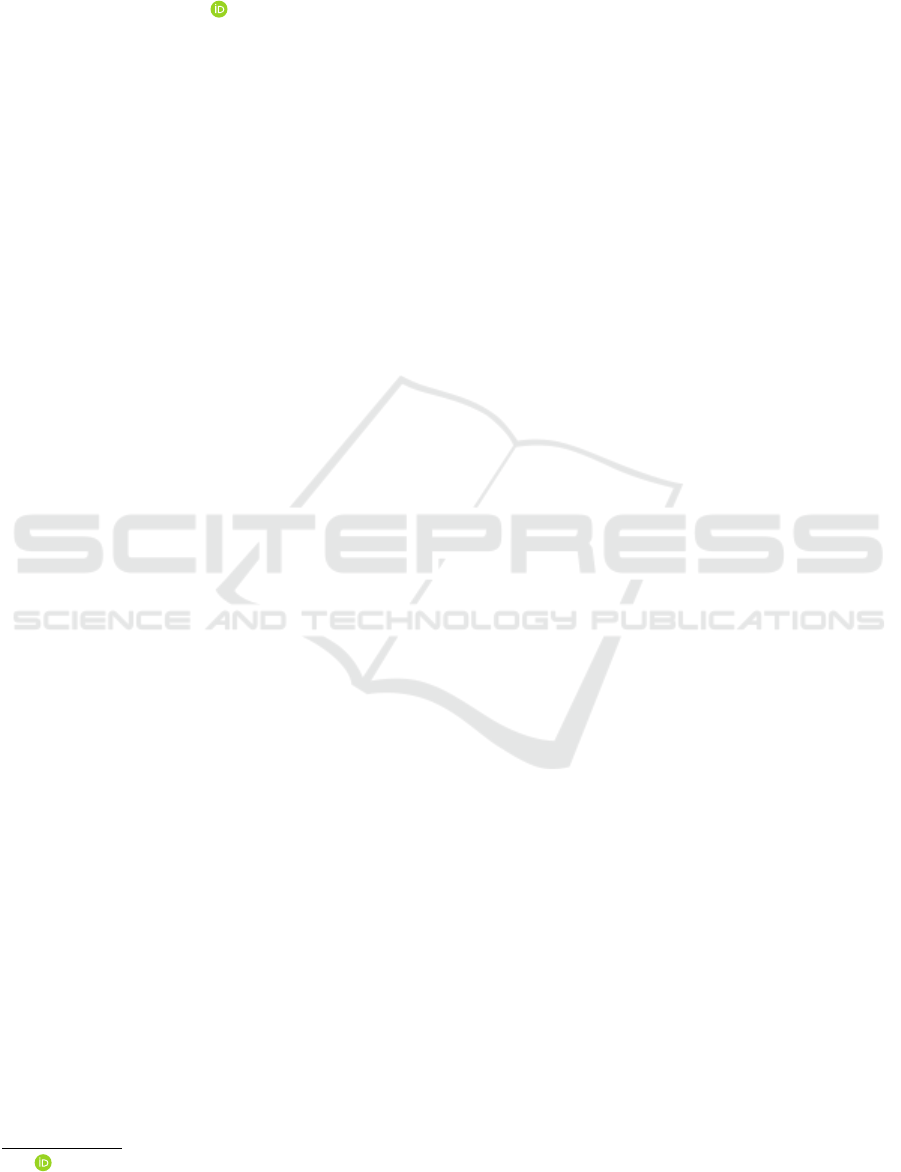
Fuzzy Logic-based Adaptive Cruise Control for Autonomous Model Car
Khaled Alomari
a
, Ricardo Carrillo Mendoza, Stephan Sundermann, Daniel Goehring
and Ra
´
ul Rojas
Dahlem Center for Machine Learning and Robotics - Freie Universit
¨
at Berlin, Arnimallee 7, 14195 Berlin, Germany
Keywords:
Advanced Driver Assistance Systems, Adaptive Cruise Control, Fuzzy Logic.
