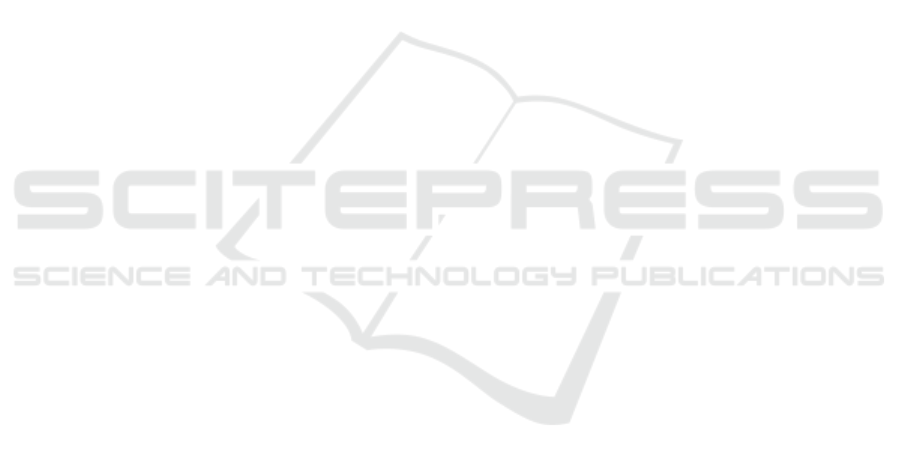
trol approach for an industrial furnace to mini-
mize idle energy consumption. arXiv e-prints, page
arXiv:1910.07501.
Benedikt, O.,
ˇ
S
˚
ucha, P., M
´
odos, I., Vlk, M., and Hanz
´
alek,
Z. (2018). Energy-aware production scheduling with
power-saving modes. In van Hoeve, W.-J., editor, Inte-
gration of Constraint Programming, Artificial Intelli-
gence, and Operations Research, pages 72–81, Cham.
Springer International Publishing.
Benini, L., Bogliolo, A., and Micheli, G. D. (2000). A
survey of design techniques for system-level dynamic
power management. IEEE Transactions on Very Large
Scale Integration (VLSI) Systems, 8(3):299–316.
Che, A., Wu, X., Peng, J., and Yan, P. (2017). Energy-
efficient bi-objective single-machine scheduling with
power-down mechanism. Computers & Operations
Research, 85:172 – 183.
Devadas, V. and Aydin, H. (2012). On the interplay of
voltage/frequency scaling and device power manage-
ment for frame-based real-time embedded applica-
tions. IEEE Trans. Comput., 61(1):31–44.
Du
ˇ
sek, J. (2016). N
´
avrh
´
upravy
ˇ
r
´
ızen
´
ı v
´
yrobn
´
ı linky s ohle-
dem na sn
´
ı
ˇ
zen
´
ı jej
´
ı spot
ˇ
reby. Master’s thesis, Czech
Technical University in Prague, the Czech republic.
Fang, K.-T. and Lin, B. M. (2013). Parallel-machine
scheduling to minimize tardiness penalty and power
cost. Computers & Industrial Engineering, 64(1):224
– 234.
Gahm, C., Denz, F., Dirr, M., and Tuma, A. (2016). Energy-
efficient scheduling in manufacturing companies: A
review and research framework. European Journal of
Operational Research, 248(3):744 – 757.
Gao, K., Huang, Y., Sadollah, A., and Wang, L. (2019).
A review of energy-efficient scheduling in intelligent
production systems. Complex & Intelligent Systems.
Garey, M. and Johnson, D. (1977). Two-processor schedul-
ing with start-times and deadlines. SIAM Journal on
Computing, 6(3):416–426.
Gerards, M. E. T. and Kuper, J. (2013). Optimal DPM and
DVFS for frame-based real-time systems. ACM Trans.
Archit. Code Optim., 9(4):41:1–41:23.
Gong, X., Pessemier, T. D., Joseph, W., and Martens, L.
(2016). A generic method for energy-efficient and
energy-cost-effective production at the unit process
level. Journal of Cleaner Production, 113:508 – 522.
Kon
´
e, O., Artigues, C., Lopez, P., and Mongeau, M. (2011).
Event-based MILP models for resource-constrained
project scheduling problems. Computers & Opera-
tions Research, 38(1):3 – 13. Project Management and
Scheduling.
Liang, P., dong Yang, H., sheng Liu, G., and hua Guo,
J. (2015). An ant optimization model for unrelated
parallel machine scheduling with energy consumption
and total tardiness. Mathematical Problems in Engi-
neering.
Liu, S., Pinto, J. M., and Papageorgiou, L. G.
(2008). A TSP-based MILP model for medium-
term planning of single-stage continuous multiproduct
plants. Industrial & Engineering Chemistry Research,
47(20):7733–7743.
Masmoudi, O., Yalaoui, A., Ouazene, Y., and Chehade,
H. (2017). Solving a capacitated flow-shop prob-
lem with minimizing total energy costs. The Interna-
tional Journal of Advanced Manufacturing Technol-
ogy, 90(9):2655–2667.
M
´
odos., I., Kalodkin., K.,
ˇ
S
˚
ucha., P., and Hanz
´
alek., Z.
(2019). Scheduling on dedicated machines with en-
ergy consumption limit. In Proceedings of the 8th In-
ternational Conference on Operations Research and
Enterprise Systems - Volume 1: ICORES,, pages 53–
62. INSTICC, SciTePress.
Meng, L., Zhang, C., Shao, X., and Ren, Y. (2019). Milp
models for energy-aware flexible job shop scheduling
problem. Journal of Cleaner Production, 210:710 –
723.
Mitra, S., Grossmann, I. E., Pinto, J. M., and Arora,
N. (2012). Optimal production planning under
time-sensitive electricity prices for continuous power-
intensive processes. Computers & Chemical Engi-
neering, 38:171 – 184.
Mouzon, G., Yildirim, M., and Twomey, J. (2007). Opera-
tional methods for minimization of energy consump-
tion of manufacturing equipment. International Jour-
nal of Production Research, 45:4247–4271.
Shrouf, F., Ordieres-Mer
´
e, J., Garc
´
ıa-S
´
anchez, A., and
Ortega-Mier, M. (2014). Optimizing the production
scheduling of a single machine to minimize total en-
ergy consumption costs. Journal of Cleaner Produc-
tion, 67:197 – 207.
Sinha, A. and Chandrakasan, A. (2001). Dynamic power
management in wireless sensor networks. IEEE De-
sign Test of Computers, 18(2):62–74.
APPENDIX
Here, the position-based MILP model used for the
comparison is described. It was originally proposed in
(Che et al., 2017) to minimize the total tardiness and
idle energy on a single machine with a single power-
saving mode.
Reference Model
The idea of the model is to represent all possible
positions to which the individual jobs can be as-
signed. The variable representing the completion time
is linked with the position instead of the job. A set
of constraints assure that if a job is assigned to some
position, its completion time is bounded (by the dead-
line, neighboring jobs, etc.). Following decision vari-
ables are used:
x
i,l,k
Binary variable; if job J
i
is assigned to position
l on machine M
k
. then x
i,l,k
= 1, otherwise 0
y
l,k
Binary variable; if there is turn-off-on opera-
tion immediately after l-th job is processed on
machine M
k
, then y
l,k
= 1, otherwise 0
On Idle Energy Consumption Minimization in Production: Industrial Example and Mathematical Model
45