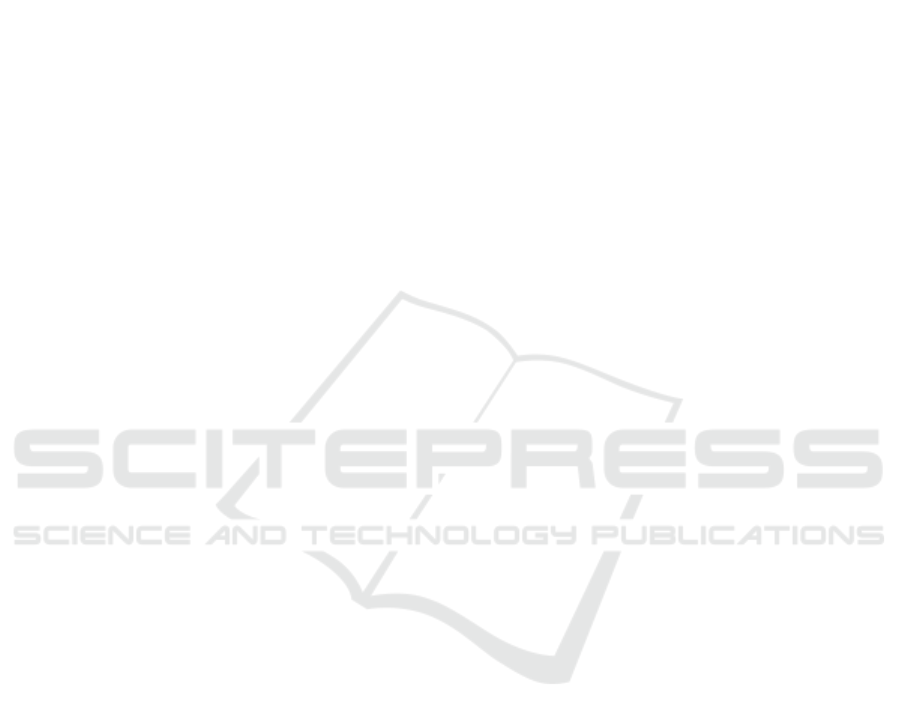
Dynamic Error Compensation Model of Articulated Arm Coordinate
Measuring Machine
Jiaqi Zhu
1, a
, Xugang Feng
1, b, *
and Jiayan Zhang
1, c
1
School of Electrical and Information Engineering, Anhui University of Technology, Ma’anshan 243032, China
Keywords: Neural network, Simulated annealing algorithm, Flexible arm coordinate measuring machine, Error
compensation.
Abstract: The error factors of articulated arm coordinate measuring machine (AACMM) are many and the
relationship between them is nonlinear, which is difficult to establish the model by traditional mathematical
modeling. This paper analyses the error sources, on the basis of parameter calibration, to select the angle
coding, thermal deformation and probe system as the research object and introduce coordinate values to
indirectly describe the remaining errors in the model. The BP neural network is used to build up the error
compensation model, connection weights of the neural network are optimized by the modified simulated
annealing (MSA) algorithm, which solves the problem that the neural network is easy to fall into the local
minimum and the susceptible to interference. The data samples are obtained through experiments, and the
test data are utilized to exercise model built. The experimental result demonstrates that the average value of
the single point repeatability error after compensation is reduced from 0.1782 mm to 0.0383 mm.
1 INTRODUCTION
The articulated arm coordinate measuring machine
(AACMM) generally having 6 degrees of freedom is
a non-orthogonal coordinate system measuring
device that simulates the structure of the human arm.
It has broad application prospects, not only can
complete online measurement and evaluation on the
assembly line, but also suitable for outdoor
measurement and occasions where the object tested
is inconvenient to move. The advantages involves of
easy portability, low price, flexible measurement,
large measuring range and practicality in the field.
Due to its series-space open-chain structure, the
measurement error has the characteristics of
accumulation, transmission and amplification during
the measurement process, ultimately leading to poor
overall performance of the measuring machine (Zhao
H N, Yu L D, Jia H K, et al, 2016; Feng X G, Xu C,
Zhang J Y, et al, 2016; Fedorov V G, 2008; Romdhani F ,
François Hennebelle, Ge M , et al, 2015; Xing H L, Bo C,
Zu R Q, 2013).
At present, the AACMM mainly reduces the
error by calibrating the structural parameters
according to calibration algorithm or external high-
precision equipment. For example, Santolaria J et al
established an error model based on Fourier
polynomial and estimated the parameter error of the
AACMM machine by using a spherical gauge with
14 spheres (SANTOLARIA J., AGUILAR J.J. YAGUE
J.A., et al, 2008). ACERO studied the feasibility of
laser tracker as a reference instrument in AACMM
parameter calibration (ACERO R., BRAU A.,
SANTOLARIA J., et al, 2015). Zheng D T established
the spatial point error model and spatial error
distribution of the AACMM by using the basic
theory of functional network and the principle of
vector machine (Zheng D T, FEI Y T, 2010).
However, there are many error factors in the
AACMM, and the structural parameters are only a
part of it. This paper analyzes the error sources in
the measurement space and applies a method based
on the improved simulated annealing algorithm to
optimize the neural network to model the multiply
error of the coordinate measuring machine. By
comparing the results, the validity of the
compensation model is verified.
2 ERROR ANALYSIS
The AACMM is composed of three joint arms and
one probe combined through six rotary joints in
210
Zhu, J., Feng, X. and Zhang, J.
Dynamic Error Compensation Model of Articulated Arm Coordinate Measuring Machine.
DOI: 10.5220/0008856502100216
In Proceedings of 5th International Conference on Vehicle, Mechanical and Electrical Engineering (ICVMEE 2019), pages 210-216
ISBN: 978-989-758-412-1
Copyright
c
2020 by SCITEPRESS – Science and Technology Publications, Lda. All rights reser ved