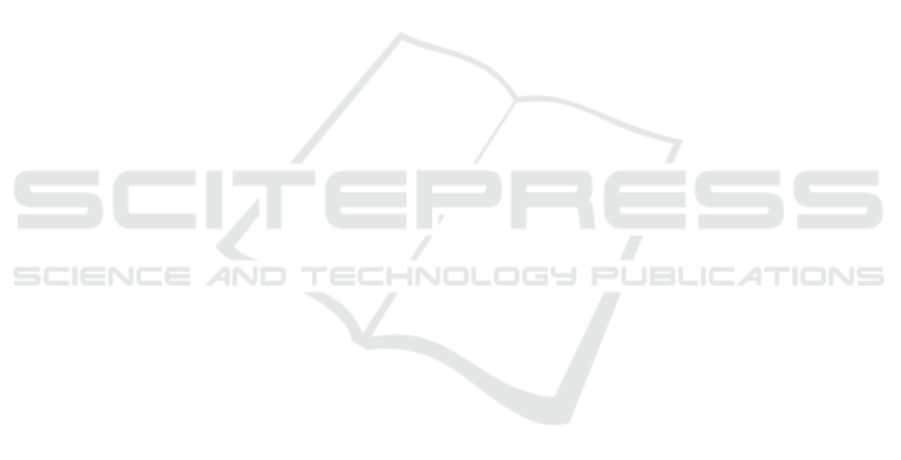
Harbour, M. G., Garc
´
ıa, J. G., Guti
´
errez, J. P., and Moyano,
J. D. (2001). Mast: Modeling and analysis suite for
real time applications. In Real-Time Systems, 13th Eu-
romicro Conference on, 2001., pages 125–134. IEEE.
Henia, R., Hamann, A., Jersak, M., Racu, R., Richter, K.,
and Ernst, R. (2005). System level performance anal-
ysis – the symta/s approach. IEE Proceedings – Com-
puters and Digital Techniques, 152(2):148–166.
Henzinger, T. A., Horowitz, B., and Kirsch, C. M. (2001).
Giotto: A time-triggered language for embedded pro-
gramming. In Proceedings of the 1st International
Workshop on Embedded Software, EMSOFT ’01.
IBM Software (2019). Ibm rational rhapsody developer.
https://www.ibm.com/software/products/en/ratirhap.
Accessed Nov 2019.
INCHRON (2019). chronSIM.
https://www.inchron.com/tool-suite/chronsim.html.
Nov 2019.
Iqbal, M. Z., Ali, S., Yue, T., and Briand, L. (2012). Ex-
periences of Applying UML/MARTE on Three Indus-
trial Projects. In Proceedings of the 15th International
Conference MODELS’12.
Iyenghar, P., Noyer, A., Engelhardt, J., Pulverm
¨
uller, E.,
and Westerkamp, C. (2016). End-to-end path delay
estimation in embedded software involving heteroge-
neous models. In 11th IEEE Symposium on Industrial
Embedded Systems, SIES, 2016, pages 183–188.
Iyenghar, P. and Pulvermueller, E. (2018). A model-driven
workflow for energy-aware scheduling analysis of iot-
enabled use cases. IEEE Internet of Things Journal,
5(6):4914–4925.
Jianqiang, W., Shengbo, L., Xiaoyu, H., and Keqiang,
L. (2010). Driving simulation platform applied to
develop driving assistance systems. IET Intelligent
Transport Systems, 4(2):121–127.
Kaynar, D. K., Lynch, N., Segala, R., and Vaandrager, F.
(2003). Timed I/O Automata: A Mathematical Frame-
work for Modeling and Analyzing Real-Time Sys-
tems. In Proceedings of the 24th IEEE RTSS.
Kim, J. H., Kang, I., Kang, S., and Boudjadar, A.
(2016). A process algebraic approach to resource-
parameterized timing analysis of automotive software
architectures. IEEE Transactions on Industrial Infor-
matics, 12(2):655–671.
Kirner, R., Lang, R., Puschner, P., and Temple, C. (2000).
Integrating WCET Analysis into a Matlab/Simulink
Simulation Model. In Proceedings of 16th IFAC Work-
shop on Distributed Computer Control Systems 2000.
Klobedanz, K., Kuznik, C., Thuy, A., and Mueller,
W. (2010). Timing modeling and analysis for
AUTOSAR-based software development: a case
study. In Proceedings of Conference on Design, Au-
tomation and Test in Europe, pages 642–645. Euro-
pean Design and Automation Association.
Kusano, K. D. and Gabler, H. (2011). Method for estimat-
ing time to collision at braking in real-world, lead ve-
hicle stopped rear-end crashes for use in pre-crash sys-
tem design. SAE International Journal of Passenger
Cars – Mechanical Systems, 4(1):435–443.
Luxoft – Symtavision (2019). Timing analysis so-
lutions. https://auto.luxoft.com/uth/timing-analysis-
tools/. Accessed Nov 2019.
Navet, N. and Simonot-Lion, F., editors (2009). Automotive
embedded systems handbook. CRC press.
Noyer, A., Iyenghar, P., Engelhardt, J., Pulvermueller, E.,
and Bikker, G. (2016). A model-based framework
encompassing complete workflow from specification
until validation of timing requirements in embedded
software systems. Software Quality Journal, pages 1–
31.
Peraldi, M. and Sorel, Y. (2008). From high-level modelling
of time in marte to realtime scheduling analysis. In
First International Workshop on Model Based Archi-
tecting and Construction of Embedded Systems.
Peraldi-Frati, M.-A., Blom, H., Karlsson, D., and Kuntz, S.
(2012). Timing modeling with autosar - current state
and future directions. In Design, Automation Test in
Europe Conference, DATE.
Petriu, D. C. (2013). Software Model-based Performance
Analysis, pages 139–166. John Wiley & Sons, Inc.
Scheickl, O., Ainhauser, C., and Gliwa, P. (2012). Tool sup-
port for seamless system development based on au-
tosar timing extensions. In Proceedings of Embedded
Real-Time Software Congress(ERTS).
Scheid, O. (2015). AUTOSAR Compendium, Part 1: Appli-
cation & RTE. CreateSpace Independent Publishing
Platform.
Singhoff, F., Legrand, J., Nana, L., and Marc
´
e, L. (2004).
Cheddar: a flexible real time scheduling framework.
In ACM SIGAda Ada Letters, volume 24, pages 1–8.
ACM.
van der Horst, R. and Hogema, J. (1993). Time-to-collision
and collision avoidance systems. In Proceedings of
the 6th ICTCT Workshop.
Zhao, Y., Liu, J., and Lee, E. A. (2007). A program-
ming model for time-synchronized distributed real-
time systems. In Proceedings of 13th IEEE Real Time
and Embedded Technology and Applications Sympo-
sium, RTAS, pages 259–268.
MODELSWARD 2020 - 8th International Conference on Model-Driven Engineering and Software Development
38