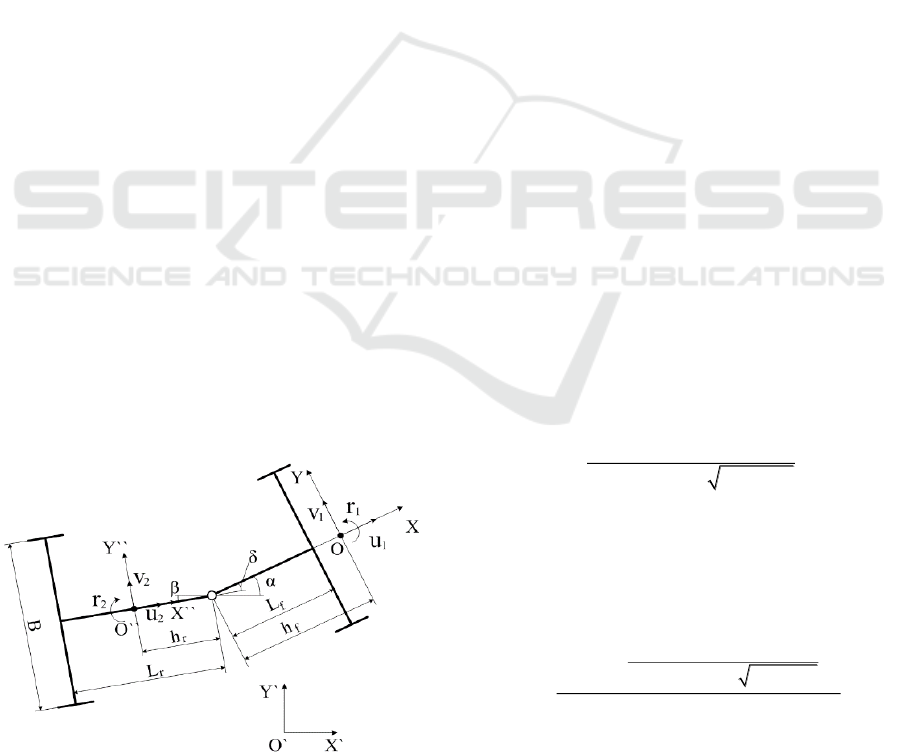
torque control strategy can not meet the
requirements of the vehicle's passing ability on a
complex roads, and it is prone to inconsistent
operation between the wheels, which consumes
additional power and wears the tires, resulting in
deterioration of steering and handling performance.
Therefore, it is necessary to put forward the driving
control strategy with sliding rate as the control target,
coordinate and control the driving force of each
wheel, and avoid the above situation. The control
strategy with consistent slip rate needs to calculate
the slip of each wheel by monitoring the vehicle
speed and the driving wheels ' rotational velocity,
and then control the torque to adjust the slip rate of
each drive wheel ,so that they tend to be
consistent(Shen Jun,Song Jian,Wang Huiyi, 2007).
And for full-wheel drive articulated electric-driven
vehicles, how to obtain accurate absolute speed is
also a key issue, and now there is no good solution
for such articulated vehicles.
Taking the steering condition of 35t wheeled
electric-driven articulated underground mining truck
as the research object, this paper establishes
kinematics and dynamics model of the vehicle, and
analyzes the relationship between every wheel’s
rotation speed and torque. The longitudinal
acceleration of the prototype is tested with the
acceleration sensor in real time and Kalman filter is
used to obtain the effective absolute speed of the
vehicle. A multi-body dynamics simulation platform
including steering wheel angle input model, wheeled
electric drive model and underground mine vehicle
virtual prototype model were established, and a joint
simulation of vehicle steering differential conditions
was carried out with the sliding rate controller ,
takes the equal slip rate as control target. And the
results of equal torque control strategy are compared
and analyzed.
Figure 1. Vehicle kinematic model.
2 MATHEMATICAL MODEL
ESTABLISHMENT
2.1 Kinematics Model
In order to accurately describe the slide rate of each
wheel, a vehicle kinematics model needs to be
established. As shown in Fig 1, the coordinate
system OXYZis an absolute coordinate system
fixed on the ground. OXYZ and OXYZare the
dynamic coordinate systems whose coordinate origin
is fixed on the center of mass of the front and rear
vehicle bodies respectively. X, X axles coincide
with the longitudinal axes of the front and rear
bodies, and δ denotes the angle between the front
and rear bodies.B denotes the distance between the
front and rear body, Lf denotes the distance between
the front wheel center and the hinged joint, Lr
denotes the distance between the rear wheel center
and the hinged joint, denotes is the distance between
the front body mass center and the hinged joint, and
hr denotes the distance between the rear body mass
center and the hinged joint. u1, v1, r1 denote the the
front car body’s longitudinal velocity, transverse
velocity, and transverse angle velocity around the Z
axis respectively, while u2, v2, r2 denote the the rear
car body’s longitudinal velocity, transverse velocity,
and horizontal angle velocity around the Z axis
respectively. The sum of r1 and r2 denotes the angle
change rate between the front and rear bodies, that is
(1)
From the motion relationship of each wheel,
regarding the steering angle as a known parameter,
1
2
(1 )
2 cot 2 1 cot
fl
fr
B
uu
LL
(2)
uflu
fl
, ufr, url, urr denote longitudinal velocity of
the center of the left front wheel, right front wheel,
left rear wheel and right rear wheel respectively.
And derive the slip rate expression of the wheels
1
2
(1 )
2 cot 2 1 cot
fr
fl
B
wR u
LL
S
wR
(3)
Sflu
fl
, Sfr, Srl, Srrs
fl
s
fr
denote the slip rate of the
left front wheel, right front wheel, left rear wheel
and right rear wheel respectively. w denote the
wheel angular speed to define the speed, and
Differential Control Strategy Research of Wheeled Electric Drive ADT Mining Truck
71