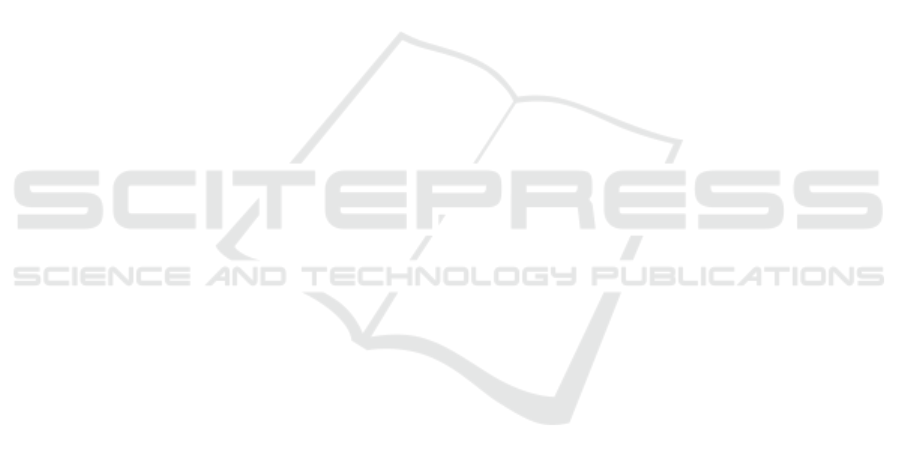
protective equipment.
• The workspace must be reachable and abandoned
quickly and securely through particular doors and
must be well maintained.
• An appropriate place for emergencies should be
available rescue tools to suit the needs.
Based on Government Regulation No. 11 Years
1979 about occupational safety in the purification
and processing of oil and Gas, there is OSH policy
in article 8 that the workplace should be clean and
well maintained. According to (Busyairi et al.,
2014) The company must understand that safety of
good work is to give employees a personal protective
equipment, pay attention to the condition of the
work tools, do maintenance tools, provide suitable
raw materials, Provide good lighting on the job site,
as well as cleanliness and maintained order. The
hygiene-well-maintained workspace makes the job
fun, easy, and fast. One of the ways to manage
the workplace is to move items that are no longer
needed and maintain cleanliness by storing goods in a
suitable place neatly for easy retrieval.
For the workplace must be supplemented with
proper illumination, by the terms of occupational
safety and health, allowing the workforce to see the
work meticulously, quickly and without unnecessary
effort. Adequate and well-arranged lighting will also
help create a safe and comfortable work environment.
The background of external human experiences
such as light, sound, temperature, color, and other
natural elements related to the environment, described
according to Potter & Perry in (Kristian et al., 2018).
According to Brewer and Sakai (Prayoga, 2014),
Symptoms include headaches, decreased intellectual
ability, concentration, and speed of thought. Poor
lighting can lead to eye fatigue by diminishing power
of work efficiency, mental fatigue, sore complaints
in the eye area and headaches around the eye, visual
impairment, and increased accidents. The potential
of poor lighting can prevent or reduce, workplace
lighting must be eligible to do the job. In-workplace
lighting improvements, results are seen directly in
improving productivity and reducing errors while
working. Direct light tends to be comfortable with
the number 200, which is a safe boundary of comfort
(Kristian et al., 2018).
Furthermore, the workspace must have proper
ventilation adjusted to the number of people, and
the air condition contained in the room. Indoor
air quality is primarily determined by the use of
the KOLOWA ventilation so that the movement of
air from outer space to the place becomes easy
(Vidyautami et al., 2015). Based on the research
conducted by Indrani in (Pandiangan et al., 2013) The
existence of ventilation on buildings in the tropics
is very important for thermal comfort and role in
supporting the increase of productive working time.
The dimensions of ventilation openings designed
according to (Pandiangan et al., 2013) are 24 x 1.25
meters for the northern wall and 23 x 1.25 meters
for the west wall and at a height of 3 meters above
the factory floor to be able to improve the comfort In
working mainly for production rooms using machines
that emit heat.
Also, the noise factor affects OSH so that workers
need personal protective equipment. Based on the
data from the WHO in (Dewanty and Sudarmaji,
2015) is known that the hearing loss due to noise is
the second most work caused by a lifetime accident.
The machine has noise with high strength sound.
The negative impact it brings to the employee is the
noise. This condition can result in hearing loss known
as Noise-Induced Hearing Loss. Hearing-impaired
due to noise or Noise-Induced Hearing Loss is a
hearing loss arising from repeated exposure, and
long can be chronic that is after working more than
10-15 years according to Adding in (Dewanty et al.,
2015). Research conducted by (Fithri and Annisa,
2015) several factors, namely environment influenced
noise disturbance, inspection, and human. Noise
level measurements are not routine and less thorough.
Noise level is due to lack of human resources to
perform noise measurements and when measurements
are carried out only in a few samples, not exhaustive.
While in terms of human, time is exposed to the noise
of workers too long, this is because noise does not
correspond to the level of noise that occurred expose
the length of the worker. Also, many workers ignore
personal protective equipment (PPE) on the grounds
of discomfort when working with PPE, and a long
working period for senior workers. Actual hearing
loss can prevent in the following ways:
• Using an ear protector
Using earplugs when working with high noise
exposure is the most significant preventative
effort. You can use an earplug or earmuff that has
an NRR (Noise Reduction Rate) value according
to the noise value in the work area or with the
largest NRR.
• Know the work area with high noise risk
Not all workers carry a Sound Level Meter (Noise
level gauge) or Noise Dosimeter (noise gauge for
personal monitoring) at work, so they do not know
the magnitude of the noise frequency in the work
area. Therefore, the company should install the
ear protective safety sign for a working area with a
high noise level exceeding 85 dBA. Also, workers
should even know which areas of work can pose a
ICoSEEH 2019 - The Second International Conference on Social, Economy, Education, and Humanity
142