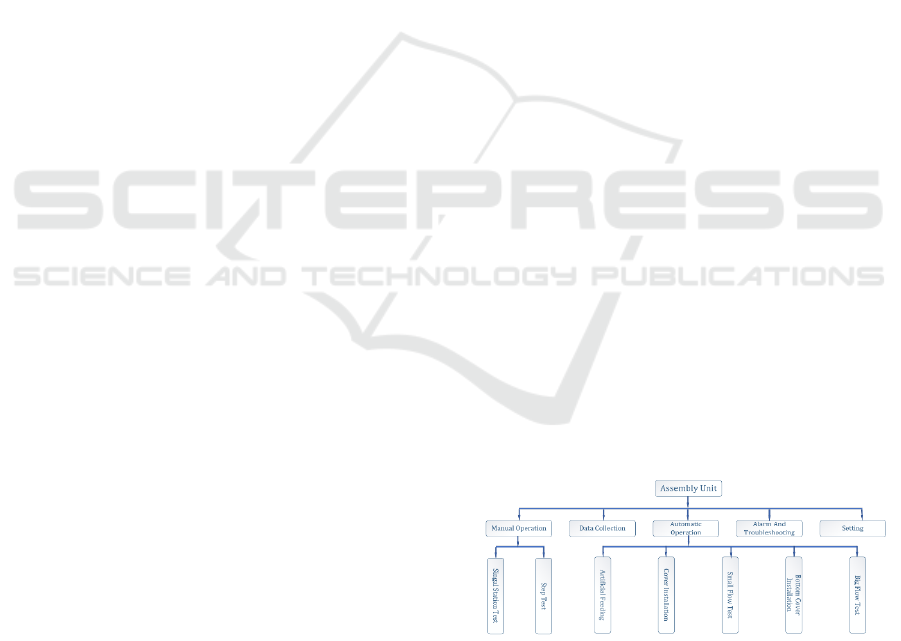
3.1 Section Headings
PLC is widely used in modern control systems due
to its small size, low cost, high reliability and strong
anti-interference ability. The system uses Siemens
S7-1200 series CPU, combined with I/O expansion
module, analog module, etc., and is programmed
with TIA PORTAL V14. The control system mainly
includes PLC controller, servo motor, electric
cylinder, cylinder and other actuators, and each part
is coordinated with each other to form an organic
whole, realizing automatic assembly and detection
(Suli Zhong, 2017).
3.1.1 Main Program Module
The main program module mainly includes a calling
program segment for six FC modules, an Ethernet
communication program segment of the upper
computer Labview, an error code program segment,
an emergency stop and an automatic interlocking
program segment, and a data transfer processing
program segment of the upper computer. Production
ratio and timing block, alarm-light-discharge
reminder. The FC1-FC6 modules respectively
correspond to the logic programming of six stations
(Wu Jianlong, 2018). The FC module contains the
main program, manual program, single-step program,
single-station program, automatic program and clear
automatic program of the station.
3.1.2 Hand Automatic Interlock and Process
Module
The module mainly includes program segments:
screen button interlock, hand automatic interlock,
output relay, sensor shielding, data single rotation,
time conversion block and alarm.
3.1.3 IAI Electric Cylinder Servo Drive
Module
The module mainly includes a program segment:
reading the position of the servo electric cylinder
and judging and calculating, finishing the writing
position information, basic control commands,
writing commands and positions (Zhao Dandan,
2018; Suli Zhong, 2017).
3.1.4 Sensor Conversion Module
The collected sensor data is processed, and then
logically programmed in the program, finally
achieving stable interaction with the machine, and
transmitting the required measurement data to the
host computer for display and saving.
3.2 Human-Computer Interaction Page
Design
The system adopts MCGS touch screen and upper
computer Labview as human-machine interface. The
touch screen mainly realizes operation and
monitoring of assembly process, realizes parameter
configuration of equipment, fault alarm and so on
(Wang Hongyi, 2017). The upper computer Labview
mainly realizes the display of product detection
curve and the processing of product quality
inspection data.
3.2.1 Main Program Module
The main interface mainly realizes the product
assembly status and data display. Basically contains
all the information about the product assembly.
Including production, the number and proportion of
qualified products or non-conforming products, real-
time test data of the product, assembly test time and
cycle, alarm display, product status display of each
station, including parameter setting, status
monitoring, manual operation, etc. Entrance.
3.2.2 Main Program Module
The parameter setting interface mainly sets the
parameters of each part of the system, including test
parameters, analog parameters, servo parameters,
delay parameters, I/O shielding, and function
shielding (Wu Jianlong, 2018). As shown in Figure
4 test parameter setting interface, the pressure, time
and flow parameters of the large and small flow test
are mainly set, and the pressure limit of different
stations is set.
Fig 3. Assembly system control module diagram
ICVMEE 2019 - 5th International Conference on Vehicle, Mechanical and Electrical Engineering
34