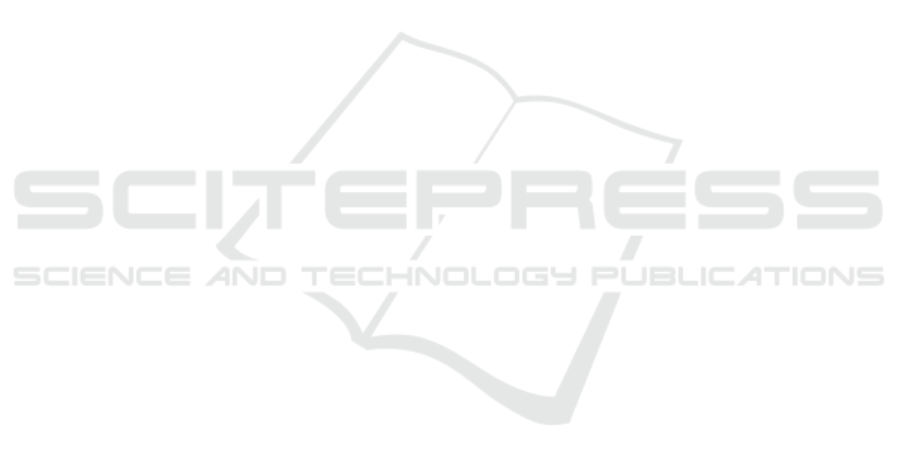
Danielczuk, M., Matl, M., Gupta, S., Li, A., Lee, A.,
Mahler, J., and Goldberg, K. (2019). Segmenting
unknown 3d objects from real depth images using
mask r-cnn trained on synthetic data. In 2019 In-
ternational Conference on Robotics and Automation
(ICRA), pages 7283–7290. IEEE.
Dieter Schraft, R. and Ledermann, T. (2003). Intelligent
picking of chaotically stored objects. Assembly Au-
tomation, 23(1):38–42.
Do, T.-T., Cai, M., Pham, T., and Reid, I. (2018). Deep-
6dpose: Recovering 6d object pose from a single rgb
image. arXiv preprint arXiv:1802.10367.
Dutta, A. and Zisserman, A. (2019). The via annotation
software for images, audio and video. arXiv preprint
arXiv:1904.10699, 5.
Girshick, R. (2015). Fast r-cnn. In Proceedings of the IEEE
international conference on computer vision, pages
1440–1448.
He, K., Gkioxari, G., Doll
´
ar, P., and Girshick, R. (2017).
Mask r-cnn. In Proceedings of the IEEE international
conference on computer vision, pages 2961–2969.
Hema, C. R., Paulraj, M., Nagarajan, R., and Sazali, Y.
(2007). Segmentation and location computation of bin
objects. International Journal of Advanced Robotic
Systems, 4(1):9.
Jolliffe, I. (2011). Principal component analysis. Springer.
Karakasis, E. G., Amanatiadis, A., Gasteratos, A., and
Chatzichristofis, S. A. (2015). Image moment invari-
ants as local features for content based image retrieval
using the bag-of-visual-words model. Pattern Recog-
nition Letters, 55:22–27.
Kim, K., Kim, J., Kang, S., Kim, J., and Lee, J.
(2012). Vision-based bin picking system for indus-
trial robotics applications. In 2012 9th International
Conference on Ubiquitous Robots and Ambient Intel-
ligence (URAI), pages 515–516. IEEE.
Levine, S., Pastor, P., Krizhevsky, A., Ibarz, J., and Quillen,
D. (2018). Learning hand-eye coordination for robotic
grasping with deep learning and large-scale data col-
lection. The International Journal of Robotics Re-
search, 37(4-5):421–436.
Lin, T.-Y., Maire, M., Belongie, S., Hays, J., Perona, P.,
Ramanan, D., Doll
´
ar, P., and Zitnick, C. L. (2014).
Microsoft coco: Common objects in context. In Euro-
pean conference on computer vision, pages 740–755.
Springer.
Liu, M.-Y., Tuzel, O., Veeraraghavan, A., Taguchi, Y.,
Marks, T. K., and Chellappa, R. (2012). Fast ob-
ject localization and pose estimation in heavy clutter
for robotic bin picking. The International Journal of
Robotics Research, 31(8):951–973.
Long, J., Shelhamer, E., and Darrell, T. (2015). Fully con-
volutional networks for semantic segmentation. In
Proceedings of the IEEE conference on computer vi-
sion and pattern recognition, pages 3431–3440.
Mahler, J., Liang, J., Niyaz, S., Laskey, M., Doan, R., Liu,
X., Ojea, J. A., and Goldberg, K. (2017). Dex-net
2.0: Deep learning to plan robust grasps with synthetic
point clouds and analytic grasp metrics. arXiv preprint
arXiv:1703.09312.
Noh, H., Hong, S., and Han, B. (2015). Learning de-
convolution network for semantic segmentation. In
Proceedings of the IEEE international conference on
computer vision, pages 1520–1528.
Palzkill, M. and Verl, A. (2012). Object pose detection in
industrial environment. In ROBOTIK 2012; 7th Ger-
man Conference on Robotics, pages 1–5. VDE.
Ren, S., He, K., Girshick, R., and Sun, J. (2015). Faster
r-cnn: Towards real-time object detection with region
proposal networks. In Advances in neural information
processing systems, pages 91–99.
Schwarz, M., Milan, A., Periyasamy, A. S., and Behnke,
S. (2018). Rgb-d object detection and semantic seg-
mentation for autonomous manipulation in clutter.
The International Journal of Robotics Research, 37(4-
5):437–451.
Spenrath, F., Palzkill, M., Pott, A., and Verl, A. (2013).
Object recognition: Bin-picking for industrial use. In
IEEE ISR 2013, pages 1–3. IEEE.
Taheritanjani, S., Haladjian, J., and Bruegge, B. (2019).
Fine-grained visual categorization of fasteners in
overhaul processes. In 2019 5th International Confer-
ence on Control, Automation and Robotics (ICCAR),
pages 241–248. IEEE.
Taheritanjani, S., Schoenfeld, R., and Bruegge, B. Auto-
matic damage detection of fasteners in overhaul pro-
cesses.
Wang, P., Chen, P., Yuan, Y., Liu, D., Huang, Z., Hou, X.,
and Cottrell, G. (2018). Understanding convolution
for semantic segmentation. In 2018 IEEE winter con-
ference on applications of computer vision (WACV),
pages 1451–1460. IEEE.
Wu, Y., Marks, T., Cherian, A., Chen, S., Feng, C., Wang,
G., and Sullivan, A. (2019). Unsupervised joint 3d ob-
ject model learning and 6d pose estimation for depth-
based instance segmentation. In Proceedings of the
IEEE International Conference on Computer Vision
Workshops, pages 0–0.
ICPRAM 2020 - 9th International Conference on Pattern Recognition Applications and Methods
500