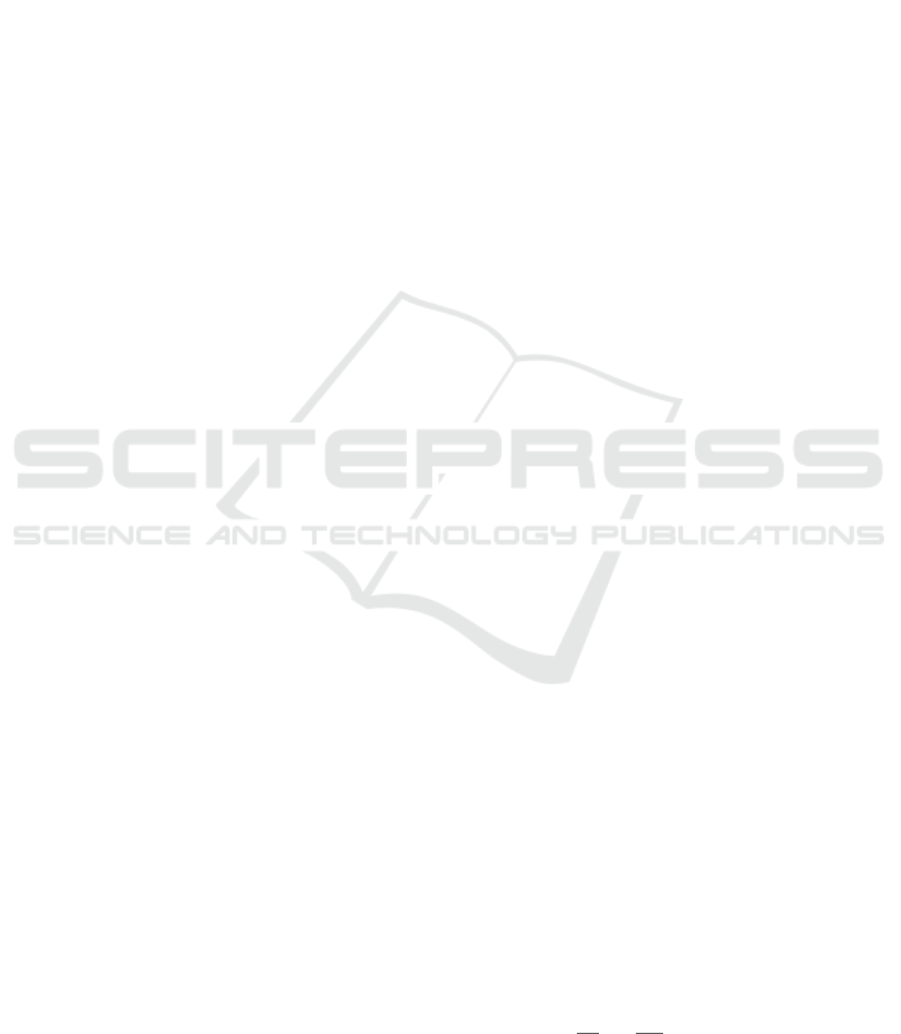
Simulation of a Proportional-Integral-Derivative Control for
Continuous Bioreactor
Rudy Agustriyanto, Puguh Setyopratomo, Akbarningrum Fatmawati
Faculty of Engineering, The University of Surabaya, Jl. Raya Kalirungkut, Surabaya, Indonesia
Keywords: Bioprocess control, simulation, PID controller, bioreactor.
Abstract: In a continuous bioreactor, feed is added, and the product flow is removed at a constant rate. The objective is
to maintain the system at a steady state with high product formation. This can produce a very productive
process, with a low operating cost. However, there are operational challenges, especially on an industrial
scale, because they require tightly controlled conditions and strong monitoring methods. For long operation,
the system suffers a higher risk of contamination. This paper investigated the PID (Proportional integral
Derivative) control strategy of a continuous bioreactor. Several tuning methods of PID controller were used
for controller parameters determination (i.e., Direct Synthesis, Ziegler-Nichols (Z-N), and Tyreus-Luyben
(TLC)). The results of the closed-loop simulation for servo (setpoint tracking) problems are presented in this
paper for each method and compared. The results showed that the three method works well qualitatively.
However, the process model of the system needs to be modified by introducing 5 hrs time delay, which is
useful in obtaining cross over frequency and to make PID possible in the Direct Synthesis method.
1 INTRODUCTION
An important aspect of bioprocess control is to lay
down real-time operations that are stable, less
susceptible to various disturbances, close to certain
circumstances, or desired profiles compatible with an
optimal operating condition (Dochain, 2008).
Bioprocess control itself can be defined as providing
an environment that is close to optimal so that
microorganisms can grow to reproduce and produce
the desired product. This includes providing the right
concentration of nutrients (e.g., carbon, nitrogen,
oxygen, phosphorus, sulfur, minerals), eliminating
toxic metabolic products (e.g., CO2), and controlling
important parameters (e.g., pH, temperature).
The dynamics model for a bioreactor system has
been available (Riggs and Karim, 2006). Based on
this model, Agustriyanto (2015) obtained the first-
order transfer function in the Laplace domain, which
then successfully controlled by the Proportional
Integral (PI) controller (2016). Simulation results of a
closed-loop system with PI controller tuned by direct
synthesis method have been presented (Agustriyanto,
2016).
The objective of this paper is to investigate the
Proportional Integral Derivative (PID) control
strategy of the above continuous bioreactor.
In the next section (Method), the system being
studied (continuous bioreactor) will be explained
first, followed by its open-loop transfer function in
the Laplace domain. PID control of the bioreactor
system will also be discussed and followed by several
tuning methods (Direct Synthesis, Ziegler Nichol,
and Tyreus Luyben).
Section 3 (Results and Discussion) mainly
presenting controller parameters and their closed-
loop simulation results.
2 METHOD
2.1 Continuous Bioreactor
The continuous bioreactor being studied is presented
in Figure 1 (Riggs and Karim, 2006). The model
based on first principle (mass conservation) for this
system is presented as follows:
Agustriyanto, R., Setyopratomo, P. and Fatmawati, A.
Simulation of a Proportional-Integral-Derivative Control for Continuous Bioreactor.
DOI: 10.5220/0009423201190123
In Proceedings of the 1st International Conference on Industrial Technology (ICONIT 2019), pages 119-123
ISBN: 978-989-758-434-3
Copyright
c
2020 by SCITEPRESS – Science and Technology Publications, Lda. All rights reserved
119