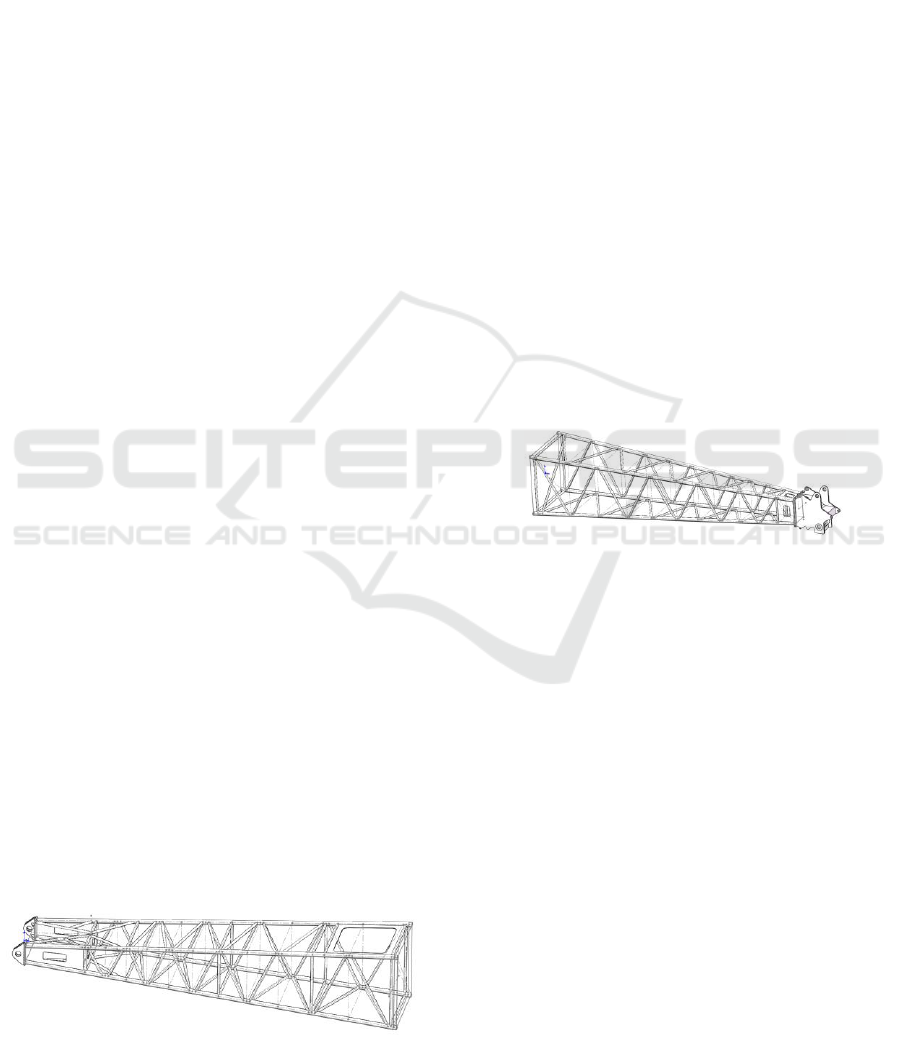
Finite Element Model Establishment and Strength Analysis of Crane
Boom
Linyan Zhang
1
, Hongliang Zhang
1, a, *
,Changguo Lu
1
1
Department of Computing,Yingkou Institute of Technology, Yingkou,China
Keywords: Crane Boom, Finite element analysis, Strength Analysis.
Abstract: This paper is devoted to the strength analysis of crane boom with Ansys software. The results of strength
analysis and theoretical calculation are compared and analyzed, and a method of using software to analyze
the strength of crane boom is discussed. Firstly, using SolidWorks software, the three-dimensional model of
each jib of the main arm of heavy crane is established by means of shell pulling, which is saved in x-t
format. Secondly, the three-dimensional model is imported into Ansys software, and the finite element
model of heavy crane boom is established by assigning attributes and meshing. Thirdly, the crane boom
priority model is constrained and loaded, and the static simulation is carried out. Finally, the simulation
results and theoretical results are compared and analyzed to verify the accuracy of the model (SINGH B,
et.al, 2011; TOMASZ G, et.al, 2011).
1 ESTABLISHMENT OF FINITE
ELEMENT MODEL OF CRANE
BOOM
1.1 Applying SolidWorks Software to
Build Three-Dimensional Model
Firstly, the three-dimensional model of crane boom
is established by using SolidWorks software. In
SolidWorks, all boards extract the middle surface,
and all tubes extract the axis to build a three-
dimensional model. The model of the crane boom
needs to be established, including the boom root, the
boom head, the completed 3m, 6m, 12m middle
boom. According to the requirement of the subject,
the structure size of the arm frame of the main arm is
determined. According to the size requirement, the
arm head and the arm root of the main arm are
drawn. The model is shown in Figures 1 and 2.
Fig 1. Arm Root.
Fig 2. Arm Head.
1.2 Introduction to Ansys Software
Ansys software is developed by American Ansys
Company. It is a finite element analysis software
which integrates structure, fluid, electric field,
magnetic field, sound field and thermal analysis. It
has corresponding interfaces with most software
(such as Pro/Engineer, Hypermesh, Adams, Nastran,
Ideas, etc.), and can realize data sharing and
exchange between them. The cell types used in this
paper are shell 63 unit, beam 188 unit, link 180 unit
and mass 21 unit.
1.3 A Simplified Scheme for Modeling
Process Using Ansys Software
Beam 188 beam element is commonly used in Ansys
to simulate the main chord and web members. This
element can define the cross-section shape and also
simulate the mechanics of the main chord and web
192
Zhang, L., Zhang, H. and Lu, C.
Finite Element Model Establishment and Strength Analysis of Crane Boom.
DOI: 10.5220/0008850001920196
In Proceedings of 5th International Conference on Vehicle, Mechanical and Electrical Engineering (ICVMEE 2019), pages 192-196
ISBN: 978-989-758-412-1
Copyright
c
2020 by SCITEPRESS – Science and Technology Publications, Lda. All rights reserved