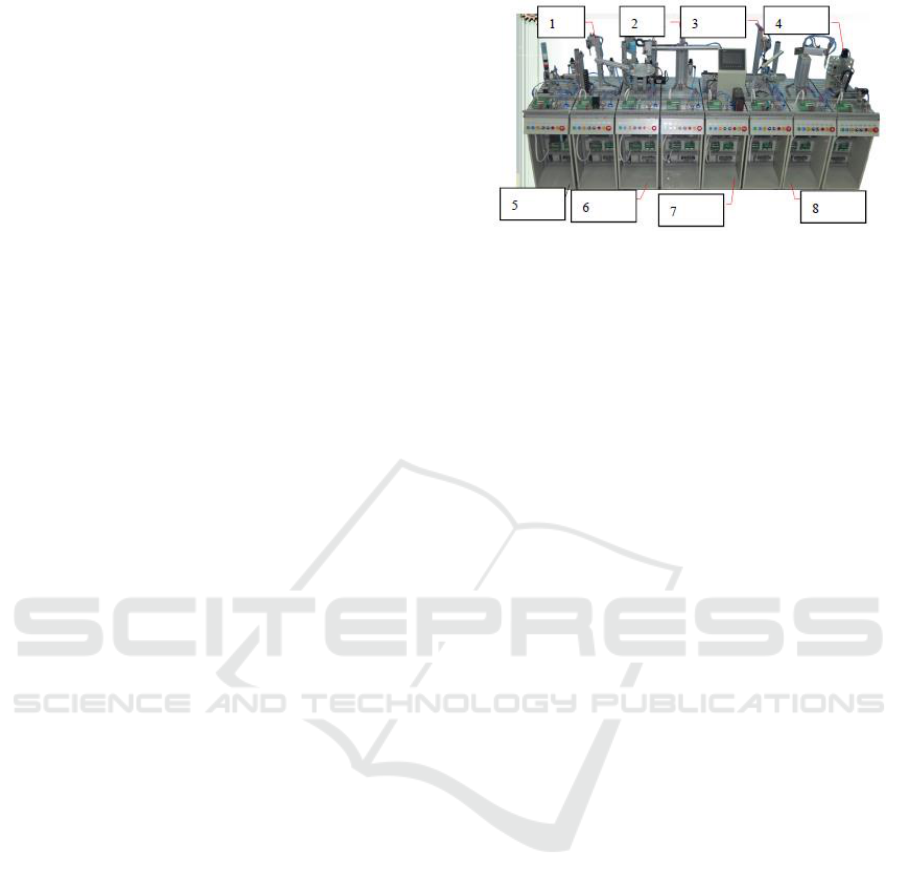
1.3 Domestic and International Status
of Teaching Flexible
Manufacturing System
The flexible teaching system in our country lags
behind many foreign countries. Universities such as
those in Japan, Singapore, the UK and Germany are
far ahead of us in the relevant allocation [6]. In
universities in these countries, flexible systems
range from simple to complex, allowing students to
experience operating platforms themselves. In the
process, students can also research, debug and
program on these advanced flexible systems. In
China, many of the country's top universities also
provide students with teaching systems, but most of
them are imported from Britain or Germany, and
needed a lot of money. Although some universities
are trying to develop relevant systems independently,
most of them still lack relevant teaching systems and
cannot provide relevant practical links.
2 RESEARCH CONTENT, KEY
TECHNOLOGIES AND
RESEARCH OBJECTIVE
2.1 Research Content
Modular flexible automatic production line training
system is one of the most typical mechatronics and
automation products. It is for vocational colleges,
technical schools, education training institutions and
developed, such as it is suitable for automation and
machinery manufacturing, mechanical and electrical
integration, electrical engineering and automation,
automation engineering, control engineering,
measurement and control technology, computer
control, automatic control, mechanical and electrical
engineering, mechanical design and theory and other
related professional teaching and training. It not only
specially designed for teaching, but also
strengthened various control technology and
engineering practice ability. The original system is
shown in figure 1.
1-detecting unit; 2-handling unit; 3-Extract installation
unit; 4-Ster; eo storage unit; 5-feeding unit; 6-processing
unit; 7-Sorting and conveying unit; 8-Operator unit
Fig 1. Schematic diagram of the original automatic
production line.
2.2 Key Technologies
(1) The system organically integrates mechanical,
pneumatic, electrical control, motor transmission,
sensing and testing, PLC and industrial network
control technology, with modular structure and easy
combination. Can complete all kinds of individual
skills training and comprehensive project training,
can also carry out mechanical parts installation and
debugging, pneumatic system installation and
debugging, electrical control circuit installation and
PLC programming, mechanical and electrical
equipment installation and debugging, automatic
control system installation and debugging, industrial
network control system installation and debugging
in one. It can meet the needs of practical teaching
and engineering training.
(2) Regardless of mechanical structure or control,
the system adopts unified standard interface, with
high compatibility and expansibility. With the rapid
development of industrial field technology, this
system can keep pace with the upgrading and
expansion of field technology and fully meet the
needs of practical training and teaching
(3)This system can exercise learners' innovative
thinking and practical ability. Learners can use this
system to carry out engineering training in
mechanical assembly, electrical design, wiring, PLC
programming and debugging, field bus construction
and maintenance, etc.
(4) Siemens PLC adopts Siemens PROFIBUS-
DP network communication, which enables the real-
time exchange of control information and state data
between various stations. It is equipped with 10.4-
inch, 256-color industrial color touch screen to
realize industrial control.
Research and Discussion on Flexible Automatic Production Line Upgrade System
379