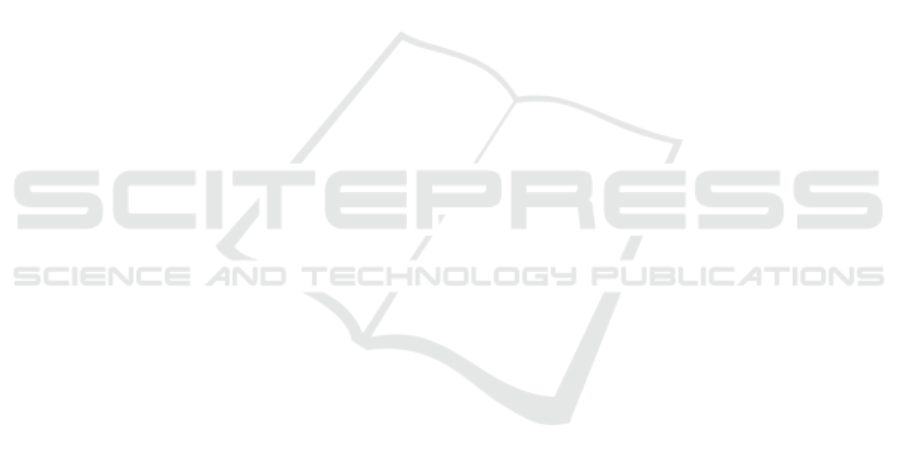
separation distance. In method d), the robot veloc-
ity is limited according to the body part that is near-
est to the robot. Neither of both operation methods
admits economically efficient human-robot collabora-
tion. Aiming at an economically efficient solution that
respects the safety regulations, the concept of a col-
laboration framework is proposed in this paper com-
bining operation methods c) and d). To this end, the
robot velocity is adapted according to the body part
closest to the robot TCP (according to method c)) so
to ensure the power and force limitations (according
to d)).
At first, it is mandatory to guarantee, that the in-
stantaneous robot velocity will not lead to a viola-
tion of the force and pressure thresholds of ISO/TS
15066, i.e. to be in accordance with the regulations of
method d).
In order to exclude collisions while the robot ve-
locity is decreased to an ISO conform limit, it is nec-
essary to take into account the protective separation
distance between the operator and the robot, which is
described in method c) as
S
p
(t
0
) = S
h
+ S
r
+ S
s
+C + Z
d
+ Z
r
,
(2)
with S
p
(t
0
) being the protective separation distance
at current time t
0
. In the following the contributions
to the protective separation distance (2) are described
in more detail.
The contribution due to the operator’s motion is
given by
S
h
=
Z
t
0
+t
r
t
0
v
h
·dt ,
(3)
with t
r
being the reaction time of the robot system
and v
h
being the directed speed of humans within
the collaborative environment. Since the velocities
of humans (respectively of their body parts) cannot
be monitored with the investigated sensor technolo-
gies, a constant velocity of 1.6 m/s for separating dis-
tances > 0.5 m and 2.0 m/s for distances below 0.5
m according to ISO 13855 (ISO 13855, 2010) are as-
sumed.
S
r
is the contribution due to the robot’s reaction
time, i.e. the distance that arises due to the robot’s
movement towards or away from the human, starting
from the moment when a human comes too close to
the robot until the safety control system initializes a
stop. In the course of a more generic investigation
of the robot’s influence towards the separation dis-
tance, the planned robot path and the adjusted veloc-
ity profile have to be studied more carefully. When-
ever a change of maximal robot velocities occurs, the
velocity contribution towards or away from the hu-
man effects the separation distance. Subsequently, it
is mandatory to determine the influence of the veloc-
ity change within the robot’s reaction time. The in-
vestigated use case does not tend to have large robot
movements towards the human and therefore the in-
fluence of the robot motion is not studied within the
proposed analysis.
In the specification, the expression S
s
corresponds
to the distance the robot TCP travels after a halt
command has been issued until the robot has finally
stopped. As the proposed framework only takes into
account velocity adjustments and does not consider
the stopping of the robot, this term can be omitted in
the analysis.
The intrusion distance C is defined in ISO 13855
as the distance a part of the body can permeate the
sensing field before being detected. It is formulated
as
C = 8(d −14) ,
(4)
with d being the sensor detection capacity [mm].
Since no opto-electronic safety light-beam system
is used, this expression can be neglected within
the framework due to a sensor detection capac-
ity < 40 mm as well.
Finally, Z
d
and Z
r
are uncertainty contributions
corresponding to the position uncertainty of the op-
erator and the position uncertainty of the robot sys-
tem. In this paper these uncertainties are not ana-
lyzed quantitatively, but rather qualitative statements
are given and possible uncertainties of the estimation
of the human movement are considered.
Thus, the main focus of this analysis lies on the
consequences of the human motion for the needed
separation distances for an ISO compatible exploita-
tion of maximal robot velocities. As the specification
implies constant human velocities, the main parame-
ter which characterizes the separation distance is the
reaction time of the robot system t
r
.
4 LATENCY ANALYSIS
The main feature of the proposed framework proto-
type is the reduction of the robot velocity according
to the human body part closest to the robot. Since the
robot reaction to a human action will not be executed
instantaneously, the appearing reaction time t
r
must
be characterized carefully. In the following, the terms
reaction time t
r
and latency t
Lat
will be used synony-
mously.
In order to detect possible changes in the envi-
ronment a sensor system has to be used, which takes
some time t
Cap
to capture recent information from the
environment.
Accordingly, the gained information has to un-
dergo some processing steps with total processing
Analysis of Different Human Body Recognition Methods and Latency Determination for a Vision-based Human-robot Safety Framework
According to ISO/TS 15066
371