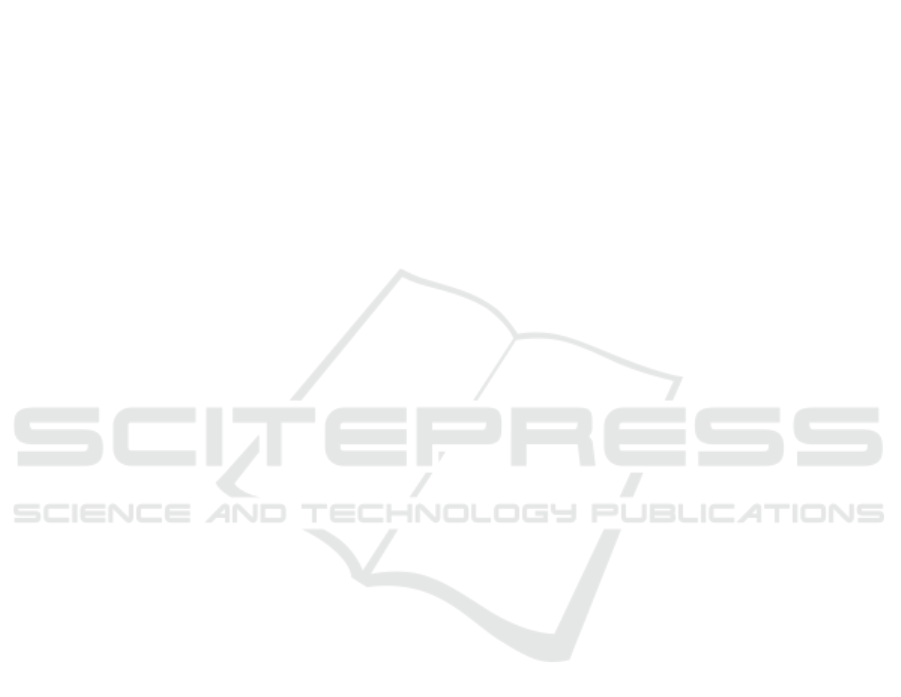
Design of Lubrication and Cooling Flushing Mechanism for Hand-
held Pneumatic Rock Drill
Yueyong Wang
1, 2, a
, Yimin Zhang
1, 2, b
, Zunling Du
1, 2
, Shijie Wang
1
1
School of Mechanical Engineering, Shenyang University of Technology, Shenyang, Liaoning 110870, China
2
Institute of Equipment Reliability, Shenyang University of Chemical Technology ,Shenyang, Liaoning 110142, China
Keywords: Pneumatic rock drill, lubrication mechanism, cooling flushing mechanism.
Abstract: The advantages and disadvantages of the traditional lubrication and cooling mechanism of Air-leg Rock
drill are analyzed. In order to solve the shortcomings of the traditional structure and the fatal disadvantages
of gas-water linkage failure and hammer washing, a new lubrication and cooling mechanism of Air-leg
Rock drill is designed. It prevents the backfilling of pneumatic rock drill in the normal working process and
at the end, improves the life of pneumatic rock drill as a whole, and has been verified in the customer site,
and achieved good results.
1 INTRODUCTION
Pneumatic rock drills used in mining, railway and
highway construction generally work in open pits,
tunnels or mountainous areas (Liu Enguo., 2013).
When the pneumatic rock drill works, there is
relative movement between the head and the rotating
sleeve and between the piston and the rotating nut. It
is easy to wear and tear (Chen Bingzhi, 1987).
Insufficient lubrication is one of the reasons that
often cause the failure of rock drill and parts damage
(Class B, Grade, 1979). Because of the change of
working condition of rock drill, water pressure also
changes, which can't guarantee that water pressure is
always lower than air pressure. In the water washing
mechanism of conventional pneumatic rock drill,
water pressure in water needle can't be adjusted.
Reverse irrigation during normal working process
and at the end of pneumatic rock drill will destroy
the lubrication system of pneumatic rock drill,
accelerate wear and tear, reduce the service life of
parts, and also reduce the machine torque. Drilling
efficiency decreases (Liu Jian, et.al, 2015).
2 CURRENT LUBRICATION
MECHANISM
Air leg rock drill needs lubricating oil for three
purposes: reducing friction, anti-corrosion and
sealing clearance. At present, pneumatic rock drill
has three parts that need lubrication (Yang
Wansheng, 2008): spline pair, brazing tail pair, head
and rotating sleeve matching pair. The lubrication
oil supply of pneumatic rock drill depends on the
exhaust of the front chamber of the cylinder, and the
residual air of compressed air containing atomized
oil passes through the friction pair parts mentioned
above. There are two ways of drainage (Cai Shumei,
2002):
One is the single drainage mode, and the
compressed air residual flow through the spline pair
gap, through a narrow way, flows through the
brazing tail pair and the head and the rotating sleeve
matching pair, leading to the atmosphere. It is
simple in structure, but when the rock drill is
operated under heavy load, because of less gas
flowing through and less atomized oil, it causes poor
lubrication and shortens the service life of the rock
drill.
The other is double drainage and compressed air
surplus through spline pair, which only leads to
brazing tail pair. In addition, a drainage air passage
is provided to lubricate the matching pair of the head
and the rotating sleeve. Its structure is complex and
the lubrication condition of the spline pair becomes
worse due to the reduction of compressed air surplus
flowing through the spline pair, which will also
shorten the service life of the rock drill.
172
Wang, Y., Zhang, Y., Du, Z. and Wang, S.
Design of Lubrication and Cooling Flushing Mechanism for Hand-held Pneumatic Rock Drill.
DOI: 10.5220/0008849001720174
In Proceedings of 5th International Conference on Vehicle, Mechanical and Electrical Engineering (ICVMEE 2019), pages 172-174
ISBN: 978-989-758-412-1
Copyright
c
2020 by SCITEPRESS – Science and Technology Publications, Lda. All rights reserved