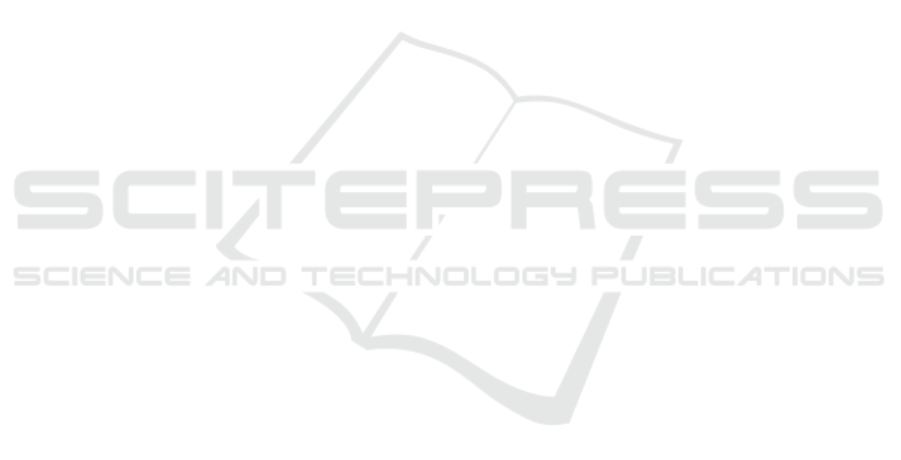
for which purpose. We propose to use another lan-
guage to represent the system functions to simulate,
independently of their implementation models, and to
build a model transformation toward CosiML.
REFERENCES
Andr
´
en, F., Strasser, T., and Kastner, W. (2017). Engineer-
ing Smart Grids: Applying Model-Driven Develop-
ment from Use Case Design to Deployment. Energies,
10(3):374.
Blochwitz, T., Otter, M., Arnold, M., Bausch, C., Elmqvist,
H., et al. (2011). The functional mockup interface for
tool independent exchange of simulation models. In
Proceedings of the 8th International Modelica Con-
ference, pages 105–114.
Broman, D., Greenberg, L., Lee, E. A., Masin, M., Tripakis,
S., and Wetter, M. (2015). Requirements for Hybrid
Cosimulation Standards. In Proceedings of the 18th
International Conference on Hybrid Systems: Compu-
tation and Control, HSCC ’15, pages 179–188. ACM.
Cremona, F., Lohstroh, M., Broman, D., Lee, E. A., Masin,
M., and Tripakis, S. (2019). Hybrid co-simulation:
it’s about time. Software and System Modeling,
18(3):1655–1679.
Dahmann, J. S. and Morse, K. L. (1998). High Level Ar-
chitecture for simulation: An update. In Proceed-
ings. 2nd International Workshop on Distributed In-
teractive Simulation and Real-Time Applications (Cat.
No.98EX191), pages 32–40.
Elsheikh, A., Awais, M. U., Widl, E., and Palensky, P.
(2013). Modelica-enabled rapid prototyping of cyber-
physical energy systems via the functional mockup in-
terface. pages 1–6. IEEE.
´
Evora G
´
omez, J., Hern
´
andez Cabrera, J. J., Tavella,
J.-P., Vialle, S., Kremers, E., and Frayssinet, L.
(2019). Daccosim NG: Co-simulation made simpler
and faster. In The 13th International Modelica Con-
ference, pages 785–794.
Gomes, C., Meyers, B., Denil, J., Thule, C., Lausdahl, K.,
Vangheluwe, H., and De Meulenaere, P. (2018a). Se-
mantic adaptation for FMI co-simulation with hierar-
chical simulators. SIMULATION.
Gomes, C., Thule, C., Larsen, P. G., and Vangheluwe, H.
(2018b). Co-Simulation: A Survey. ACM Computing
Surveys, 51(3):49:1–49:33.
