (2007): Gravity
center height limit of loaded wagon based on safety
criteria for derailment coefficient. China Railway
Science. Vol.28, pp.106-110.
Nagesh, S, Murthy, HNN. (2015): Influence of nanofillers
on the quality of CO2 laser drilling in vinylester/glass
using Orthogonal Array Experiments and Grey
Relational Analysis. Optics and Laser Technology.
Vol.69, pp.23-33.
Renjun Wang, Jihua Chen, Hengchun Wang. (1982):
Problems about the center of gravity of loaded cars.
Sichuan: Railway society of Sichuan.
Saedon, JB, Jaafar, N. (2014): Multi-objective
optimization of titanium alloy through orthogonal
array and grey relational analysis in WEDM. 2nd
International Conference on System-Integrated
Intelligence - Challenges for Product and Production
Engineering. pp. 832- 840.
Sivam, SP, Michaelraj, AL. (2014): Statistical multi-
objective optimization of electrical discharge
machining parameters in machining titanium grade 5
alloy using graphite electrode. Proceedings of the
Institution of Mechanical Engineers Part B-Journal of
Engineering Manufacture. Vol.228, pp.736-743.
Suarez, Berta, Felez, Jesus. (2013): Sensitivity analysis to
assess the influence of the inertial properties of
railway vehicle bodies on the vehicle's dynamic
Research on the Permitted Height of Combined Center of Gravity for Railroad Cars
163