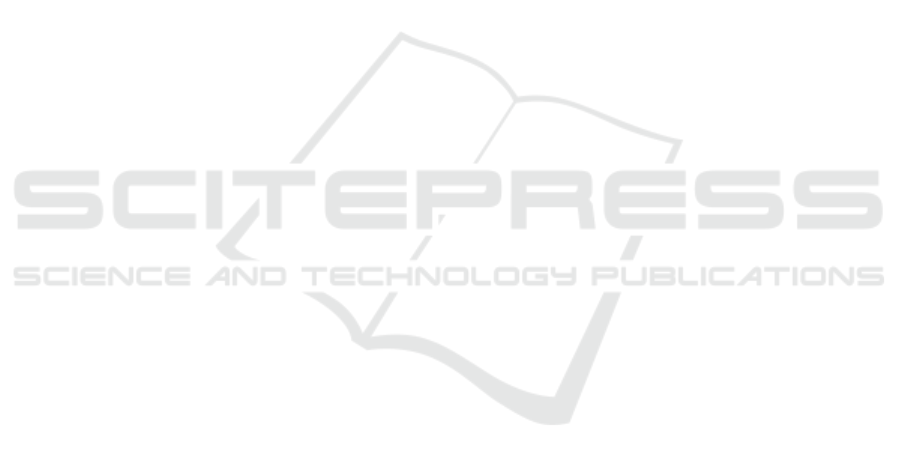
ing step, which takes into account the orientation of
the source and destination sections of the pipe. Also,
the techniques proposed make pipe routing possible
for pipes that have a non symmetrical section such as
a rectangular one.
Both presented approaches are sensitive to the in-
crease in the number of bends, even if the MILP ap-
proach seems more robust for delivering an optimal
solution. The MILP resolution might also be boosted
by using column generation techniques with a master
problem considering bend variables. The Combined
Graph-LP solver could also be accelerated by im-
proving the combination enumeration procedure with,
for example, a bidirectional A* enumeration starting
from the source and destination orientations.
As a result, the new methods introduced in this
paper can be efficiently used as a first routing algo-
rithm. If the optimal pipe route obtained by solving
the 3D-OFPRP problem collides with obstacles of the
3D-PRP problem, Branch-and-Cut techniques can be
integrated to the MILP approach by (a) analyzing the
solution generated, (b) adding new integer variables
and new linear constraints to enforce that pipe sec-
tions must not traverse the obstacle sides for which
collisions are detected, (c) solving the problem again,
and so on until a valid pipe routing is found. One dif-
ficulty though will concern the management of colli-
sions with the pipe itself, since the pipe sections can-
not be considered as fixed obstacles from one resolu-
tion to the next.
REFERENCES
Ando, Y. and Kimura, H. (2012). An automatic piping al-
gorithm including elbows and bends. Journal of the
Japan Society of Naval Architects and Ocean Engi-
neers, 15:219–226.
Asmara, A. and Nienhuis, U. (2006). Automatic piping sys-
tem in ship. In International Conference on Computer
and IT Application (COMPIT).
Belov, G., Czauderna, T., Dzaferovic, A., de la Banda,
M. G., Wybrow, M., and Wallace, M. (2017). An op-
timization model for 3d pipe routing with flexibility
constraints. In International Conference on Princi-
ples and Practice of Constraint Programming, pages
321–337. Springer.
Fan, X., Lin, Y., and Ji, Z. (2006). The ant colony opti-
mization for ship pipe route design in 3d space. In
2006 6th World Congress on Intelligent Control and
Automation, pages 3103–3108. IEEE.
Furuholmen, M., Glette, K., Hovin, M., and Torresen,
J. (2010). Evolutionary approaches to the three-
dimensional multi-pipe routing problem: a compar-
ative study using direct encodings. In European Con-
ference on Evolutionary Computation in Combinato-
rial Optimization, pages 71–82. Springer.
Guirardello, R. and Swaney, R. E. (2005). Optimization of
process plant layout with pipe routing. Computers &
chemical engineering, 30(1):99–114.
Hightower, D. W. (1969). A solution to line-routing prob-
lems on the continuous plane. In Proceedings of the
6th annual Design Automation Conference, pages 1–
24. ACM.
Ikehira, S., Kimura, H., Ikezaki, E., and Kajiwara, H.
(2005). Automatic design for pipe arrangement us-
ing multi-objective genetic algorithms. Journal of the
Japan Society of Naval Architects and Ocean Engi-
neers, 2:155–160.
Ito, T. (1999). A genetic algorithm approach to piping route
path planning. Journal of Intelligent Manufacturing,
10(1):103–114.
Jiang, W.-Y., Lin, Y., Chen, M., and Yu, Y.-Y. (2015). A co-
evolutionary improved multi-ant colony optimization
for ship multiple and branch pipe route design. Ocean
Engineering, 102:63–70.
Kimura, H. (2011). Automatic designing system for pip-
ing and instruments arrangement including branches
of pipes. In International Conference on Computer
Applications in Shipbuilding (ICCAS), pages 93–99.
IEEE.
Lee, C. Y. (1961). An algorithm for path connections and its
applications. In IRE transactions on electronic com-
puters, number 3, pages 346–365. IEEE.
Liu, L. and Liu, Q. (2018). Multi-objective routing of multi-
terminal rectilinear pipe in 3d space by moea/d and
rsmt. In 3rd International Conference on Advanced
Robotics and Mechatronics (ICARM), pages 462–467.
IEEE.
Medjdoub, B. and Bi, G. (2018). Parametric-based dis-
tribution duct routing generation using constraint-
based design approach. Automation in Construction,
90:104–116.
Park, J.-H. and Storch, R. L. (2002). Pipe-routing algorithm
development: case study of a ship engine room design.
Expert Systems with Applications, 23(3):299–309.
S.-H., K., W.-S., R., and S., J. B. (2013). The develop-
ment of a practical pipe auto-routing system in a ship-
building cad environment using network optimization.
International journal of naval architecture and ocean
engineering, 5(3):468–477.
Sakti, A., Zeidner, L., Hadzic, T., Rock, B. S., and Quar-
tarone, G. (2016). Constraint programming approach
for spatial packaging problem. In International Con-
ference on AI and OR Techniques in Constraint Pro-
gramming for Combinatorial Optimization Problems,
pages 319–328. Springer.
Zhu, D. and Latombe, J.-C. (1991). Pipe routing-path plan-
ning (with many constraints). In Proceedings. 1991
IEEE International Conference on Robotics and Au-
tomation, pages 1940–1947. IEEE.
Optimal Pipe Routing Techniques in an Obstacle-Free 3D Space
79