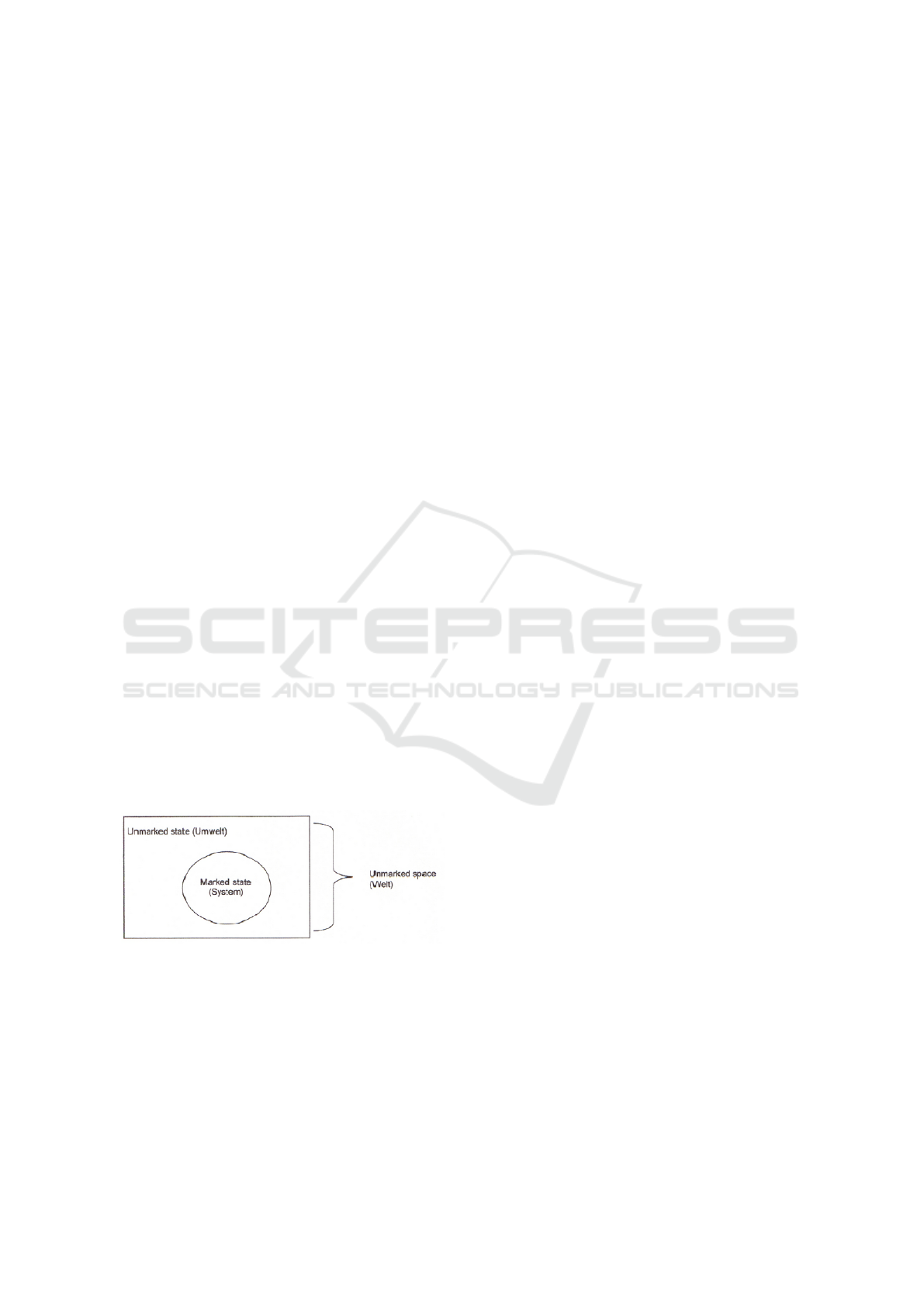
2 POSITION
The position of this paper is, that a simple logistic cell
model with one exemplary IoT-sensor application, is
adequate for implementing a scalable logistic process
and that this process can be hence demonstrated by a
simple physical model as well as a simulation model.
