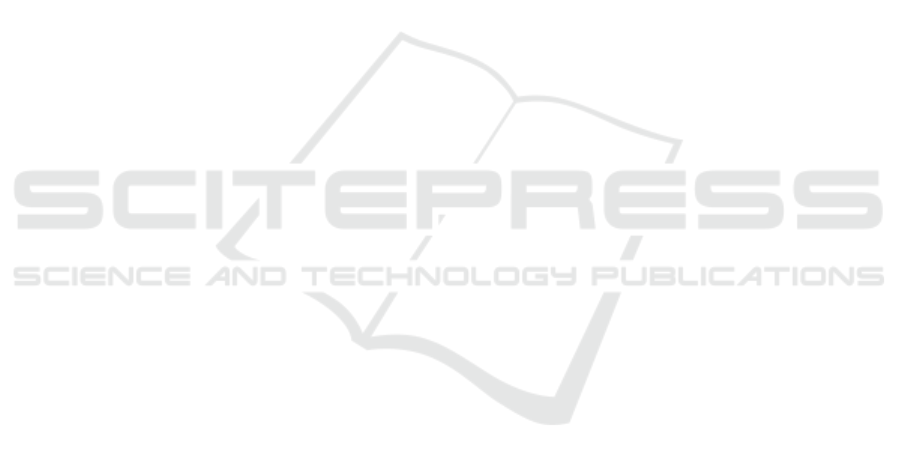
pensate for as much as 87% of the positioning error.
The number of measured points was 12, and the per-
formance of the four different algorithms was com-
pared (Barati et al., 2011). Improved quantum par-
ticle swarm optimization (IQPSO) also proved as an
effective algorithm for the identification of the robot
parameters (Wang et al., 2016). The mean squared
error (MSE) of 260 positions measured by the laser
tracker was 2.80 mm, and after IQPSO optimization,
the MSE was only 0.07 mm. Compared with the or-
dinary particle swarm optimization algorithm (Alici
et al., 2006), the convergence speed was improved by
200%. The genetic algorithm can also be used to es-
tablish and identify the whole geometric model of a
robot (Dolinsky et al., 2007). The mapping between
the ideal and the realized robot positions were based
on a dataset of 30 robot measurements. Another 30
positions were used for the validation of the calibra-
tion and the MSE was improved from 1.85 mm prior
to calibration to 0.77 mm after calibration.
Parametric calibration has fast convergence, the
computation cost is low and the insight into the error
sources is provided. Geometrical errors are usually
the main cause of robot inaccuracy and they are re-
sponsible for up to 90% of the total positioning errors
(Judd and Knasinski, 1990). However, non-geometric
error sources (such as joint compliance errors caused
by the robot weight and the payload, link deflection
errors, backlash in gear transmission and thermal ef-
fects) make a smaller but still a significant contribu-
tion to the positional error of the robot (Elatta et al.,
2004). It is difficult to model these effects paramet-
rically because their number is too great to consider
every one of them, but they can be corrected with
non-parametric calibration. This type of calibration is
independent of the robot model, and one of the meth-
ods used for non-parametric calibration is optimiza-
tion with neural networks. It consists of three basic
steps: measurement and the recording of the real and
expected position of the robot, training and testing
the neural network which simulates the behaviour of
the robot and using the neural network output for the
compensation of the error.
Neural networks were mostly used as an addi-
tional step in the calibration process for compensation
of the non-geometric errors after the kinematic pa-
rameters have been determined (Aoyagi et al., 2010).
The first experiments in using neural networks for
robot calibration started three decades ago, and the
artificial neural network managed to reduce the ab-
solute positioning error by 1/3 for a 6-DOF manip-
ulator (Takanashi, 1990). This was succeeded with
a small dataset of 25 measured points. A Recur-
rent Neural Network (RNN) was also used for both
the simulated and the experimental calibration of a 6-
DOF robot (Xiao-Lin Zhong and Lewis, 1995). Only
the internal joint measurements were used while the
manipulator was in contact with the constraint plane,
which generated the identification equations. A Hop-
field type RNN was used for solving these equations
and kinematic parameters were extracted. In total,
120 points have been used and position accuracy has
been improved to the level of robot repeatability. A
back-propagating neural network was used to com-
pensate the joint transmitting error, but only after the
geometric calibration of the robot (Liu et al., 2007).
The input values for the neural network were joint
angles and the information about the rotation direc-
tion, and the output was the angle by which the mo-
tors should rotate. The number of measured points
was 19, and the robot workspace size was 15 x 15 x
15 cm. Experimental verification showed the MSE
decreased from 3.7 mm prior, to 0.5 mm after the cal-
ibration process. More extensive data was provided
with automated measuring system, which collected
more than 10.000 robot positions and configurations
(Zhao et al., 2019). The two-step calibration process
consisted of a parametric calibration which identified
the geometric parameters, and a non-parametric cali-
bration which identified the nonlinear residual errors
by using deep neural networks. The MSE was re-
duced from 1.81 mm to 0.10 mm. The repeatability
accuracy of the robot was 0.05 mm. Other compensa-
tions of non-parametric effects were made with neu-
ral networks after identification of a robots geometric
parameters by using the extended Kalman filter algo-
rithm (Nguyen et al., 2015) and joint angle division
(Wang et al., 2019). Experimental validations of both
methods confirmed the enhanced position accuracy,
which was increased from 3.59 mm to 0.42 mm in the
first, and from 17 cm to 4.5 cm in the second example.
Shallow neural networks were used on a simu-
lated dataset, which demonstrated the superior perfor-
mance of a non-parametric calibration with a neural
network in comparison with bilinear and fuzzy inter-
polations (Bai and Wang, 2019). The absolute posi-
tion accuracy of a drilling robot was also improved
by using the algorithm based on the extreme learning
machine (Yuan et al., 2018). The input of the neural
network was ideal position of a robot and the output
was positional error measured by a laser tracker. The
robot controller was directed to compensate for the
predicted positional errors. By using this method, the
absolute position was improved by 75.89%. It was
also shown that choosing different hyperparameters
of a neural network could increase the accuracy.
The main advantage of the non-parametric cali-
bration lies in the possibility of simple application to
ROBOVIS 2020 - International Conference on Robotics, Computer Vision and Intelligent Systems
52