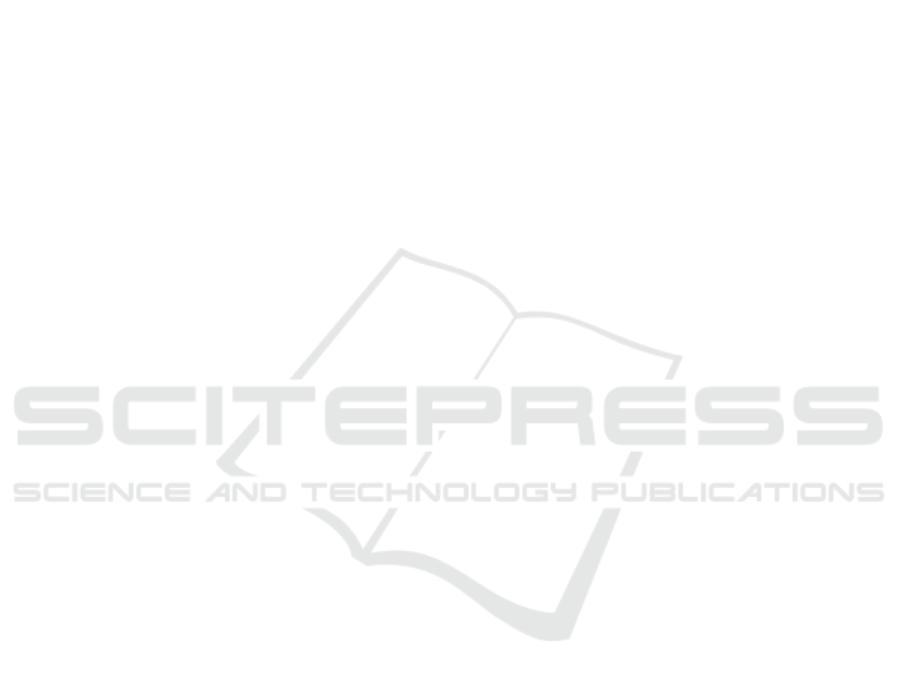
The Effect of Regeneration Time of Biomass Activated Carbon using Low
Temperature to Reduce Filtration Loss in Water-based Drilling Fluid
Mursyidah
1
, Nur Hadziqoh
1
, Arif Rahmadani
1
, Idham Khalid
1
and Hasnah Binti Mohd Zaid
2
1
Faculty of Engineering, Universitas Islam Riau, Pekanbaru, Indonesia
2
Fundamental & Applied Sciences Department, Universiti Teknologi Petronas, 32610 Seri Iskandar, Perak Darul Ridzuan,
Malaysia
hasnamz@utp.edu.my
Keywords:
Activated Carbon, Oil Palm Shell, Filtration Loss, Regeneration of Activated Carbon
Abstract:
Activated Carbon (AC) is a material that has porous structure and high surface area. If Activated Carbon has
long been opened to the air and interacts to the air, The surface of activated carbon can bind molecules from the
liquid or gas phases by van der waals force. It can affect decreasing the ability of activated carbon to reduce
filtration loss in water-based drilling fluid. The research has been carried out to increase the effectiveness
of AC as an additive in drilling process by thermal regeneration of activated carbon using low temperature.
This research using several samples that have various regeneration time by heated at 200
◦
C. The regeneration
times are for 0 minute (AC non- regeneration process), 30 minutes, 60 minutes, 90 minutes, and 120 minutes.
Scanning Electron Microscope (SEM) shows the surface morphology and porous size of the sample. The
results show that filtration loss decrease with addition time respectively 15 ml, 13.7 ml, 13.1 ml, 12.6 ml, and
12.1 ml. Regeneration process of activated carbon is one of the ways to reuse damaged activated carbon that
can control filtration loss until 12.1 ml.
1 INTRODUCTION
The Drilling fluid also called drilling mud is one of
important process in the petroleum industry. Some of
the petroleum industry faces challenges while drilling
processing. One of the challenges is how to con-
trol filtration loss in drilling operations. The way
to reduce filtration loss during the drilling process at
water-based mud can be added additive material into
drier mud to produce appropriate mud cake and can
control fluid loss (Paydar and Ahmadi, 2017). Some
materials used as additives to control filtration loss are
bentonite, calcium carbonate, boehmite, nano metal
oxide, nano zinc oxide, nano silica, carbon nanostruc-
ture (El-Diasty and Ragab, ).
Activated Carbon (AC) is an amorphous solid that
has high surface area and porous structure (Sivakumar
et al., 2012). It is widely used to adsorb the molecules
from liquid and gas phase. AC is used in many ap-
plication due to unique porous characteristic such as
water filter (Siong et al., 2013), nuclear (Foo and
Hameed, 2012), pharmaceutical (ALKHATIB, 2016),
agriculture (Nolan et al., 2015), gas and oil indus-
try (Mahto, 2013). The adsorptive properties of the
AC is needed to adsorb the adsorbate of the water-
based drilling fluid. The surface area of AC is excess
1000 m2/g that result have powerful adsorptive prop-
erties (Tadda et al., 2016). The smaller size of AC
increased the surface area. The quality of AC depen-
dent on the raw materials and the activation process.
AC is produced by various sources of carbonaceous
material such as coconut shell, sawdust, agricultural
activities waste (McLean, 2003).
The adsorptive properties of the activated carbon
can decrease when activated carbon has been long
opened in the air and interacts with the air. The
surface of activated carbon which is porous struc-
ture adsorb organic component and any impurities.
It is because of London dispersion force between
molecules. London dispersion force is a type of Van
der waals force that can bind activated carbon with
molecules from liquid or gas phases. The Van der
waals force is a weak electrostatic force between un-
charged molecules. The force have short range and
sensitive in interaction between the carbon surface
and the adsorbate molecules. The adsorption capacity
of activated carbon is finite. If the porous surface of
activated carbon adsorb any impurities from the air,
322
Hadziqoh, N., Mursyidah, ., Rahmadani, A., Khalid, I. and Binti Mohd Zaid, H.
The Effect of Regeneration Time of Biomass Activated Carbon using Low Temperature to Reduce Filtration Loss in Water-based Drilling Fluid.
DOI: 10.5220/0009385503220325
In Proceedings of the Second International Conference on Science, Engineering and Technology (ICoSET 2019), pages 322-325
ISBN: 978-989-758-463-3
Copyright
c
2020 by SCITEPRESS – Science and Technology Publications, Lda. All rights reserved