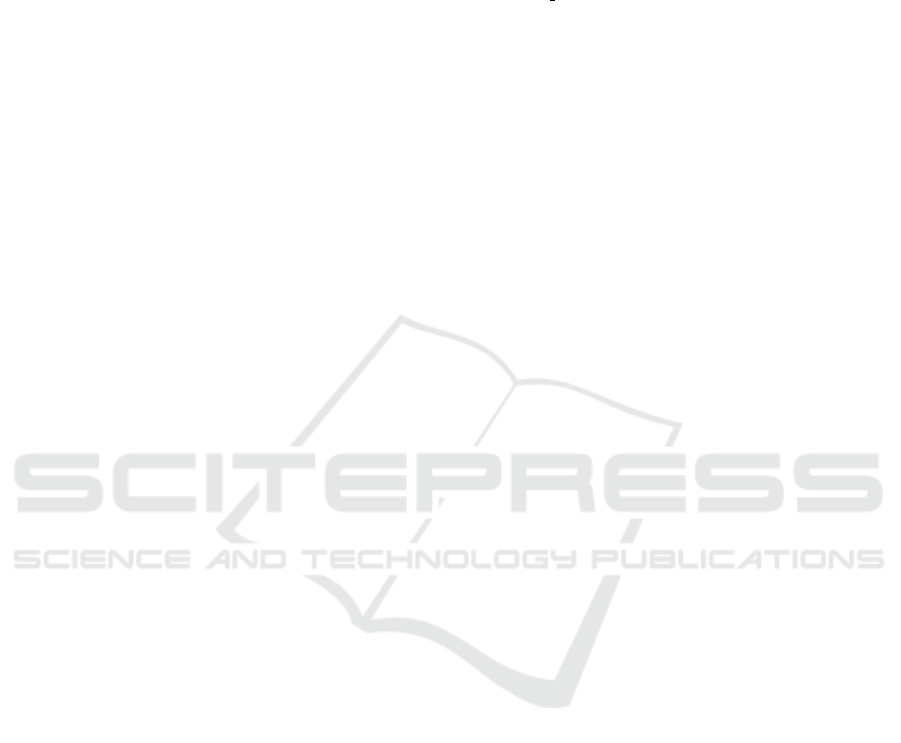
As an outlook, we mention that data enables much
more than creating data-driven services: data is trans-
forming car manufacturers from traditional engineer-
ing companies to data-driven companies. This indi-
cates that not only service creation but also car devel-
opment in general is progressively based on data.
REFERENCES
Aeberhard, M., K
¨
uhbeck, T., and et al. (Retrieved May
6, 2019). Automated driving with ros at bmw.
https://roscon.ros.org/2015/presentations/ROSCon-
Automated-Driving.pdf.
Ardelt, M., Coester, C., and Kaempchen, N. (2012). Highly
automated driving on freeways in real traffic using a
probabilistic framework. IEEE Transactions on Intel-
ligent Transportation Systems, 13(4):1576–1585.
Arena, F. and Pau, G. (2019). An overview of vehicular
communications. Future Internet, 11(2).
BMW GROUP (Retrieved November 19, 2018). BMW
group launches BMW cardata: new and innova-
tive services for customers, safely and transpar-
ently. https://www.press.bmwgroup.com/global/
article/detail/T0271366EN/bmw-group-launches-
bmw-cardata:-new-and-innovative-services-for-
customers-safely-and-transparently?language=en.
Christ, M., Braun, N., Neuffer, J., and Kempa-Liehr, A. W.
(2018). Time series feature extraction on basis of scal-
able hypothesis tests (tsfresh a python package). Neu-
rocomputing, 307:72 – 77.
Geron, A. (2017). ”Hands-on machine learning with
scikit-learn & tensorflow”. O’Reilly Media, Inc., Se-
bastopol, CA, USA.
Glattes, K. (2016). ”Der Konkurrenz ein Kundenerleb-
nis voraus: Customer Experience Management –
111 Tipps zu Touchpoints, die Kunden begeistern”.
Springer.
Guyon, I., Gunn, S., Nikravesh, M., and Zadeh, L. (2006).
”Feature Extraction: Foundations and Applications”.
Studies in Fuzziness and Soft Computing. Springer.
Guyon, I., Gunn, S., Nikravesh, M., and Zadeh, L. (2008).
