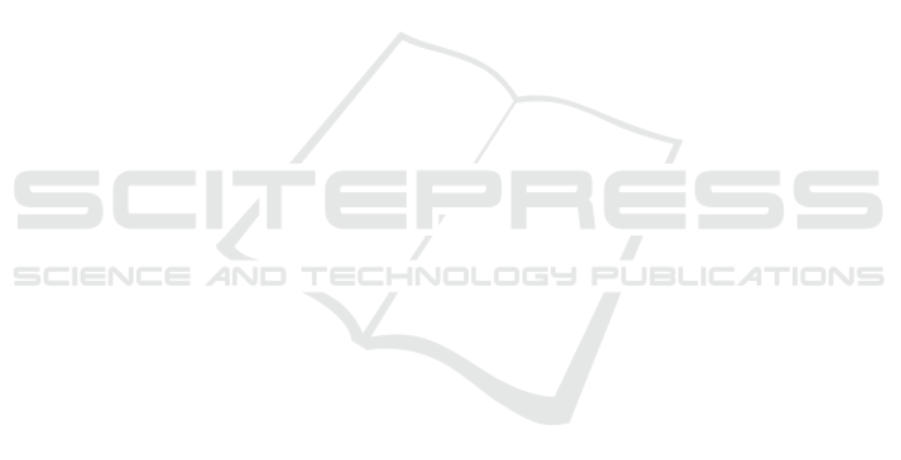
2 THE HPDC USE-CASE
The high pressure die casting (HPDC) process is
a discontinuous permanent mold based production
technology that is primarily used to cast light met-
als such as aluminum and magnesium alloys. One
process cycle typically lasts around 60 s for the pro-
duction of one casting and consists of multiple sub-
cycle phases in which the molten metal is injected into
a cavity (die), subsequently solidified and ejected as
a solid part afterwards. Parts made with the HPDC
process are frequently used for high volume automo-
tive applications including power train components,
such as transmission housings, but also crash-relevant
structural parts like shock towers.
A HPDC cell does not only include the HPDC ma-
chine itself, but also various auxiliary systems which
are used to enable a highly automated production sys-
tem which requires an adequate information network
(Rix et al., 2016). A common machine consists of the
shot end, which uses a hydraulic drive system to inject
molten metal into the cavity and to keep the metal un-
der high pressure during solidification. The machine
is supported by external cell components such as a
molten metal holding furnace, a ladle system to trans-
fer the metal to the machine, multiple oil- or water-
based thermal regulation units that deliver coolant to
the die, a vacuum system that evacuates the cavity
shortly before injection, and a spraying system to ap-
ply a release agent on the hot work steel surface of
the die. These auxiliary systems are used at differ-
ent points in time or sub-cycle phases of the over-
all cycle. Most sensors provide values continuously
throughout the cycle, one could gather all these values
simply by assigning a constant sampling rate indepen-
dent of the machine’s current state. The assignment
of this constant sampling rate does impose limitations
on the quality of the data acquisition. The overall cy-
cle duration and the times of the sub-cycle phases can
vary either due to adjustments to the process control
by the operator or production interruptions caused by
unstable process conditions. A constant sampling rate
over the full cycle limits the ability to differentiate
between sub-cycle phases. For this reason it is ben-
eficial to detect the transition from one sub-cycle to
the consecutive cycle phase, and to have the ability
to adjust sampling rates or to transmit the sampled
values only if the change of the absolute value is rel-
evant from an engineering stand point. For example,
the molten metal is dosed into a reservoir, referred to
as the shot chamber, and then injected by a plunger.
The plunger injection phase can be differentiated in
the slow shot and the fast shot. The dosing proce-
dure usually lasts around 4-7 s, the slow shot is in
the 750-1500 ms range and the fast shot which fills
the cavity typically lasts around 25-100 ms. Hori-
zontal real time controlled cold chamber HPDC ma-
chines have advanced PLCs and a hydraulic system
that enable the replication of these parameters. Due
to changes of the state of the machine (wear, aging
or losses of fluids, high operating temperatures) how-
ever irregularities and fluctuations can be introduced.
It is important to enable a clear reflection of these
changes within the data captured over time from the
machine. This can only be realized by a transition
from the constant acquisition approach to a more so-
phisticated, data-driven, approach, because sampling
rates without variable adjustments between sub-cycle
phases cannot achieve this objective. Improved detec-
tion and documentation of undesired state changes is
the first step towards continuous improvement of the
HPDC process.
3 RELATED WORK
The context of this paper is shown in Figure 1, which
depicts the traditional extract-transform-load (ETL)
as well as the more modern extract-load-transform
(ELT) process. Solutions with relational data mod-
els, like data warehouses, first transform extracted
data into their designated schema and then load it
(Quix, 2003; Quix et al., 2016; Vassiliadis and Sim-
itsis, 2009). In contrast, data lakes and other NoSQL
systems make data quickly available by first loading it
and then in-place transforming it later in time (ELT).
The data collection approach we propose however
tackles the OPC UA data collection within the ex-
traction phase and thus is independent from the cho-
sen approach ETL or ELT, because either one starts
with the extraction (E). Therefore, we focus on related
work on the extraction phase, OPC UA in particular,
and skip the not directly related load and transform
steps in this section.
Common data collection systems using OPC UA
(Hannelius et al., 2008) either permanently read data
(polling) or use built-in subscription functionalities.
Polling is simple to implement as the client actively
reads data from the server, typically in fixed time in-
tervals. An example would be to collect a certain
temperature value every 2000 ms. Depending on the
actual value pattern, this approach can be very in-
efficient because of two reasons: It can miss value
changes if the polling interval does not hit them, or
it collects the same value over and over again for in-
frequently changing sensor values. The latter can be
tackled by decreasing the polling frequency, which
worsens the former, and vice versa.
When to Collect What? Optimizing Data Load via Process-driven Data Collection
221