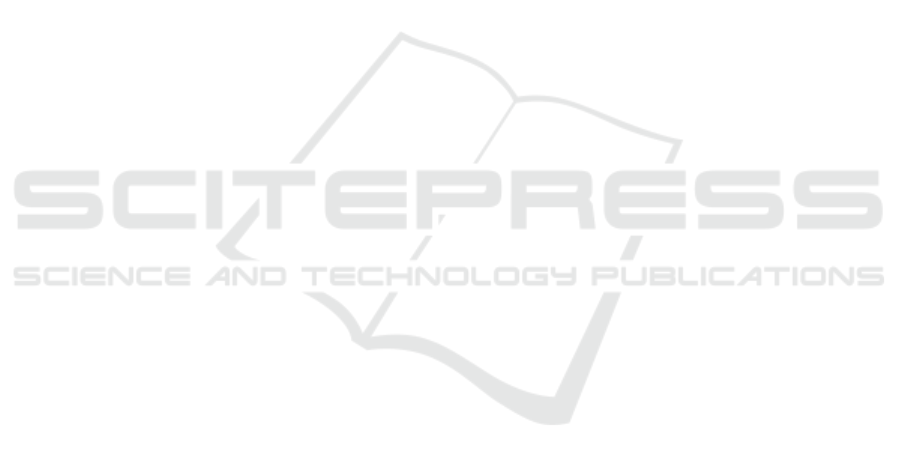
ing) that are useful to model contiguity and visibility
requirements. In the second step, we used the cre-
ated 2D layers to build 3D pallets by using a sim-
ple greedy strategy. Extensive computational exper-
iments on real-world instances proved the effective-
ness of the proposed heuristic.
To evaluate the extreme points, we proposed sev-
eral fitness evaluation functions, and found that the
one based on the concept of Bounding Box gave bet-
ter results than the other ones on average. We also
analyzed the influence of some constraints (e.g., rota-
tion and visibility) when tailoring our heuristic to ba-
sic 2D packing heuristics from the literature, gaining
interesting insights in the difficulty of the real-world
instances that we tested.
As future work, we intend to develop metaheuris-
tic algorithms to try to enhance the quality of the solu-
tions that we generated so far. We also intend to pro-
pose formal mathematical models to express the con-
cept of contiguity and visibility of items, thus filling a
gap in the existing literature. We are also interested in
studying a more complex problem that joins together
the pallet building problem with the vehicle routing
problem, so as to consider the location of pallets into
trucks and their delivery to the clients that required
them. In this case, we should extend the concept of
family, not only relying on the geometric characteris-
tics of the items, but adding new criteria of separation,
in order to help both problems (packing and delivery)
to increase the quality of the final optimization.
ACKNOWLEDGEMENTS
We thank the University of Parma and the University
of Modena and Reggio Emilia (Italy) for the financial
support to this work.
REFERENCES
Alonso, M., Alvarez-Valdes, R., Iori, M., and Parre
˜
no,
F. (2019). Mathematical models for multi container
loading problems with practical constraints. Comput-
ers & Industrial Engineering, pages 722–733.
Alonso, M., Alvarez-Valdes, R., Iori, M., Parre
˜
no, F., and
Tamarit, J. (2017). Mathematical models for multi
container loading problems. OMEGA 66, pages 106–
117.
Alonso, M., Alvarez-Valdes, R., Parre
˜
no, F., and Tamarit, J.
(2016). Algorithms for pallet building and truck load-
ing in an interdepot transportation problem. Mathe-
matical Problems in Engineering, page 11.
Alvarez-Valdes, R., Parre
˜
no, F., and Tamarit, J. (2008). Re-
active GRASP for the strip-packing problem. Com-
puters & Operations Research, 35:1065–1083.
Bischoff, E. and Ratcliff, M. (1995). Issues in the devel-
opment of approaches to container loading. Omega,
23:377–390.
Bortfeldt, A. and Gehring, H. (2001). A hybrid genetic al-
gorithm for the container loading problem. European
Journal of Operational Research, 131:143–161.
Bortfeldt, A. and W
¨
ascher, G. (2013). Constraints in con-
tainer loading – a state-of-the-art review. European
Journal of Operational Research, 229:1–20.
Burke, E., Kendall, G., and Whitwell, G. (2004). A New
Placement Heuristic for the Orthogonal Stock-Cutting
Problem. Operations Research, 52:655–671.
Chazelle, B. (1983). The Bottomn-Left Bin-Packing
Heuristic: An Efficient Implementation. IEEE Trans-
actions on Computers, C-32:697–707.
Crainic, T., Perboli, G., and Tadei, R. (2008). Extreme
point-based heuristics for three-dimensional bin pack-
ing. INFORMS J. on Computing, 20:368–384.
Crainic, T., Perboli, G., and Tadei, R. (2012). Recent Ad-
vances in Multi-Dimensional Packing Problems. In
Volosencu, C., editor, New Technologies – Trends, In-
novations and Research. IntechOpen, Rijeka.
Delorme, M., Iori, M., and Martello, S. (2017). Logic
based benders’ decomposition for orthogonal stock
cutting problems. Computers & Operations Research,
78:290–298.
Egeblad, J., Garavelli, C., Lisi, S., and Pisinger, D. (2010).
Heuristics for container loading of furniture. Euro-
pean Journal of Operational Research, 200:881–892.
Fekete, S. and Schepers, J. (1997). A new exact algorithm
for general orthogonal d-dimensional knapsack prob-
lems. In Algorithms — ESA ’97, pages 144–156.
Haessler, R. and Talbot, F. (1990). Load planning for ship-
ments of low density products. European Journal of
Operational Research, 44:289–299.
Hopper, E. and Turton, B. (1998). Application of Genetic
Algorithms to Packing Problems – A Review. In Soft
Computing in Engineering Design and Manufactur-
ing, pages 279–288.
Imahori, S. and Yagiura, M. (2010). The best-fit heuristic
for the rectangular strip packing problem: An efficient
implementation and the worst-case approximation ra-
tio. Computers & Operations Research, 37:325–333.
Iori, M., Lima, V., Martello, S., Miyazawa, F., and Monaci,
M. (2019). Two-dimensional cutting and packing:
Problems and solution techniques. Technical report,
University of Bologna.
Iori, M. and Martello, S. (2010). Routing problems with
loading constraints. TOP, 18:4–27.
Iori, M. and Martello, S. (2013). An annotated bibliography
of combined routing and loading problems. Yugoslav
Journal of Operations Research, 23:311–326.
J
´
ozefowska, J., Pawlak, G., Pesch, E., Morze, M., and
Kowalski, D. (2018). Fast truck-packing of 3d boxes.
Engineering Management in Production and Services,
10:29–40.
Leung, S., Zhang, D., and Sim, K. (2011). A two-stage
intelligent search algorithm for the two-dimensional
strip packing problem. European Journal of Opera-
tional Research, 215:57–69.
Solution of a Practical Pallet Building Problem with Visibility and Contiguity Constraints
337