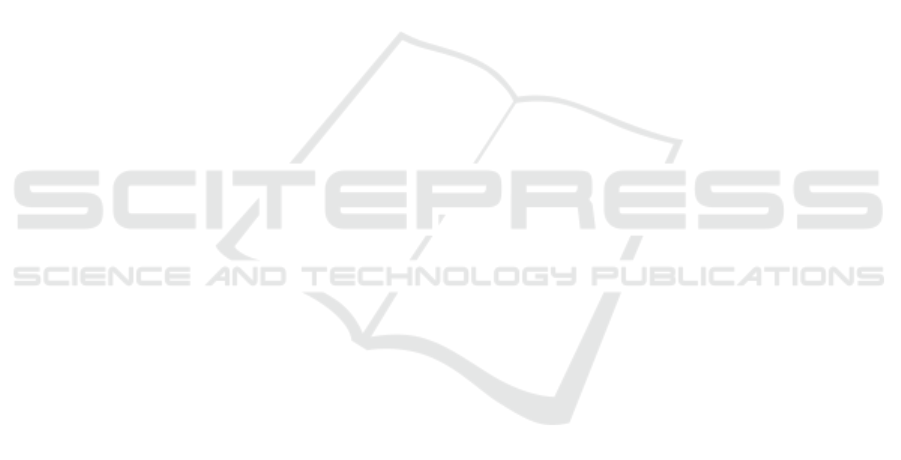
parts was re-designed from their initial geometry with
the objective of enhancing producibility to achieve ef-
ficient high volume manufacturing rather than proto-
typing. The results show that designing with automa-
tion in mind made the assembly process easier for
robots - but also humans.
As seen in Fig. 4 the landing gear has a square
shape and locks in place with the hub through a snap-
connection, rather than a threaded assembly. Parts
assembled in fixtures were designed with embedded
features leading to a kinematic coupling between part
and fixture during the process. The general feature
across all of the parts was to embed flat faces leading
to a simpler finger design and a higher rate of success-
ful manipulations.
The overall framework proposed in this paper was
tested on the drone motor assembly use case. The
production engineers used the front-end of the fin-
ger design framework to specify the requirements and
give information about the task specifying how the
parts are introduced to the cell, what is the task com-
prised of, grippers and robots used for the task, mate-
rials, etc. Some of the requirements given through the
front-end interface are:
• The parts arrive in the robot cell in fixtures where
their position is semi-defined.
• The parts have to be aligned in the finger to en-
sure a stable pose of the object for the following
assembly process.
• The finger acts as an fixture onto which the rest of
the sub-assembly parts have to be assembled.
• The robot has to perform various tasks, therefore
the fingers have to be exchanged when another
task arises.
• The fingers have to be manufactured through ad-
ditive manufacturing.
As mentioned before the main idea of the front-end is
to gather user information related to the task, which
has to be handled. One of the functionalities is also
the ability to upload the 3D representations of the ob-
ject and visualize how they can be grasped. This func-
tionality can be customized by the user: the user con-
figures the view (see Fig.3, web application data) until
he is satisfied with the pose of the object placed in the
mock-up gripper. This information gives the designer
using the back-end the information on the grasp pose
of the object in relation to the gripper fingers. The in-
formation is compiled and used in the back-end finger
design and evaluation procedures.
To design the suitable finger shape for the pre-
sented assembly task, we have utilized our previ-
ously introduced gripper simulation framework (Wol-
niakowski et al., 2018). The finger design framework
is based on the Open Dynamics Engine (Smith, 2005)
and a visual interface provided by RobWork (Ellek-
ilde and Jorgensen, 2010).
Furthermore, the requirement presented by the
end user is to use the fingertip exchange mechanisms
(Kramberger et al., 2019) in order to perform quick
changeovers between fingertips dedicated for differ-
ent part handling. In addition we had access to a
manual CAD fingertip designed for handling the mo-
tor assembly, by an expert engineer. Therefore, we
can compare the manual CAD design with the design
produced by the presented framework. A comparison
between the two designs is shown in Fig. 6.
The hand and the design made with the back-end
were furthermore tested in simulation in order to es-
tablish the range at which the fingers are able to com-
pensate the possible position uncertainty introduced
by the object handling before the assembly task. In or-
der to define the uncertainty and compensation map-
ping, grasps were executed in simulation with increas-
ing offset from the nominal pose along all three prin-
cipal position and orientation axis. In total 100 grasps
with offsets from the nominal prose per axis were exe-
cuted in the range from (σ
pos
= −10mm to 10mm and
σ
ang
= −5
◦
to 5
◦
). The combined simulation experi-
ment results for the two finger designs are presented
in Fig. 5. The figure is divided into two parts. The
left side represents the position and the right side the
orientation part of the conducted tests (three plots for
each of the position and orientation axes respectively)
represent the grasping success and reliability distribu-
tion for the two designs tested in simulation .
For each of the finger designs, the experiments
were executed in six batches, where in each batch the
object was displaced from its nominal pose defined by
the user along one of the axes. Each individual plot in
Fig. 5 shows the grasping success evaluated along the
individual axis (x, y, z, Rx, Ry, Rz). The solid green,
yellow and red lines represent successful, misaligned
and failed grasps for the hand designed fingers respec-
tively. Whereas the dotted blue, cyan and black lines
give the indications of the before mentioned grasp-
ing evaluation indices related to the design made by
the presented framework in this paper. The results ac-
quired with the design framework show a boundaries
of the alignment capabilities which are easily to dis-
tinguish. In comparison, in the hand design results the
boundary outlining the successfully aligned grasps is
more dispersed and cannot be easily defined.
For instance, with the experiments conducted in
the roll and pitch direction with the hand design, it
can be seen that finger design is not able to com-
pensate for the pose uncertainty repetitively, therefore
the success measures e.g. green are dispersed along
Robotic Finger Design Workflow for Adaptable Industrial Assembly Tasks
73