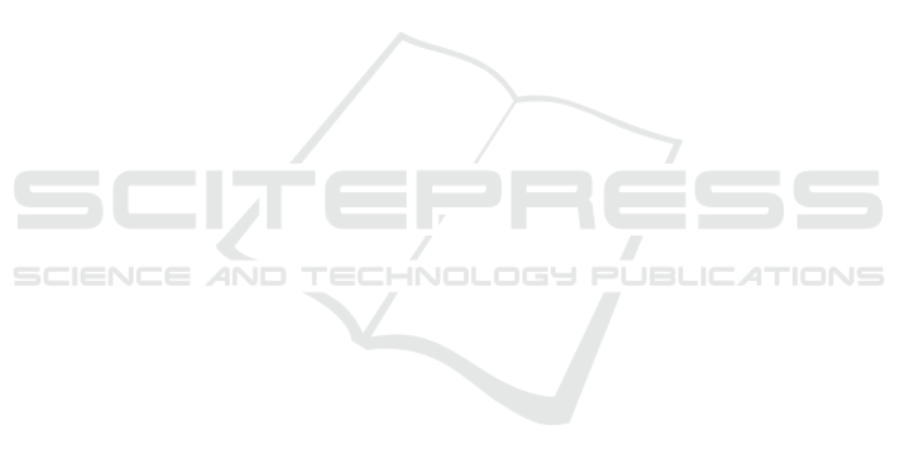
tool the AutomationML Editor and measured with
KLM, needed steps for both approaches. The out-
come showed promising results in terms of mod-
eling efficiency in favor of our software prototype.
However, the results must be validated also with
more complex use cases and under different as-
pects, such as understandability.
Limitations. There are certain limitations and
threats to validity to this work: The prototype in
its current form, only covers the discussed scenar-
ios, however there are more advanced and com-
plex use cases, that are necessary for the daily work
and to support true round-trip engineering in PSE.
The generated test data was relatively simple and
small in comparison to real-world production sys-
tem data sets. Furthermore, it does not cover the
whole functionality of the AML standard, such as
SystemUnitClasses, RoleClasses, and references
to external resources. Furthermore, the visual aspects
for graph-based model inspection need to be tested if
they produce better results for model comprehension
of users.
Concerning the evaluation, KLM is a static calcu-
lation method. This validation does not test the data
with real participants, regarding usability. These lim-
itations should be covered in future work to ensure
increased validity for the results.
7 CONCLUSION AND FUTURE
WORK
Graph-based model inspection approaches in PSE
have not gained much attention so far, although there
are various benefits of implementing such a visuali-
sation: Such tool-based solutions can provide a bet-
ter understanding of project relationships and depen-
dencies between disciplines. The holistic overview
over multiple disciplines has the potential to decrease
defects and effort for data integration, such as con-
sistency and change checking. Consequently, data
quality and chances for successful completion of PSE
projects could be increased.
We introduced and investigated PSE scenarios and
InfoVis methods to improve the model perception in
PSE. Our proposed solution has the mentioned draw-
backs and shortcomings that need to be addressed in
future research. However, the identified gaps in re-
search, the requirements for visualising engineering
data and proof of concept in form of a developed soft-
ware prototype contribute to the field of model-based
engineering and can be a foundation for future re-
search. Our results are an initial step to gather knowl-
edge in the area of applying InfoVis methods in the
PSE domain to improve the model quality in a multi-
disciplinary industrial context.
Future Work. To overcome the limitations of the
basic test data and to evaluate the findings of this pa-
per additional research is needed. Suggestions for
future work is to extend and configure the prototype
with special test data-sets for each discussed use case
and to collect empirical data instead of relying on the
KLM method. Usability tests or field studies would
be viable approaches and also the testing of other vi-
sualisation techniques could add more value to the re-
search. In this work we focused on visualising the
project hierarchy, to make it more useful for real-
world applications, more functions of AML should be
added.
ACKNOWLEDGEMENT
The financial support by the Christian Doppler Re-
search Association, the Austrian Federal Ministry for
Digital & Economic Affairs and the National Foun-
dation for Research, Technology and Development is
gratefully acknowledged.
REFERENCES
Biffl, S., L
¨
uder, A., Rinker, F., and Waltersdorfer, L.
(2019). Efficient engineering data exchange in multi-
disciplinary systems engineering. In International
Conference on Advanced Information Systems Engi-
neering, pages 17–31. Springer.
Biffl, S., Schatten, A., and Zoitl, A. (2009). Integration of
heterogeneous engineering environments for the au-
tomation systems lifecycle. In 2009 7th IEEE Inter-
national Conference on Industrial Informatics, pages
576–581. IEEE.
Bordeleau, F., Liebel, G., Raschke, A., Stieglbauer, G., and
Tichy, M. (2017). Challenges and research directions
for successfully applying mbe tools in practice. In
MODELS (Satellite Events), pages 338–343.
Card, S. K., Mackinlay, J. D., and Shneiderman, B., editors
(1999). Readings in Information Visualization: Using
Vision To Think. Morgan Kaufmann Publishers Inc.,
San Francisco, CA, USA.
Card, S. K., Moran, T. P., and Newell, A. (1983). The psy-
chology of human-computer interaction, volume 15.
CRC Press.
Drath, R. (2009). Datenaustausch in der Anlagenplanung
mit AutomationML: Integration von CAEX, PLCopen
XML und COLLADA. Springer-Verlag.
MODELSWARD 2020 - 8th International Conference on Model-Driven Engineering and Software Development
124