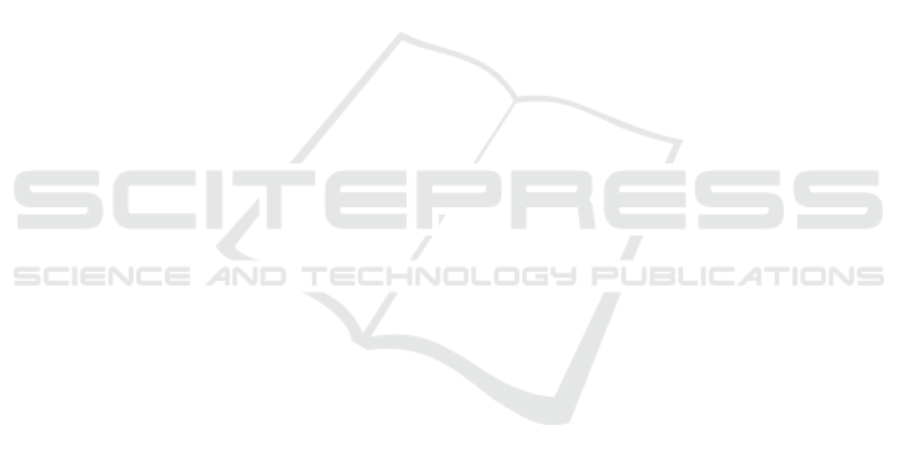
method to mitigate sand control. This is not surpris-
ing since frac-pack combines two processes, fractur-
ing and packing. Fracturing will create more paths
for hydrocarbon to flow and gravel packing will resist
sand to be produced. Thus, well productivity logically
will increase but still sand problem can be mitigated.
This thesis will mostly talk about frac-pack and its
modelling in M Well in Indonesia.
2 BASIC THEORY
History of Frac-pack
Frac-pack term is first popularized in the late of 1950
by Shell in Germany to define a completion method
which conducts fracturing before installing gravel
pack (Ellis, 1998). Another application of frac-pack
is conducted by Amoco in Hackberry, Louisiana, in
1964, which involves fracturing method in the current
sand control completion. At that time, the process is
called “hack fracs” (Ellis, 1998; Economides et al., ).
Not until the successful result of Tip-Screenout
(TSO) in North Sea Chalk formations. Prudhoe
Bay and Kuparuk Field (Alaska) in 1987, frac-pack
method is focusly developed. Over the years, frac-
pack is now utilized by combining TSO hydraulic
fracture, which creates short and high conductive
fracture, and gravel pack, which resist the proppant
from flowing back. The fracture created is meant to
bypass near-wellbore damages, which can give nega-
tive impact to hydrocarbon production.
However, before frac-pack is highly recom-
mended for sand problem mitigation nowadays, this
method apparently is used to be highly debatable.
This conflict is caused by concerns that frac-pack is
prone to problems, such as adding the completion cost
and contaminating the nearby water bearing sands.
This concerns can be tackled by the effectiveness of
frac-pack utilization in many fields in the world, starts
from Gulf of Mexico, America, Africa, Europe un-
til Asia Pacific, as stated by R.C. Ellis (Ellis, 1998;
Febriani, 2003; Hashemi and Gringarten, ). Until
now, the number of frac-pack utilization keeps in-
creasing all over the world and this shows a good
prospect of frac-pack in the future.
Frac-pack Mechanism
Frac-pack is originally a combination between frac-
turing and gravel-pack. The standard to measure a
successful frac-pack is the ability of this method to
mitigate sand problem and at the same time create
fracture to cover the skin made by the sand screens.
This fracture created is held open by utilizing prop-
pant pumped along with the fracturing fluid.
Tip-screen out fracturing is a method used to do
fracturing in weak and high permeability reservoir.
The goal is creating short and wide fracture with
length of 25 to 50 ft and width of 1 to 2 in by forcing
an early screen-out. Screen-out is a condition when
treatment area cannot accept proppant anymore, caus-
ing the pump pressure increase to its limit and prop-
pant cannot flow farther to the tip (Houchin and Dun-
lap, ; Odeh, 1980; Ott, 2003). This is occurred when
the fluid leaks off to the formation faster than pre-
dicted, caused by the high permeability of the forma-
tion. Screen-out is usually undesirable because a frac-
turing process with early screen-out cannot achieve its
designed fracture length and width. However, in frac-
pack, the fracture geometry is not the main goal. Frac-
turing process is conducted by following these stages:
• Spearhead stage
Also known as acid stage, this stage is meant to clear
debris which may still exist in the wellbore by using
a mixture of water and diluted acid, i.e. hydrochloric
acid. The result of this stage is a clear pathway for
fracturing fluid to flow into the formation.
• Pad stage
In this stage, the fracturing fluid will be pumped into
the well to frac the formation and initiate fracturing
of target formation. Due to its purpose to make frac-
tures only, proppant has not been mixed in the fractur-
ing fluid. Proppant/slurry stage In this stage, proppant
(sand) will be mixed with the fracturing fluid before
being pumped into wellbore. Proppant is used to keep
the fracture opened. Thus, it is meant to maintain the
enhanced permeability created by the fracturing in the
pad stage.
• Flush stage
In this stage, fresh water will be pumped into well-
bore. It is meant to flush out any excess proppant,
which may still exist in the wellbore. Tip Screen-out
fracturing process in each stage can be seen in Figure
1.
Frac-pack Benefits
Frac-pack offers many benefits, which impacts
to its popularity as sand control completion method,
which are:
• Lower average skin value: skin generated from
fracturing process can reduce the skin create by
the gravel pack only, leading to a better produc-
tivity.
• Support high production rate of production
• Longer life span. As proppant is filling the frac-
ture to the tip, the sand will be filtered from pack
at the tip first. This can improve the life span of
frac-pack because the sand pack around perfora-
tion is not affected too much.
ICoSET 2019 - The Second International Conference on Science, Engineering and Technology
292