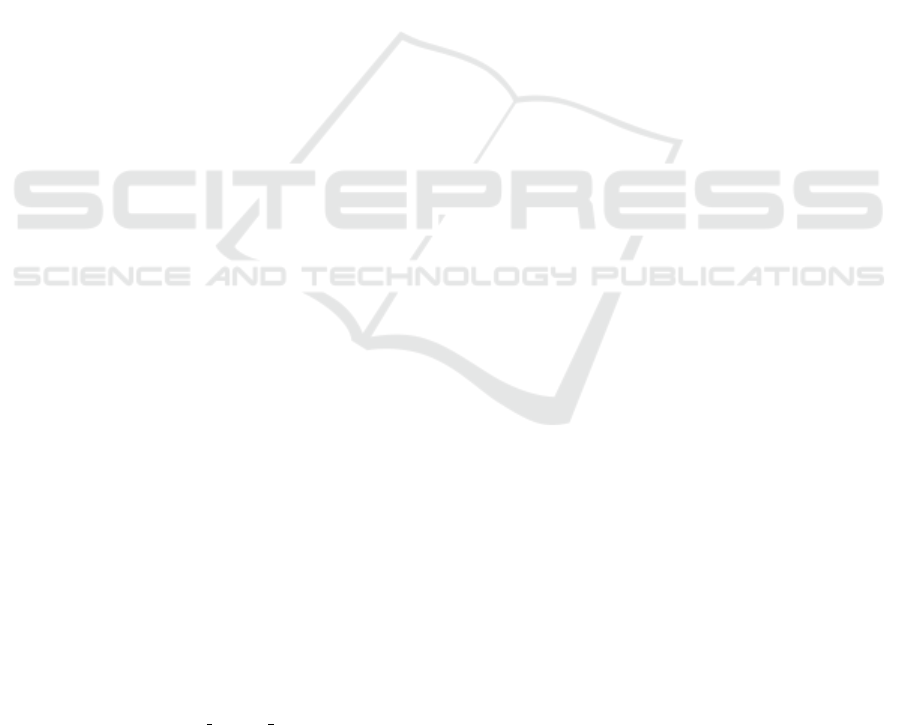
system by actively correcting for all types of nomi-
nal variations, while offering increased resistance to
possible cyberattacks on the process equipment.
REFERENCES
An, J. and Cho, S. (2015). Variational autoencoder based
anomaly detection using reconstruction probability.
Special Lecture on IE, 2(1).
Boyer, S. A. (2009). SCADA: Supervisory Control And
Data Acquisition. International Society of Automa-
tion, USA, 4 edition. ISBN 1936007096.
Delsanter, J. (1992). Six sigma. Managing Service Quality,
2(4).
Deming, W. E. (1986). Out of Crisis. MIT Center for Ad-
vanced Engineering Study, Cambridge, MA, USA.
Deming, W. E. and Renmei, N. K. G. (1951). Elementary
Principles of the Statistical Control of Quality; a Se-
ries of Lectures. Tokyo, Nippon Kagaku Gijutsu Rem-
mei, Tokyo, Japan.
Denton, D. (1991). Lessons on competitiveness: Motorola’s
approach. Production and Inventory Management
Journal, 32(3).
Fujimoto, S., van Hoof, H., and Meger, D. (2018). Ad-
dressing function approximation error in actor-critic
methods. arXiv preprint arXiv:1802.09477.
Goodfellow, I., Bengio, Y., and Courville, A. (2016). Deep
Learning. MIT Press, Cambridge, MA, USA. ISBN
0262035618. http://www.deeplearningbook.org.
Goodfellow, I. J., Pouget-Abadie, J., Mirza, M., Xu, B.,
Warde-Farley, D., Ozair, S., Courville, A., and Ben-
gio, Y. (2014). Generative adversarial nets. In
Proceedings of the 27th International Conference on
Neural Information Processing Systems - Volume 2,
NIPS’14, pages 2672–2680, Cambridge, MA, USA.
