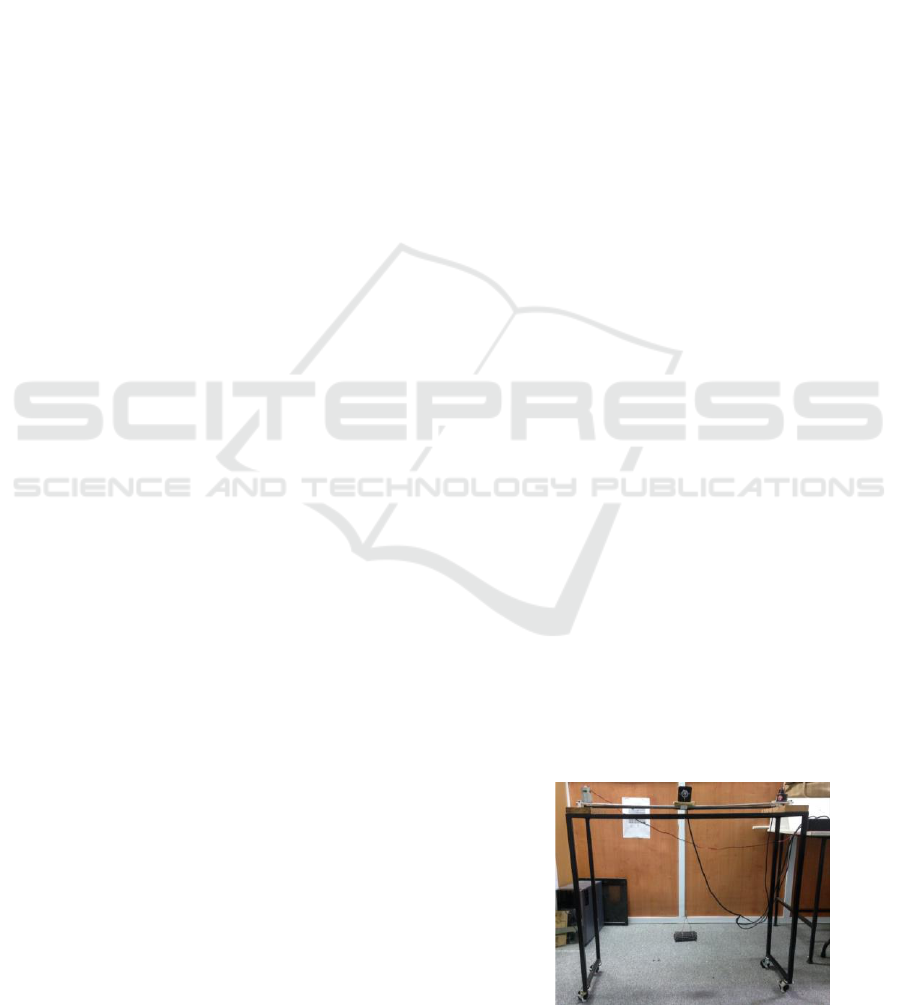
Comparison of Anti-sway Gantry Crane Control System based on
PID and Fuzzy Logic Control
Primarratna Setiyopamuji, Fuad Fahmi, Porman Pangaribuan, Erwin Susanto
and Agung Surya Wibowo
Electrical Engineering Department of Telkom University, Telekomunikasi Street Number 01, Bandung Regency,
Indonesia, 40257
Keywords: Anti-sway, Gantry Crane, Fuzzy Logic, Proportional-Integral-Derivative.
Abstract The development of industry involves automation as the core of the manufacturing process and material
handling. One of the automatic applications called gantry crane used for things moves from one place to
another place. The problem arises when the gantry crane makes a movement to carry some loads. The cable
which connects the crane and load may make sway continuously. This sway is unwanted because it will be
dangerous to people or the environment near the gantry crane. Moreover, the load could be dropped, or the
worse thing is the cable could be broken. As a result of that, the sway should be eliminated faster. This research
purposed to design an antisway system that will reduce or make the sway is gone quickly. PID and Fuzzy
Logic are used as the method of the controller for the implementation of anti-sway. The result showed that
the sway could decrease in two aspects. The first is the duration of sway reduced from 158,35 to 3,885 second
by fuzzy logic and from 82 to 7 seconds by PID. The second is maximum sway was also reduced from 17,52
to -8,09 by fuzzy logic and from -12,59 to 4.22 by PID.
1 INTRODUCTION
Gantry crane is used in many industries or harbor to
do load movement easily. The conventional crane
sometimes is not safe because there is a way which
makes an operator must be careful to control the crane
manually. The sway is hardly attenuated, and it
becomes a challenging problem for engineers on how
to design a control system that works for reducing the
sway in gantry crane. The system which can decrease
and attenuate the sway is called anti-sway. It will run
automatically together with control of crane's
position.
Some methods have been developed to handle or
to implement anti-sway. There are fuzzy logic
controller [1], [2], and PID [3]. However, we do not
believe in the assumption that a controller method is
better than another method. So, this research would
compare two popular methods applied in the anti-
sway system. In the experiment, the response of the
sway degree would be showed and plotted with
different parameters and conditions.
2 GANTRY CRANE
Cranes are usually used for moving heavy goods
transportation in harbor, manufacture, and high
construction building project. One of the types of
cranes is a gantry crane. That has two holders on both
sides and one rail between the holders. Most of the
gantry cranes are operated manually, which may
swing the heavy load like a pendulum. The swing
needs to be balanced quickly so that the sway will not
be harmful, and the goods are moved faster. Figure 1
below shows the prototype of the gantry crane used
in this research.
Figure 1: Prototype of Gantry Crane.
Setiyopamuji, P., Fahmi, F., Pangaribuan, P., Susanto, E. and Wibowo, A.
Comparison of Anti-sway Gantry Crane Control System based on PID and Fuzzy Logic Control.
DOI: 10.5220/0009490302650271
In Proceedings of the 1st International Conference on Industrial Technology (ICONIT 2019), pages 265-271
ISBN: 978-989-758-434-3
Copyright
c
2020 by SCITEPRESS – Science and Technology Publications, Lda. All rights reserved
265