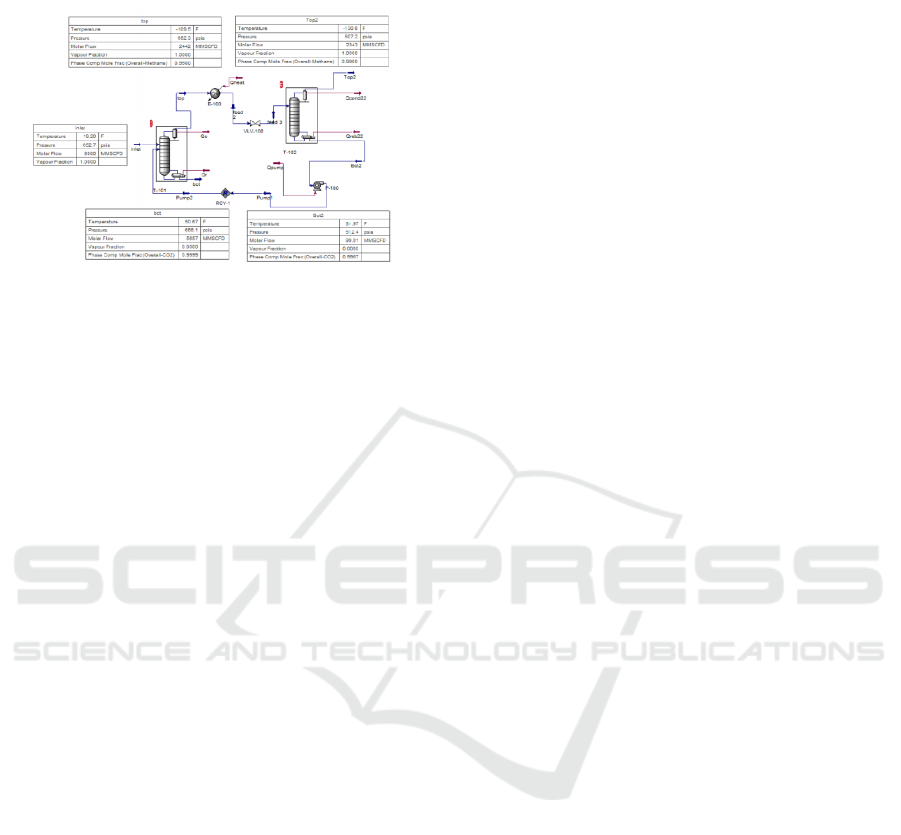
be seen in Figure 7.
Figure 7: Overall Design of Cryogenic Process.
To validate the results of the calculation of the dis-
tillation column, a reference is needed for compari-
son. In this study a reference to the size of the dis-
tillation column from the RCC Regenerator Column
was used, Balongan refinery with a diameter of about
9 meters and a height of more than 20 meters. Then
the feed gas rate is determined by the length of the
agreed contract. In this study the reference of feed
gas flow rate uses a reference from Nainggolan (2016)
with a flow rate of 8 BSCFD. From these references,
determining the size of the distillation column can be
done.
The variation in flow rate from 1-8 BSCFD pro-
duces a diameter of more than 11 meters. Whereas
the flow rate of 100-800 MMSCFD has the largest di-
ameter at the rate of 800 MMSCFD with a value of
10 meters. For the rate of 8 BSCFD, a diameter of
52.5 meters is produced, in the field this condition is
not possible so there is a need for a scenario to di-
vide the flow rate in the column in parallel, more than
one in each column. In the first column the maximum
rate that can be accommodated is 500 MMSCFD with
a diameter of 7.4 meters, while for the second col-
umn the maximum rate that can be accommodated is
610.4 MMSCFD from the results of the first column
with a diameter of 8 meters. The scenario is based
on the smallest condenser duty and reboiler duty to-
tal requirements is selected so that the first scenario
with column 1 (7.4 meters in diameter and 17.66 me-
ters in height) is obtained and 16 pieces are needed
column 2 (with a diameter of 8 meters and a height
of 22.38 meters) requires 4 pieces. From these results
for the next process, it is necessary to consider the ap-
plication of the distillation column in the field, with
the limitation of the location of the Natuna Gas Field
which is offshore resulting in the availability of land
and installation of the distillation column equipment
that needs to be reviewed.
Based on the designs presented above, it can be
proposed to be two main distribution/processing hub,
namely the platform based unit processing and on-
shore facility, connected with underwater pipeline. It
is worth noting that applying platform based process-
ing facility requires massive capital due to the size
of the processing facility, while using onshore facil-
ity would require very large pipe with high corrosion
potential. Further study should be done to assess the
economic and technical feasibility of these projects.
4 CONCLUSIONS
The choice of CO
2
separation technology from natu-
ral gas is based on several factors that are highly de-
pendent on the conditions and characteristics of the
gas field being reviewed.
Under pressure and gas flow rates based on the
case of the Natuna Gas Field, the cryogenic distilla-
tion process is chosen in the separation of CO
2
con-
tent at high flow rates, and is considered capable of
obtaining specifications of CO
2
content of less than
or equal to 1%.
In designing CO
2
separation using cryogenic dis-
tillation at a very high flow rate, a flow rate distri-
bution scenario in parallel with different columns is
needed to meet these needs due to limited location
availability.
With the content of 71% CO
2
and 29% methane,
the results of separation using two-column cryogenic
distillation obtained by the case of 8000 MMSCFD
flow rate obtained the number of the first column as
much as 16 with a diameter of 7.4 meters and height
of 17.66 meters, while the number of second columns
was 4 in diameter 8 meters high and 22.38 meters.
REFERENCES
Biyanto, T. R. (2007). Cascade control using soft sensor for
aldehide column energy saving. IPTEK The Journal
for Technology and Science, 18(4).
Burgers, W., Northrop, P., Kheshgi, H., and Valencia, J.
(2011). Worldwide development potential for sour
gas. Energy Procedia, 4:2178–2184.
Fenter, D., Hadiatno, D., et al. (1996). Reservoir simulation
modeling of natuna gas field for reservoir evaluation
and development planning. In SPE Asia Pacific Oil
and Gas Conference. Society of Petroleum Engineers.
IEA (2017). WEO 2017.
Kohl, A. L. and Nielsen, R. (1997). Gas purification. Else-
vier.
Liu, X., Jin, D., Wei, S., Wang, Z., An, C. G., and W.
(2015). Strategies to enhance CO2 capture and sepa-
A Solution to Increase Natuna D Alpha’s Resource Utilization by Cryogenic Distillation: Conceptual Design Sensitivity Study
347