Guermazi, S., Tatibouet, J., Cuccuru, A., Dhouib, S.,
G
´
erard, S., and Seidewitz, E. (2015). Executable mod-
eling with fUML and alf in papyrus: Tooling and ex-
periments. In EXE@MoDELS.
Li, W., Monti, A., Luo, M., and Dougal, R. A. (2011). VP-
NET: A co-simulation framework for analyzing com-
munication channel effects on power systems. In 2011
IEEE Electric Ship Technologies Symposium, pages
143–149.
Muller, S. C., Georg, H., Nutaro, J. J., Widl, E., Deng, Y.,
Palensky, P., Awais, M. U., and al. (2018). Interfacing
Power System and ICT Simulators: Challenges, State-
of-the-Art, and Case Studies. IEEE Trans. Smart Grid,
9(1):14–24.
Nutaro, J. (2011). Designing power system simulators
for the smart grid: Combining controls, communi-
cations, and electro-mechanical dynamics. In 2011
IEEE Power and Energy Society General Meeting,
pages 1–5.
Oudart, D., Cantenot, J., Boulanger, F., and Chabridon, S.
(2019). An Approach to Design Smart Grids and Their
IT System by Cosimulation:. In MODELSWARD 19,
pages 370–377. SCITEPRESS - Science and Technol-
ogy Publications.
Palensky, P., Van Der Meer, A. A., Lopez, C. D., Joseph, A.,
and Pan, K. (2017). Cosimulation of Intelligent Power
Systems: Fundamentals, Software Architecture, Nu-
merics, and Coupling. IEEE Industrial Electronics
Magazine, 11(1):34–50.
Paris, T., Ciarletta, L., and Chevrier, V. (2017). Design-
ing co-simulation with multi-agent tools: a case study
with NetLogo. In Francesco Belardinelli, E. A., ed-
itor, 15th European Conference on Multi-Agent Sys-
tems (EUMAS 2017), volume 10767 of Multi-Agent
Systems and Agreement Technologies, pages 253–267,
´
Evry, France. Springer.
Rohjans, S., Lehnhoff, S., Sch
¨
utte, S., Andr
´
en, F., and
Strasser, T. (2014). Requirements for Smart Grid sim-
ulation tools. In 2014 IEEE 23rd International Sym-
posium on Industrial Electronics (ISIE), pages 1730–
1736.
Suri, K., Cuccuru, A., Cadavid, J., Gerard, S., Gaaloul, W.,
and Tata, S. (2017). Model-based Development of
Modular Complex Systems for Accomplishing Sys-
tem Integration for Industry 4.0. In Proceedings of the
5th International Conference on Model-Driven Engi-
neering and Software Development - Volume 1: MOD-
ELSWARD,, pages 487–495. ScitePress.
Tavella, J.-P., Caujolle, M., Vialle, S., and al. (2016). To-
ward an Accurate and Fast Hybrid Multi-Simulation
with the FMI-CS Standard. In Emerging Technologies
and Factory Automation (ETFA-2016), Berlin, Ger-
many.
Van Acker, B., Denil, J., Vangheluwe, H., and De Meule-
naere, P. (2015). Generation of an optimised master
algorithm for fmi co-simulation. In DEVS Integrative
M&S Symposium, DEVS ’15. Society for Computer
Simulation International.
Yang, C.-H., Zhabelova, G., Yang, C.-W., and Vyatkin, V.
(2013). Cosimulation Environment for Event-Driven
Distributed Controls of Smart Grid. IEEE Trans. In-
dustrial Informatics, 9(3):1423–1435.
Zhao, H., Apvrille, L., and Mallet, F. (2017). Multi-View
Design for Cyber-Physical Systems. In PhD Sympo-
sium at 13th International Conference on ICT in Ed-
ucation, Research, and Industrial Applications, pages
22–28, Kiev, Ukraine.
A Model based Toolchain for the Cosimulation of Cyber-physical Systems with FMI
25