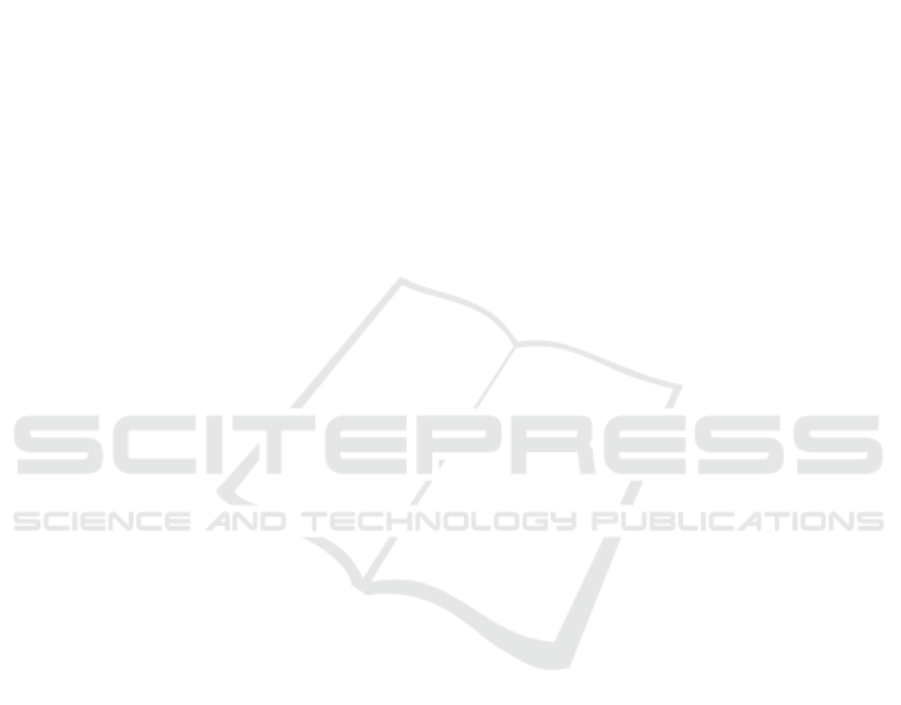
Automatic Food Packaging System using Programmable Logic
Controller
Ahmad Sahru Romadhon, Vivi Tri Widyaningrum
Mechatronic Departement, Faculty of Engineering University of Truojoyo Madura, Raya Telang Street PO BOX 2 Kamal,
Bangkalan, East Java, Indonesia
Keywords: Food packaging, PLC and automatic packaging.
Abstract: Food packaging using conventional machine has undelighted results, so it automatic packaging would be the
solve that problem.it can more productive and quick. Basically, the working system of this automatic
packaging begins with installing plastic on the rollers and installing plastic on the edge of the feeding tube so,
the plastic will have a shape also like the tube. The next step is to put food into the container in the machine
and the engine is turned on. Next, for the packaging grooves, the plastic will be pulled by the motor, then the
bottom of the plastic is glued by the pressing process which later the plastic will form a container in
accordance with a tubular mold. Food that has filled the container in the machine is passed through a tube that
was previously covered by plastic, then the top plastic is glued by the pressing process. The results of PLC
application testing on mechanics by providing a 12 volt power supply to a DC motor in a mechanical system
show that the program loaded into the system provides the expected results.
1 INTRODUCTION
The development of technology in the modern
industrial era is increasingly rapidly. Especially in
control systems, the technology is developing rapidly
as well where the current process is in the control
system not only in the form of a circuit that using
electrically assembled equipment, but also has used a
computer program to control it. This situation
certainly requires a simple, practical and high-tech
supporting equipment (Nanda, 2014). For example, it
can be seen at the creation of equipment that can work
automatically, thereby reducing the role of humans to
do food packaging.
Packaging is a way to protect food products,
beverages or the consumable things from damage
caused by air. According to several studies showing
that packaging is one of the most important
considerations that can influence consumer for
purchasing products. The packaging of a product can
be attractive to consumers if the packaging is well
made and neat, so it requires a packaging machine
that is simple and easy to use (Simran, ,2019). Based
on this description, the idea to create a PLC
(programable logic controller) automatic food
packaging Machine that could be make easier to the
home industry community to packaging their
products.
PLC can be used as a fairly reliable control
equipment so it is widely used in industrial
equipment, for example in the process of selecting
materials, packaging, handling materials, automatic
assembly and others. Basically, almost all systems
that require control over electricity or electronics
require a PLC (Pralhad, 2018, Sasidhar, 2017). So in
this research, PLC can be more innovating to create
Automatic Food Monitoring System Using PLC
(Programmable Logic Controller).
Basically, the packaging system in this study
functions to laminate plastic parts that have been
filled with food, so that the food is in the form of a
vacuum bag. This automatic food packaging system
begins with mounting plastics on rollers and installing
plastics on the edge of the feeding tube so the plastic
will have a shape like the tube. The plastic will be
pulled by two motors, then the bottom of the plastic
is glued by the pressing process which later the plastic
will form a container in accordance with a tubular
mold. After the pressing process is finished, the next
process is filling in the plastic and the plastic will be
pressed once more at the top.
Romadhon, A. and Widyaningrum, V.
Automatic Food Packaging System using Programmable Logic Controller.
DOI: 10.5220/0010331202710277
In Proceedings of the International Conference on Health Informatics, Medical, Biological Engineering, and Pharmaceutical (HIMBEP 2020), pages 271-277
ISBN: 978-989-758-500-5
Copyright
c
2021 by SCITEPRESS – Science and Technology Publications, Lda. All rights reserved
271