Abstract:
One of the most critical challenges for the driver during highway driving is to adjust the vehicle speed con-
tinuously to maintain safe distance in respect to the heading vehicles or highway traffic. Neglecting a safe
distance can cause deadly collisions, especially at high velocities. Thus, car speed must adapt smoothly and
efficiently in relation to the velocity of the vehicle in front and the headway distance. Adaptive Cruise Control
(ACC) is an Advanced Driver Assistant System that is used to control both velocity and distance at the same
time. The system needs either a PID controller per state or a MIMO system. In this paper, we propose an ACC
using a Fuzzy Logic approach for an autonomous model car called “AutoMiny.” AutoMiny was developed at
the Dahlem Center for Machine Learning and Robotics at Freie Universit
¨
at Berlin. It navigates by correcting
its orientation error given by a global localization system and a pre-built grid map. The proposed controller
can handle two states with differently designed profiles, and we will compare the performance of our approach
with that of a PID controller.
1 INTRODUCTION
Advanced Driver Assistant Systems (ADAS) in vehi-
cles have had significant improvement over the last
decade. This is due to increased efforts from sev-
eral automotive manufacturers and the testing of self-
driving cars on public roads around the globe in re-
cent years, which induced even more significant in-
vestments by many industry members. Cars equipped
with ADAS with several automation features, such as
automatic parking systems, automotive night visions,
and automotive navigation systems have already be-
gun to appear in the market from various manufactur-
ers. These systems are meant not only to assist the
driver in driving efficiently but also to prevent col-
lision or accident probability (Naranjo et al., 2003).
Furthermore, self-driving vehicles have become no-
table for their potential to provide individual mobility
assistance (Chan, 2017).
Adaptive Cruise Control (ACC) is a vital ADAS
that almost all automotive manufacturers are aiming
to deliver in their modern cars. Vehicles provided
with cruise control are considered level 1 autonomous
cars as defined in SAE J3016 standard (SAE-J3016,
2018). It controls both velocity and distance based
on information provided by onboard sensors such as
a
https://orcid.org/0000-0001-7248-0056
laser scanners, radars, or cameras. These sensors help
to distinguish if the vehicle is approaching a vehi-
cle ahead so that it can adjust its speed and the dis-
tance to the car ahead to prevent a collision; other-
wise, it drives at a preset speed. ACC has been intro-
duced to significantly improve driver preference and
decrease workload as an intelligent driver assistance
system. Such a system helps to prevent accidents and
depreciate the consequences of an impact should one
occur by sustaining a safe gap and speed in the de-
sired range of the driver (Sang-Jin Ko and Ju-Jang
Lee, 2007) (Mamat and Ghani, 2009). Furthermore, it
can improve driving comfort, decrease driving errors,
enhance safety, expand traffic limits, and reduce fuel
consumption (Lu and Aakre, 2018).
There are multiple methods to implement Adap-
tive Cruise Control. Mathematical control-based
techniques produce reliable results but with high com-
putational and design costs. Using fuzzy logic for
ACC has been in academia and industry for many
years (Sang-Jin Ko and Ju-Jang Lee, 2007) (Pana-
nurak et al., 2009). However, most publications fo-
cused on experiments in a simulation environment
(Basjaruddin et al., 951) (Singh et al., 2015). This pa-
per presents a large amount of interesting experimen-
tal results to compare the performance of our fuzzy
logic controller with that of a PID controller.
Alomari, K., Mendoza, R., Sundermann, S., Goehring, D. and Rojas, R.
Fuzzy Logic-based Adaptive Cruise Control for Autonomous Model Car.
DOI: 10.5220/0010175101210130
In Proceedings of the International Conference on Robotics, Computer Vision and Intelligent Systems (ROBOVIS 2020), pages 121-130
ISBN: 978-989-758-479-4
Copyright
c
2020 by SCITEPRESS – Science and Technology Publications, Lda. All rights reserved
121