It is further suggested, that such a model can be eas-
ily scaled up and interconnected to depict an indus-
trial real-world logistic process. This process is ad-
missable because it can be interpreted as an orgiton
(Heiden et al., 2019) or a fractal program (Mandel-
brot, 1991) that is based on a core element (cell, orgi-
ton, fractal generator) that is multiplied and intercon-
nected.
3 A SCALABLE LOGISTIC CELL
The term ”logistic cell” can be derived from cyber-
netics and namely from the concept of cybernetic
systems, which are informational open and func-
tional closed (compare also (Weber, 2010), (Luh-
mann, 1997)). The system is defined as open if it has
an energetic and matter exchange with the external
world. The term ”external world” is taken in this con-
text from the theory of systems of George Spencer-
Brown, where the system appears from the separation
as a marked state (system) from the unmarked state
(external world) (Spencer-Brown, 2008) (q.v. Figure
1). An informational open system means that the ex-
change of information between this system and the
external world also exists. Functional closed means,
on the other hand, that the system can define a method
of communication with the external world indepen-
dently, using its functional organization.
Figure 1: Appearance of a system in the theory of George
Spencer-Brown (Spencer-Brown, 2008).
This term of a cybernetic system can be also applied
in the logistical context. For the definition of a lo-
gistic cell, the cybernetic system has to be modified
in that way, that it is defined as open for matter and
information because it always has an exchange in the
matter (material, transport and people flow) and in-
formation (external communication) levels. For that
these flows are flowing, they have to be powered by
energy. The unity of these natural components can be
determined through the Orgiton-Theory of Bernhard
Heiden et al. (Heiden et al., 2019), where it is called
“Orgiton”. If a system is defined as matter-open it
has also to be answered, which can be designated as a
border of this system. Concerning the logistic cell, the
boarders have to be so defined that they are pulled or
pushed by the observer. So, the system has to be con-
sidered by an observer, where a concrete object has to
be marked (marked state) as a cell. To specify it as
a technical model, functional interaction of the ”cell”
has to be considered. The main feature of this inter-
action is functional autonomy, which means that it is
operationally closed. It means, that the system can
work without external input requirements because it
has sufficient own functionality. On the other hand,
this system is determined as matter open, because it
e.g. pulls the information from the external world and
can communicate with other cells through matter, en-
ergy and information exchange. From that two main
features for the determination of logistic cell can be
taken:
(1) The autonomous self-sufficiency and the
(2) potential interaction with similar cells in their re-
spective matter, energy and information levels.
This second property of the here defined logistic cell
can be denoted as scalability. Scalability can be un-
derstood as the property of a logistic cell that allows
for applying volume and / or size changes in the sys-
tem. At the same time it has to be noticed, that the
borders of logistic cells are strongly connected with
the borders of flows, respectively, the bigger is the
Material-Energy-Information (MEI)-flow, the bigger
is the ”input surface” and with it tendentiously the cell
(q.v. Figure 2). Mathematically this can be described
by Equation (1), where G
2
and G
1
are respectively the
borders of flow and cell systems.
G
2
= f (G
1
) (1)
This means that the size of the connection of the
cells changes with the material flow e.g. Imagine a
pipeline, that has to be bigger when more material is
passing between two cells. This has a manifold of ap-
plications in nature, es e.g. in trees, blood vessels,
or lung branches (compare e.g. (Mandelbrot, 1991)).
The scalability of a cell is hence closely connected
to these to borders, border of the border in the pro-
jection, and the border of the cell. This is then a
self-referential structure, an orgiton of a higher or-
der, or according to Beno
ˆ
ıt Mandelbrot a fractal self-
referential structure.
To sum up the definition of the scalable logistic
cell: The scalable logistic cell is a material and func-
Scalable Logistic Cell RFID Witness Model
421