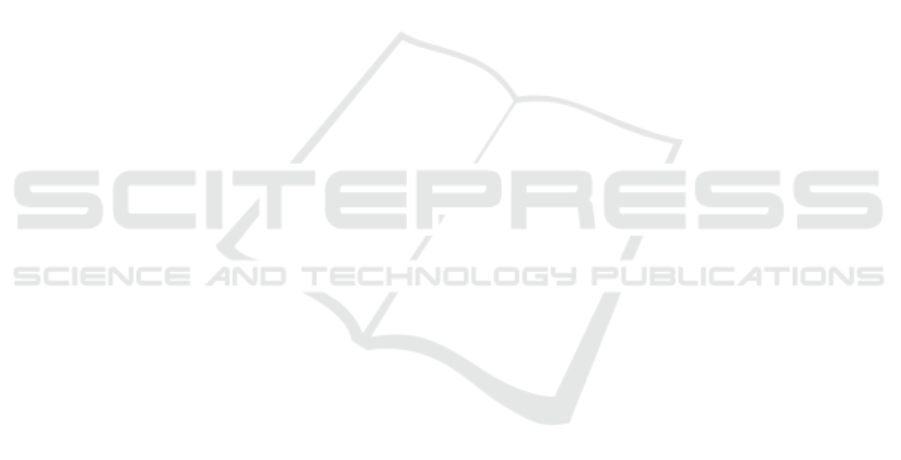
the carry over process in Telkom is carrying only the
open commitment documents without the budget so
it will consume the allocated budget in the next fis-
cal year. Though the SAP offers a carry over function
that carries the budget for commitment and residual
budget, however, it didn’t meet the needs of the user.
Hence, the user needs to perform the return budget
process, which is not effective. Moreover, because
while carrying items, the budgets are still attached the
user found it difficult to distinguish between the carry
over and carry forward because the system considered
these two budgets entering the same budget type af-
ter the carry process. Those above-mentioned issues
cause the delays of the year-end closing.
Based on those issues that have been described
in the previous paragraph, further research is needed,
mainly in the funds management module and its func-
tions so that the company can optimize its business
processes. Therefore, the existing business processes
need to be redesigned based on the requirement of the
company. The right methodology for this research is
SAP Activate, a methodology with a unique combi-
nation of SAP best practice, methodology and guided
configuration so the company can build the systems
faster and run them simply. The right solution to
resolve the problem in PT. Telekomunikasi Indone-
sia, Tbk is by redesigning the budget carry over pro-
cess in the funds management module using the SAP
methodology.
2 LITERATURE REVIEW
2.1 Enterprise Resource Planning
(ERP)
According to Surjit, Rathinamoorthy & Vardhini, En-
terprise Resource Planning (ERP) is a business pro-
cess management that gives the company to use a
system that is integrated with various applications
to regulate their business and automate functions re-
lated to technology, services, and human resources
(Surjit et al., 2016). According to Ganesh, Mohap-
atra, Sivakumar & Anbuudayasankar, Enterprise Re-
source Planning is a tool that can help the company to
plan, schedule and integrate suppliers and customers
(Ganesh et al., 2014). Enterprise Resource Planning
according to Elbardan & Kholeif is a management
system that contains a set of integrated software that
is used to integrate all of the business functions that
exists in the company (Elbardan and Kholeif, 2017).
From all of the ERP definition mentioned above, it
can be concluded that Enterprise Resource Planning
is a system that helps the company both to integrate
the main processes and coordinate information be-
tween business area so that they can support the busi-
ness processes to be better in the future. ERP sys-
tem has the capacity to simplify processes that are
slow and time-consuming in the company (Parven and
Maimani, 2014).
2.2 Systems, Applications, and Product
(SAP)
SAP stands for ”System, Applications, and Prod-
ucts in Data Processing”. SAP is a software that is
tightly integrated with each other so that every trans-
action that runs in a module will automatically affect
other related modules (Sampat, 2015). SAP supports
the company’s main business processes and functions
(Boeder and Groene, 2014). According to Okung-
bawa, SAP is used by nearly 500 companies around
the world as a solution for processing operational data
and making real-time reports so it can help manage-
ment levels to make good decisions appropriately and
enable them to manage the company’s business pro-
cesses effectively and efficiently (Okungbowa, 2015).
The main goal of SAP is to improve and simplify
internal business processes which are sometimes re-
quire reengineering process (Junnarkar and Verma,
2017). SAP allows the company to run modules in-
dividually and adjust the system according to the re-
quirements of the company (Khan, 2017).
2.3 Material Management
The Material Management module is a part of the lo-
gistics system in SAP that is connected with Produc-
tion Planning, Plant Maintenance, Warehouse Man-
agement, Sales & Distribution and Logistics Execu-
tion (Sedgley and Jackiw, 2002). This module is de-
signed to provide information, tracking and managing
the materials that are being moved, stored and sent
outside the company (Ahmed, 2014). According to
Jost, the following is an explanation of several pro-
cesses in Material Management that will be used in
the carry over process:
1. Purchase Requisition
This document is a request from a particular de-
partment to the purchasing department to provide
a certain amount of services or materials.
2. Purchase Order
This document is sent to an external business part-
ner that contains material details and quantities.
ICCETIM 2019 - International Conference on Creative Economics, Tourism Information Management
122