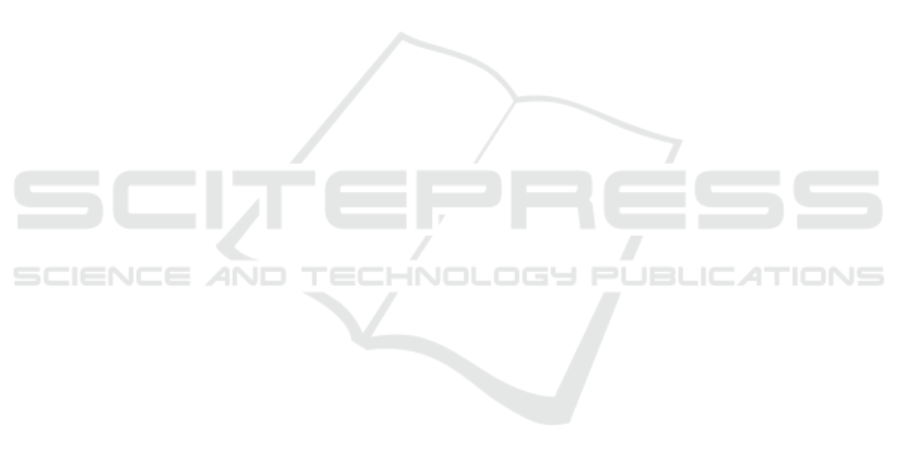
We showed that it is possible to increment the ac-
curacy of the models by complementing the dataset.
Implementing a model that can integrate more infor-
mation to improve the learning process during driving
is a direction for future work.
REFERENCES
Acosta Reche, M. and Kanarachos, S. (2017). Tire lateral
force estimation and grip potential identification using
neural networks, extended kalman filter, and recursive
least squares. Neural Computing and Applications,
2017:1–21.
Bechtoff, J., Koenig, L., and Isermann, R. (2016).
Cornering stiffness and sideslip angle estimation
for integrated vehicle dynamics control. IFAC-
PapersOnLine, 49(11):297 – 304. 8th IFAC Sympo-
sium on Advances in Automotive Control AAC 2016.
Belhajem, I., Maissa, Y. B., and Tamtaoui, A. (2018).
Improving low cost sensor based vehicle positioning
with machine learning. Control Engineering Practice,
74:168–176.
Broderick, D., Bevly, D., and Hung, J. (2009). An adaptive
non-linear state estimator for vehicle lateral dynamics.
pages 1450–1455.
Brossard, M. and Bonnabel, S. (2019). Learning wheel
odometry and imu errors for localization. In 2019 In-
ternational Conference on Robotics and Automation
(ICRA), pages 291–297. IEEE.
Chindamo, D., Lenzo, B., and Gadola, M. (2018). On the
vehicle sideslip angle estimation: A literature review
of methods, models, and innovations. Applied Sci-
ences, 8(3).
Dye, J. and Lankarani, H. (2016). Hybrid simulation of
a dynamic multibody vehicle suspension system us-
ing neural network modeling fit of tire data. page
V006T09A036.
Fejes, P. (2016). Estimation of steering wheel angle in
heavy-duty trucks.
Fukada, Y. (1999). Slip-angle estimation for vehicle stabil-
ity control. Vehicle System Dynamics, 32(4-5):375–
388.
Hochreiter, S. (1998). The vanishing gradient problem dur-
ing learning recurrent neural nets and problem solu-
tions. International Journal of Uncertainty, Fuzziness
and Knowledge-Based Systems, 6:107–116.
Hochreiter, S. and Schmidhuber, J. (1997). Long short-term
memory. Neural computation, 9:1735–80.
Kallasi, F., Rizzini, D. L., Oleari, F., Magnani, M., and
Caselli, S. (2017). A novel calibration method for
industrial agvs. Robotics and Autonomous Systems,
94:75 – 88.
Kendall, A., Grimes, M., and Cipolla, R. (2015). Convolu-
tional networks for real-time 6-dof camera relocaliza-
tion. CoRR, abs/1505.07427.
Kiencke, U. and Nielsen, L. (2000). Automotive control
systems: For engine, driveline, and vehicle. Measure-
ment Science and Technology, 11(12):1828–1828.
Kingma, D. P. and Ba, J. (2014). Adam: A method for
stochastic optimization.
Konda, K. R. and Memisevic, R. (2015). Learning visual
odometry with a convolutional network. In VISAPP
(1), pages 486–490.
Li, Z., Wang, Y., and Liu, Z. (2016). Unscented kalman
filter-trained neural networks for slip model predic-
tion. PloS one, 11:e0158492.
Melzi, S., Sabbioni, E., Concas, A., and Pesce, M. (2006).
Vehicle sideslip angle estimation through neural net-
works: Application to experimental data.
Moore, T. and Stouch, D. (2014). A generalized extended
kalman filter implementation for the robot operating
system. In Proceedings of the 13th International Con-
ference on Intelligent Autonomous Systems (IAS-13).
Springer.
Reina, G., Ishigami, G., Nagatani, K., and Yoshida, K.
(2010). Odometry correction using visual slip angle
estimation for planetary exploration rovers. Advanced
Robotics, 24:359–385.
Sasaki, H. and Nishimaki, T. (2000). A side-slip angle es-
timation using neural network for a wheeled vehicle.
SAE Transactions, 109:1026–1031.
Stanford Artificial Intelligence Laboratory et al. Robotic
operating system.
Sturm, J., Engelhard, N., Endres, F., Burgard, W., and Cre-
mers, D. (2012). A benchmark for the evaluation of
rgb-d slam systems. pages 573–580.
Valente, M., Joly, C., and de La Fortelle, A. (2019). Deep
sensor fusion for real-time odometry estimation.
Wang, S., Clark, R., Wen, H., and Trigoni, N. (2017).
Deepvo: Towards end-to-end visual odometry with
deep recurrent convolutional neural networks. In 2017
IEEE International Conference on Robotics and Au-
tomation (ICRA), pages 2043–2050.
Wei, W., Shaoyi, B., Lanchun, Z., Kai, Z., Yongzhi, W., and
Weixing, H. (2016). Vehicle sideslip angle estimation
based on general regression neural network. Mathe-
matical Problems in Engineering, 2016:1–7.
Weinstein, A. and Moore, K. (2010). Pose estimation of
ackerman steering vehicles for outdoors autonomous
navigation. pages 579 – 584.
Yim, S. (2017). Coordinated control of esc and afs with
adaptive algorithms. International Journal of Auto-
motive Technology, 18(2):271–277.
Zanon, M., Frasch, J., Vukov, M., Sager, S., and Diehl, M.
(2014). Model Predictive Control of Autonomous Ve-
hicles, volume 455.
Zhan, H., Garg, R., Saroj Weerasekera, C., Li, K., Agar-
wal, H., and Reid, I. (2018). Unsupervised learning
of monocular depth estimation and visual odometry
with deep feature reconstruction. In Proceedings of
the IEEE Conference on Computer Vision and Pattern
Recognition, pages 340–349.
ROBOVIS 2020 - International Conference on Robotics, Computer Vision and Intelligent Systems
50