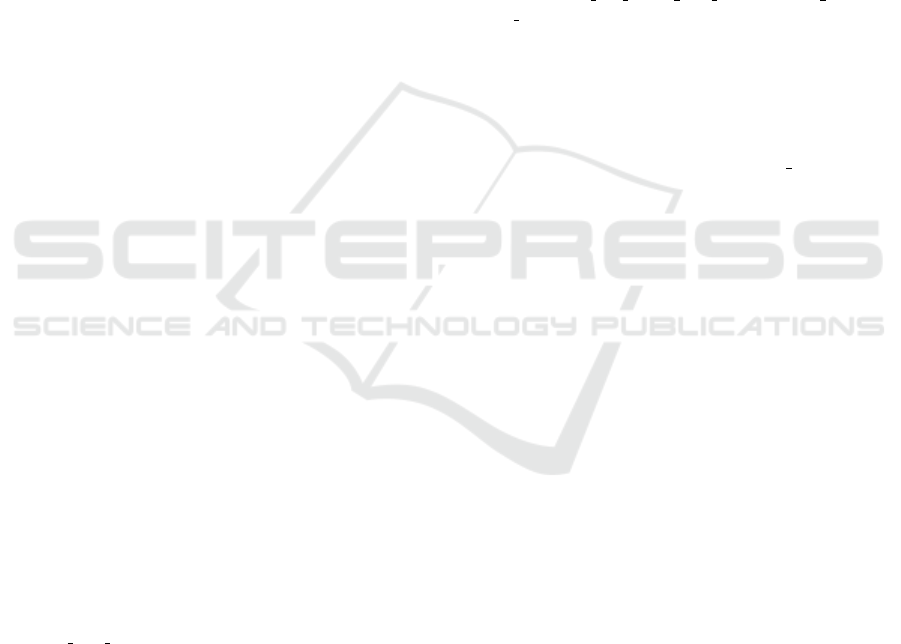
Adafruit (2016b). Adafruit Servo Shield. Available at https:
//www.adafruit.com/product/1411.
Andersen, P., Pedersen, S. T., and Dimon, J. (2002). Ro-
bust feedback linearization-based control design for a
wheeled mobile robot. Proc. of the 6th Interna- tional
Symposium on Advanced Vehicle Control.
Andromina (2016a). Andromia OFF-ROAD. Available at
http://androminarobot.blogspot.mx/ p/montaje.html.
Andromina (2016b). Andromina v.1.2. Available at http:
//androminarobot.blogspot.cz/ search/label/ Arduino.
Arduino (2016). Arduino Mega 2560. Available at https:
//www.arduino.cc/ en/ Main/arduinoBoardMega2560.
Bing-Min, S. and Chun-Liang, L. (2008). Design of an au-
tonomous lawn mower with optimal route planning. In
Industrial Technology, 2008. ICIT 2008. IEEE Inter-
national Conference on, pages 1–6, Chengdu. IEEE.
ISBN: 978-1-4244-1705-6.
Bloch, A. M. (2000). Nonholonomic Mechanics and Con-
trol. Addison-Wesley Publishing Company. ISBN:
0-387-95535-6.
Ch
´
avez Plascencia, A. and Dremstrup, K. (2011). Differen-
tial mobile robot based wheelchair. Technical report,
Aalborg University.
Coelho, P. and Nunes, U. N. (2003). Lie algebra application
to mobile robot control: a tutorial. Robotica, 21:483–
493.
Fox, D., Burgard, W., Frank, D., and Thrun, S. (1999).
Monte carlo localization: Efficient position estimation
for mobile robots. In in proc. of the national confer-
ence on artificial intelligence, AAAI, pages 343–349.
Fox, D., Burgard, W., and Thrun, S. (1997). The dynamic
window approach to collision avoidance. Robotics &
Automation Magazine, IEEE, 4(1):23–33.
Franklin, G. F. and Powell, J. D. (1994). Feedback Control
of Dynamic Systems, third edition. Addison-Wesley.
ISBN: 0-201-53487-8.
Goldstain, H. (1980). Nonholonomic Mechanics and Con-
trol. Addison-Wesley. ISBN: 0-201-02918-9.
Guy, C., Georges, B., and Brigitte, D. A.-n. (1996). Struc-
tural properties and classification of kinematic and dy-
namic models of wheeled mobile robots. IEEE Trans-
actions on Robotics and Automation, pages 47–62.
Harwood, P. (2016). Non-linear automatic control of au-
tonomous lawn mower. Master’s thesis, Link
¨
oping
University, SE-581 83 Linkoping, Sweden.
Hokuyo (2009). URG-04LX-UG01. Available at
https://www.hokuyo-aut.jp/02sensor/ 07scanner/
urg 04lx ug01.html.
Khalil, H. (2002). Nonlinear Systems. Prentice Hall. ISBN:
0-13-067389-7.
Krzysztof, K. and Dariusz, P. (2004). Modeling and con-
trol of a 4-wheel skid-steering mobile robot. Interna-
tional Journal of Applied Mathematics Computer Sci-
ence, 14(4):477–496.
Marquez, H. J. (2003). Nonholonomic Control Systems
Analysis and Design. Wiley. ISBN: 0-471-42799-3.
Mathieu, D., Roland, L., Adrian, C., Christophe, C., and
Benoit, T. (2017). Path tracking of a four-wheel steer-
ing mobile robot: A robust off-road parallel steer-
ing strategy. IEEE European Conference on Mobile
Robots (ECMR).
N.Sarkar, N. and R.V.Kumar (1992). Control of mechanical
systems with rolling constraints: Application to dy-
namic control of mobile robots. Technical report, De-
partment of Computer & Information Science (CIS),
University of Pensylvania.
Paulo, C. and Urbano, N. (2005). Path-following control
of mobile robots in presence of uncertainties. IEEE
International Journal of Transactions on Robotics,
21(2):452–261.
Quigley, M., Conley, K., Gerkey, B., Faust, J., Foote, T. B.,
Leibs, J., Wheeler, R., and Ng, A. Y. (2009). ROS: an
open-source robot operating system. In ICRA Work-
shop on Open Source Software.
SKU (2016). DC Motor with Encoder. Avail-
able at https:// www.dfrobot.com/wiki/ index.
php/Micro DC Motor with Encoder-SJ02 SKU:
FIT0450.
Smith, J., Campbell, S., and Morton, J. (2005). Design
and implementation of a control algorithm for an au-
tonomous lawnmower. In Circuits and Systems, 2005.
48th Midwest Symposium on, volume 1, pages 456–
459, Covington, KY. IEEE. ISBN: 0-7803-9197-7.
Spider (2015). Mini, ILD01, ILD02. Available at https:
//www.slope-mower.com/ spider-ild01 p12.html.
Symon, K. R. (1971). Mechanics. Addison-Wesley World
student series. Addison-Wesley Publishing Company.
ISBN: 9780201073928.
Taj, B. M. and Timothy, K. T. C. (2008). Design and mod-
elling a prototype of a robotic lawn mower. In Infor-
mation Technology, 2008. ITSim 2008. International
Symposium on, volume 4, pages 1–5, Kuala Lumpur,
Malaysia. IEEE. ISBN: 978-1-4244-2327-9.
Wasif, M. (2011). Design and implementation of au-
tonomous lawn-mower robot controller. In 7th In-
ternational Conference on Emerging Technologies
(ICET), pages 1–5. IEEE. ISBN: 978-1-4577-0769-
8.
ICINCO 2020 - 17th International Conference on Informatics in Control, Automation and Robotics
108