”Feature Extraction: Foundations and Applications”.
Studies in Fuzziness and Soft Computing. Springer.
Huber, W., Steinle, J., and Marquardt, M. (2008). Der
Fahrer steht im Mittelpunkt - Fahrerassistenz Aktive
Sicherheit bei der BMW Group. Integrierte Sicher-
heit und Fahrerassistenzsysteme, 2048:123–138.
Immonen, A., Ovaska, E., Kalaoja, J., and Pakkala, D.
(2016). A service requirements engineering method
for a digital service ecosystem. Service Oriented
Computing and Applications, 10(2):151–172.
Immonen, A., Ovaska, E., and Paaso, T. (2018). Towards
certified open data in digital service ecosystems. Soft-
ware Quality Journal, 26(4):1257–1297.
Kaiser, C., Stocker, A., and Viscusi, G. (2017). Digi-
tal vehicle ecosystems and new business models: An
overview of digitalization perspectives. In Platform
Economy & Business Models workshop at i-KNOW
2017.
Kilian, R., Gauer, C., Stein, J., and Scherer, M. (Retrieved
March 7, 2020). Connected vehicles and the road
to revenue. https://image-src.bcg.com/Images/BCG-
Connected-Vehicles-and-the-Road-to-Revenue-Dec-
2017 tcm9-179631.pdf.
Koch, M. and B
¨
ack, T. (2018). Machine learning for
predicting the impact point of a low speed vehicle
crash. In 2018 17th IEEE International Conference on
Machine Learning and Applications (ICMLA), pages
1432–1437.
Koch, M., Wang, H., and B
¨
ack, T. (2018). Machine learn-
ing for predicting the damaged parts of a low speed
vehicle crash. In Proceedings of Thirteenth Inter-
national Conference on Digital Information Manage-
ment (ICDIM 2018), pages 179–184.
Liu, S., Li, L., Tang, J., Wu, S., and Gaudiot, J. L. (2017).
”Creating Autonomous Vehicle Systems”. Synthesis
Lectures on Computer Science. Morgan & Claypool
Publishers.
Matheus, K. and K
¨
onigseder, T. (2015). Automotive Ether-
net. Cambridge University Press.
Nilsson, N. J. (1969). A mobile automaton: An applica-
tion of artificial intelligence techniques. In 1st Inter-
national Conference on Template Production, pages
509–520.
Otonomo (Retrieved November 19, 2018). Are con-
sumers willing to share connected car data?
https://otonomo.io/are-consumers-willing-to-share-
connected-car-data/.
Robert Bosch GmbH (2014). ”Bosch Automotive Electrics
and Automotive Electronics: Systems and Compo-
nents, Networking and Hybrid Drive”. Springer,
Wiesbaden, 5th edition.
Schmidhuber, J. (Retrieved November 30, 2018). Prof.
Schmidhuber’s highlights of robot car history.
http://people.idsia.ch/∼juergen/robotcars.html.
Seiberth, G. and Gruendinger, W. (2018). Data-driven busi-
ness models in connected cars, mobility services &
beyond. In BVDW Research, volume 01.
Shearer, C. (2000). The crisp-dm model: the new blueprint
for data mining. J Data Warehouse, 5:13–22.
Spurgeon, C. (2000). ”Ethernet: The Definitive Guide”.
Definitive Guide Series. O’Reilly.
Spurgeon, C. and Zimmerman, J. (2013). ”Ethernet
Switches: An Introduction to Network Design with
Switches”. O’Reilly Media.
Stone, P., Brooks, R., and et al. (Retrieved Novem-
ber 5, 2018). Artificial intelligence and life in
2030. one hundred year study on artificial intel-
ligence: Report of the 2015-2016 study panel.
http://ai100.stanford.edu/2016-report.
Tsugawa, S., Yatabe, T., and et al. (1979). An automo-
bile with artificial intelligence. In Proceedings of the
6th International Joint Conference on Artificial Intel-
ligence - Volume 2, pages 893–895, San Francisco,
CA, USA. Morgan Kaufmann Publishers Inc.
Weill, P. and Woerner, S. L. (2014). Thriving in an increas-
ingly digital ecosystem. MIT sloan management re-
view, 56(4):27–34.
VEHITS 2020 - 6th International Conference on Vehicle Technology and Intelligent Transport Systems
52