MIT Press.
Hochreiter, S. and Schmidhuber, J. (1997). Long short-term
memory. Neural Computation, 9(8):1735—-1780.
Johnson, M., Schuster, M., Le, Q. V., Krikun, M., Wu, Y.,
Chen, Z., Thorat, N., Vi
´
egas, F., Wattenberg, M., Cor-
rado, G., Hughes, M., and Dean, J. (2017). Google’s
multilingual neural machine translation system: En-
abling zero-shot translation. Transactions of the Asso-
ciation for Computational Linguistics, 5:339–351.
Kalman, R. E. (1960). A new approach to linear filtering
and prediction problems. Journal of basic Engineer-
ing, 82(1):35–45.
Karnouskos, S. (2011). Stuxnet worm impact on indus-
trial cyber-physical system security. In 37th Annual
Conference of the IEEE Industrial Electronics Society
(IECON 2011), Melbourne, Australia. http://papers.
duckdns.org/files/2011 IECON stuxnet.pdf.
Krizhevsky, A., Sutskever, I., and Hinton, G. E. (2012).
Imagenet classification with deep convolutional neu-
ral networks. In Pereira, F., Burges, C. J. C., Bot-
tou, L., and Weinberger, K. Q., editors, Advances
in Neural Information Processing Systems 25, pages
1097–1105. Curran Associates, Inc. https://bit.ly/
39PWOAb.
Kullback, S. (1959). Information Theory and Statistics.
John Wiley & Sons.
Kullback, S. and Leibler, R. (1951). On information
and sufficiency. Annals of Mathematical Statistics,
22(1):79–86.
Laughton, M. and Warne, D., editors (2003). Electrical En-
gineer’s Reference Book, chapter 16. Newnes, 16 edi-
tion. ISBN 0750646373.
Lillicrap, T. P., Hunt, J. J., Pritzel, A., Heess, N., Erez, T.,
Tassa, Y., Silver, D., and Wierstra, D. (2015a). Contin-
uous control with deep reinforcement learning. arXiv
preprint arXiv:1509.02971.
Lillicrap, T. P., Hunt, J. J., Pritzel, A., Heess, N., Erez,
T., Tassa, Y., Silver, D., and Wierstra, D. (2015b).
Continuous control with deep reinforcement learning.
arXiv preprint arXiv:1509.02971.
Malhotra, P., Ramakrishnan, A., Anand, G., Vig, L., Agar-
wal, P., and Shroff, G. (2016). LSTM-based encoder-
decoder for multi-sensor anomaly detection. arXiv
preprint arXiv:1607.00148.
Russell, S. and Norvig, P. (2010). Artificial Intelligence: A
Modern Approach. Prentice Hall, Upper Saddle River,
NJ, USA, 3 edition. ISBN 0136042597. http://aima.
cs.berkeley.edu/.
Sakurada, M. and Yairi, T. (2014). Anomaly detection
using autoencoders with nonlinear dimensionality re-
duction. In Proceedings of the MLSDA 2014 2nd
Workshop on Machine Learning for Sensory Data
Analysis, page 4. ACM.
Schulman, J., Wolski, F., Dhariwal, P., Radford, A., and
Klimov, O. (2017). Proximal policy optimization al-
gorithms. arXiv preprint arXiv:1707.06347.
Sutton, R. S. and Barto, A. G. (2018). Reinforcement
Learning: An Introduction. MIT Press, Cambridge,
MA, USA, 2 edition. ISBN 0262039249. http://
incompleteideas.net/book/the-book-2nd.html.
Thrun, S., Burgard, W., and Fox, D. (2005). Probabilistic
robotics. MIT press.
Zhou, C. and Paffenroth, R. C. (2017). Anomaly detec-
tion with robust deep autoencoders. In Proceedings of
the 23rd ACM SIGKDD International Conference on
Knowledge Discovery and Data Mining, pages 665–
674. ACM.
ICISSP 2020 - 6th International Conference on Information Systems Security and Privacy
670