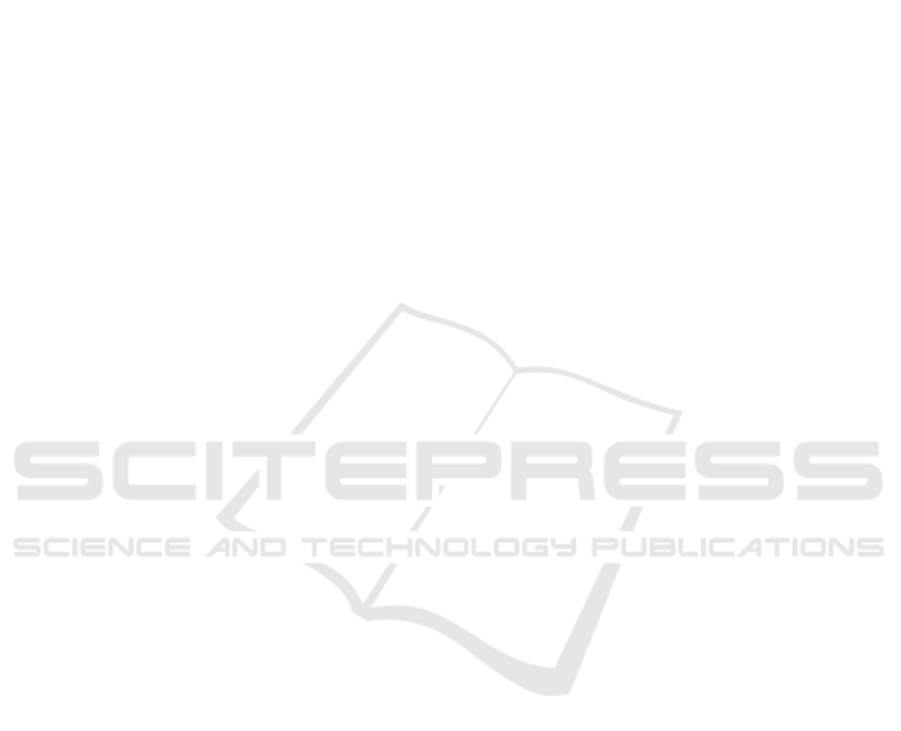
A Kinematic Design of 3-PRS Precision Compliant Parallel Platform
Zhiping Kong
1, 2, a
, Wei Zhang
1, 2, b
, Haibo Zhou
1, 2, c
1
School of Mechanical and Electrical Engineering, Central South University, Changsha, China
2
State Key Laboratory of High Performance Complex Manufacturing, Central South University, Changsha, China
Keywords: Parallel platform, Kinematics analysis, Large-stroke flexure joints.
Abstract: A kinematic design of the 3-PRS compliant parallel platform with wide-range flexure hinges is presented in
this paper. The manipulator is driven by the piezoelectric motors, which can show the superiority of parallel
platforms and large-stroke flexure hinges. First, taken into account the parasitic motions of the platform, the
kinematics solution is proposed. Then, the influence of parameters to the rotation capacity and relative
rotation error that are used to assess the quality of the revolute and spherical flexure joints. Also, the
reachable travel is observed by ANSYS Workbench. Finally, compare with the FEM and the theoretical
results by several different cases to ensure the efficiency of the kinematics model.
1 INTRODUCTION
High-precision positioning devices are often
required in different areas as scientific, medical and
communication fields for micro-system production
(Ruiz, et al., 2016). For these high-tech applications,
it is necessary to overcome the problems they
usually appear, as clearances, friction and wear,
which greatly affect the accuracy of the platform (Li
and Xu, 2007). A well-known solution for these
problems was put forward in (Bhagat U, et al., 2014),
which introduced the compliant machines with the
flexible hinges to improve the motion accuracy.
Parallel machine were first applied in the test of
tire by Gough, and later were introduced by Stewart
as the simulators (Stewart and D, 1965). Then the
Stewart structure began to be widely used in many
fields. Parallel manipulators with 6-DOF have many
advantages. Dong et al established a kinematics
model via analysing the stiffness model of the whole
6-PSS platform based on FEA method (Dong, et al.,
2005). Recently, parallel platforms with less than 6-
DOF have appeared in many different fields.
Rouhani et al developed a method on the basis of
elastokinematic analysis of a microhexapod
manipulator, in which the elastic deformation of the
flexure hinges was considered for the kinematic
analysis (Rouhani, et al., 2016). Meanwhile, It is
possible to develop 2-DOF mechanisms, as for
example the stage presented in (Huang and Dao
2016), where the stage with flexure elements allows
large displacement along x and y direction. Also, the
paper provides some useful steps for designing and
analyse by FEM. Many 3-DOF parallel manipulators
also have been designed and applied for relevant
areas. For example, the 3-UPU parallel robots with
pure translational motions in (Gregorio, et al., 1998),
other sample of this type is shown in (Liu, et al.,
2005), where the parallel manipulator HANA has
three DOF with one rotational and two translational
degree of freedom. Another 3-DOF mechanism is
presented in (Li,et al., 2005; Zhan, et al., 2005),
where the kinematic of the 3-RPS parallel
mechanism is analysed. Moreover, the necessary
steps to achieve a good design and characterization
are presented. Also 3-PUU mechanism with 2R1T is
proposed in (Wang, et al., 2016), where the mobility
analysis of the platform is carried out by the
reciprocal screw theory.
The 3-PRS parallel platforms were widely
designed and analysed in (Ruiz, et al., 2016; Li and
Xu, 2007; Jia, et al., 2016; Li, et al., 2016; Tsai, et
al., 2003). The 3-PRS parallel platform with large-
stroke flexure joints introduced in this paper. At
present, it is still a challenging task to solve the
design and kinematic problem with flexible joints.
For the mechanisms with flexible joints, they can
overcome many problems, but they also faced some
challenge, like the deformation of the joints and the
parasitic motions. Therefore, it is necessary to study
the design, kinematics and validate these compliant
parallel platform with flexible joints.
Kong, Z., Zhang, W. and Zhou, H.
A Kinematic Design of 3-PRS Precision Compliant Parallel Platform.
DOI: 10.5220/0008849403410346
In Proceedings of 5th International Conference on Vehicle, Mechanical and Electrical Engineering (ICVMEE 2019), pages 341-346
ISBN: 978-989-758-412-1
Copyright
c
2020 by SCITEPRESS – Science and Technology Publications, Lda. All rights reserved
341