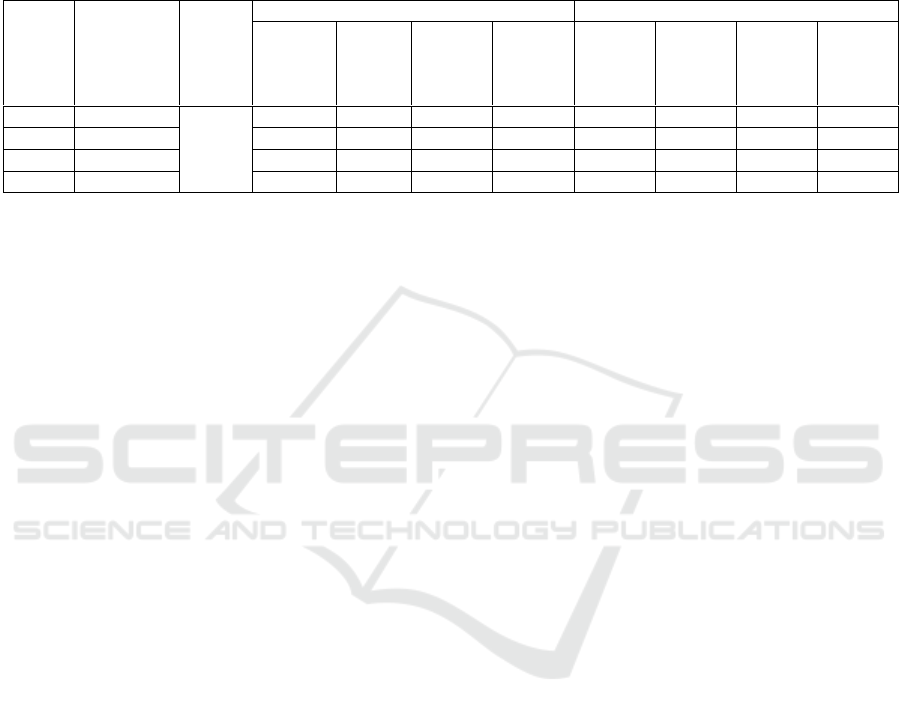
76.84. The same condition also applies for a larger
size dataset, which mostly generates less objective
function value, either in inspection task number or
CAMP task number, both using PSO-GRASP. For
1460-day planning horizon, using PSO-GRASP,
dataset G1 until G4 has objective function values
equal to 77.03, 77.35, 46.3, and 43.4, consecutively.
Based on these results, it can be concluded that
increasing the number of CAMP tasks does not
significantly change the objective function values
Table 6: The Results by Varying the Number of Iteration and Population Sensitivity Testing
Iteration /
Population
Limitation
The second experiment explored only Dataset G3
with 730 days planning horizon, as shown in Table 6,
by varying the number of iterations and population
Test13 uses 1000 iterations and 100 populations as
the baseline. Test 14 uses the same number of
iterations as the one in Test 13; however, the number
of populations of Test 14 is double the one of Test 13.
Test 15 and Test 16 have the same number of
iterations, 2000, but they differ in the number
population.
Increasing the number of population and the
number of iteration parameters escalates the CPU
time and mostly increases the objective function
values in both methods. In PSO-GRASP, doubling
the number of populations significantly increased the
objective function values with a 15% gap rather than
doubling the number of iteration parameters with only
a 5.14% gap.
Using PSO, increasing the number of iteration
parameters significantly increases the objective
function value with a 16.07% gap rather than that
increasing the population parameter with a 13.77%
gap and that increasing both iteration and population
parameters with 0.33% gap. Even though the number
of iterations and population parameters may affect
PSO performance, we cannot make any accurate
conclusion of CPU time usage because the objective
function generated by the PSO method is always
marked as an invalid solution and cannot be
implemented to the real system.
6 CONCLUSIONS
In this paper, we presented a MILP model for
optimizing aircraft maintenance scheduling
problems, considering the inspection check task and
CAMP task. Both tasks have to be considered by the
airline because it could affect the airworthiness of
their aircraft. Because of the NP-Hard nature of the
problem, we developed PSO-GRASP metaheuristic
methods to solve this problem in a reasonable time.
We tested the model using four randomly generated
datasets. We compared the metaheuristic models,
PSO, and hybrid PSO-GRASP, based on objective
function values and their CPU computational times.
The developed model could solve both small and
large-scale datasets. Using a larger scale dataset, the
result showed that the model could generate small
objective function value, but it needs longer CPU
time when tested in a similar parameter setting.
Statistical analysis shows that the PSO-GRASP
model is able to provide better performance than the
PSO method without hybridization based on the
objective function values. PSO cannot even provide a
valid solution to this problem.
By using the larger values of the iterative and the
population parameters, it makes PSO-GRASP work
better, but, in the PSO, the changes in these
parameters do not have any impacts on the solutions
made and still provide an invalid solution. Moreover,
by using these parameters or other parameters such as
the planning horizon, the computational times are
longer both for PSO and PSO-GRASP.
An interesting topic following this research is to
develop the exact algorithm, whether using Mixed
Integer Programming or Non-Linear Programming,
using either small or larger similar datasets.
Developing other metaheuristic methods, such as the
Genetic Algorithm, Tabu Search, or Simulated
Annealing, is also interesting for the next research
agenda for solving this aircraft maintenance problem.
ICONIT 2019 - International Conference on Industrial Technology
34