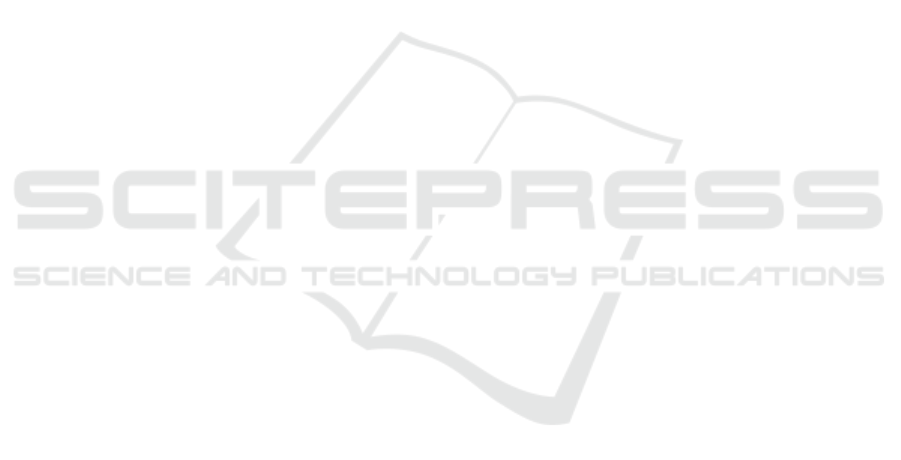
3. The Solar panel that uses the dual-axis tracker
method generates a higher power output of 9.4
W compared to 6.8 W generated by static method
which gives a difference of 2.6 W. This is due to
the static solar panel method not always perpen-
dicular to the sun, this problem could be solved
using the dual-axis tracker solar panel to ensure
the solar panel always perpendicular to the sun.
REFERENCES
Babaa, S. E., Armstrong, M., and Pickert, V. (2014).
Overview of maximum power point tracking control
methods for pv systems. Journal of Power and En-
ergy Engineering, 2:59–72. Published Online August
2014 in SciRes.
Duarte, F., Gaspar, P. D., and Gonc¸alves, L. C. (2011). Two
axes solar tracker based on solar maps controlled by
a low-power microcontroller. Journal of Energy and
Power Engineering, 5(7):671–6.
Elsherbiny, M. S., Anis, D. W. R., Hafez, D. I. M., and
Adel R. Mikhail, D. (2017-09). Design of single-axis
and dual-axis solar tracking systems protected against
high wind speeds. International Journal Of Scientific
& Technology Research, 6(09). ISSN 2277-8616.
Femia, N., Lisi, G., Petrone, G., Spagnuolo, G., and Vitelli,
M. (2008). Distributed maximum power point track-
ing of photovoltaic arrays: Novel approach and sys-
tem analysis. IEEE Transactions on Industrial Elec-
tronics, 55:2610– 2621.
IEEE (2015). Definition of iot. https://iot.ieee.org/
about.html. [Online; Accessed 03-May-2015].
Mansour, S., Anis, W., and Ismail, M. (2015). ISSN 2277-
8616, VOLUME 4, ISSUE 05.
Notosudjono, D. and Adzikri, F. (2018). Renewable Energy
Technology. UNPAK PRESS, Bogor.
Perera, A. Z., Christen, P., and Georgakopoulos, D. (2013).
Context aware computing for the internet of things: A
survey”. IEEE Communications Surveys & Tutorials,
16(1):414–454.
Prinsloo, G. J. and Dobson, R. T. (2015). Solar tracking.
stellenbosch: Solarbooks. Cambridge 2015 Book Edi-
tion, ISBN: 978–0–620–61576–1.
Ramadhan, M. G., Muttaqin, A., and Abidin, Z. (2018).
Maximum power point tracker (mppt) as a solar
cell power maximization method for solar boat eco-
charging. Seminar Nasional Teknik Elektro Universi-
tas Brawijaya.
Roth, P., Georgiev, A., and Boudinov, H. (2005). Cheap
two axis sun following device. Energy Conversion and
Management, 46(7-8):1179–92.
Takpor, T. O., Atayero, A. A., and Members, I. (July). In-
tegrating internet of things and ehealth solutions for
students’ healthcare. In Proceedings of the World
Congress on Engineering 2015 Vol I WCE 2015, vol-
ume 1, pages – 3,, London, U.K.
Solar Power Plant Tracker Upgrade and MPPT Control with Internet of Things
223