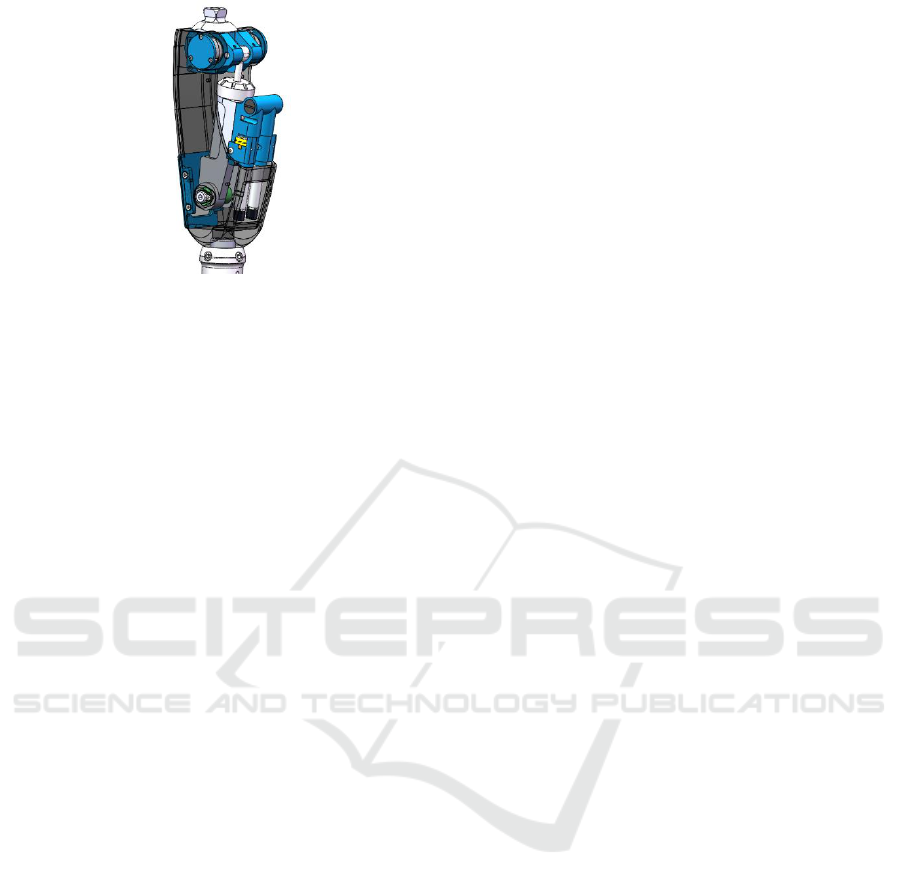
Figure 2. Knee prosthesis structure.
square of velocity (Staros & Murphy, 2013). When
the hydraulic oil flows through the small hole in the
circular tube in laminar flow state, the flow velocity
will increase instantly due to the sudden decrease of
flow area, resulting in turbulence. The relationship
between hydraulic damping force and flow velocity
change is shown in Fig. 1. This property makes it
possible to adjust the damping force of knee joint at
different speeds by changing the flow area of
hydraulic fluid. And then it changes the velocity of
hydraulic oil to create turbulence to achieve rapid
adaptation and control of damping torque. This is
very beneficial to the acquisition of the
physiological gait of the knee swing phase.
Therefore, uniaxial hydraulic knee joint structure is
selected (Hongliu Yu et al., 2009). In order to realize
the independence of intelligent knee flexion and
extension damping torque control, two motors are
used to control the corresponding plug valve
respectively. The flow area of the oil passage is
changed by the DC motor rotating plug valve, so
that the flow rate of the hydraulic oil is
instantaneously increased to form turbulent flow and
cause pressure loss. And then it controls the pressure
difference between the upper and lower chambers to
generate the damping force so as to achieve the
control of the knee damping torque at different
speeds. The overall knee structure is shown in
Figure 2. In order to ensure that the damping of the
flexion oil passage and the extension oil passage do
not affect each other, a check valve is placed in each
of the two oil passages. When the knee is flexed and
the hydraulic piston moves downward, the check
valve in the extension oil passage is closed and the
check valve in the flexion oil passage is opened.
And then the hydraulic oil can only enter the upper
chamber from the lower chamber through the flexion
adjustment oil passage. When the knee is extended
and the hydraulic piston moves upward, the check
valve in the flexion oil passage is closed and the
check valve in the extension oil passage is opened.
And then the hydraulic oil can only enter the lower
chamber from the upper chamber through the
extension adjustment oil passage. In order to assist
the knee extension, a spring is placed in the bottom
of the hydraulic cylinder. In each phase state, the
opening of the hydraulic damper valve is controlled
to adjust the flow rate of the hydraulic oil and then
control the knee damping torque. The magnitude of
the damping torque is proportional to the square of
the knee angular velocity.
(1)
M is the knee damping torque, V is the knee
angular velocity obtained by deriving the knee angle
signal, and C is the knee dynamic damping constant.
Five valve opening degrees, namely five different
damping constant values, are controlled during a
given walking cycle to achieve five phase
adaptations and adjustments. The damping value is
adjusted only when the gait phase transforms or the
period changes, and the damping constant is not
adjusted within a certain gait phase. The purpose of
the intelligent knee prosthesis adaptive control
system is to determine the damping constant which
is adapted to the phase state, that is, to control the
appropriate valve opening when the state transforms,
and then the physiological gait is achieved.
2.2 Dynamic Modeling of Lower Limb
Prosthetic System
The uniaxial knee prosthesis is connected to the
wearer's thigh stump through the prosthetic socket.
In order to design the knee controller, the thigh
motion experimental data is provided to the system
dynamics model to obtain the expected knee
damping torque curve. The damping torque curve
actually provided by the hydraulic damper is
obtained by adjusting the flow area of the hydraulic
damper in Matlab. The difference between the
simulation curve and the theoretical curve is
analyzed and compared, and the optimal flow area of
the hydraulic damper at different speeds is obtained.
The dynamic model is validated to provide
theoretical guidance for the control of the knee joint
damping torque.
The dynamic model of incorporating the
hydraulic damper into the lower limb prosthetic
system is shown in Fig. 3. The lower limb prosthetic
system of the amputated patient can be simplified
Establishment and Simulation of the Damping Torque Model of Hydraulic Intelligent Knee Prosthesis
205