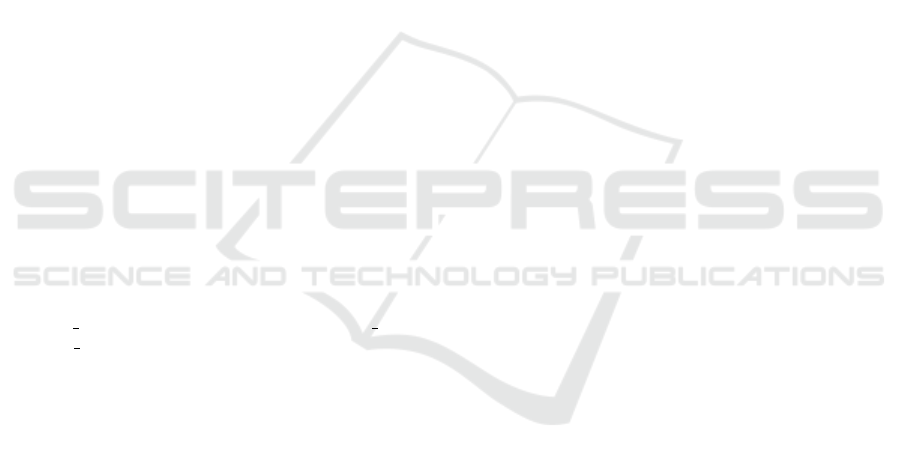
of the system. This additional knowledge at an early
stage could be very beneficial to the ECU develop-
ment process. For instance, the additional resources
(e.g. processor workload) could be utilized to further
extend or improve the functionality of AEBS (e.g. by
decreasing the period of the system end-to-end path)
or replace the ECU with a slower, cheaper version, to
save costs in mass production. At this development
stage, such design changes are still possible without
major consequences.
ACKNOWLEDGEMENTS
This work is supported by a grant (id:
KF2312004KM4) from BMWi-ZIM co-operation,
Germany and carried out in cooperation with Willert
Software Tools GmbH and SymtaVision GmbH.
The authors thank Stephan Wessels M.Sc (Uni
Osnabrueck) and Dr. Arne Noyer (Willert Software
Tools) and for their contribution with AEBS use case
and importer/exporter tool respectively.
REFERENCES
Anssi, S., G
´
erard, S., Kuntz, S., and Terrier, F. (2011). AU-
TOSAR vs. MARTE for enabling timing analysis of
automotive applications. In International SDL Forum,
pages 262–275. Springer.
AUTOSAR (2017). Specification of timing ex-
tensions. https://www.autosar.org/fileadmin/
user upload/standards/classic/4-3/AUTOSAR
TPS TimingExtensions.pdf. Accessed Jan 2020.
AUTOSAR (2018). Release 4.4.0: Methodology
and templates. https://www.autosar.org/standards/
classic-platform/classic-platform-440/. Accessed
Nov 2019.
Becker, M., Dasari, D., Mubeen, S., Behnam, M., and
Nolte, T. (2017). End-to-end timing analysis of cause-
effect chains in automotive embedded systems. Jour-
nal of Systems Architecture, 80:104 – 113.
Bhasker, J. (2010). A SystemC Primer. Star Galaxy.
Bucaioni, A., Cicchetti, A., Ciccozzi, F., Mubeen, S., and
Sj
¨
odin, M. (2017). A metamodel for the rubus com-
ponent model: Extensions for timing and model trans-
formation from east-adl. IEEE Access, 5:9005–9020.
EMF (2020). Eclipse modeling framework. https://www.
eclipse.org/modeling/emf/. Accessed Jan 2020.
Ficek, C., Feiertag, N., Richter, K., and Jersak, M. (2012).
Applying the AUTOSAR timing protection to build
safe and efficient ISO 26262 mixed-criticality sys-
tems. Proceedings of ERTS.
Franco, F. R. and et. al (2016). Workflow and toolchain for
developing the automotive software according autosar
standard at a virtual-ecu. In 2016 IEEE 25th Inter-
national Symposium on Industrial Electronics (ISIE),
pages 869–875.
Hans, B., Rolf, J., and Henrik, L. (2009). Annotation with
Timing Constraints in the Context of EAST-ADL2
and AUTOSAR-the Timing Augmented Description
Language. In STANDRTS’09.
Harbour, M. G., Garc
´
ıa, J. G., Guti
´
errez, J. P., and Moyano,
J. D. (2001). Mast: Modeling and analysis suite for
real time applications. In Real-Time Systems, 13th Eu-
romicro Conference on, 2001., pages 125–134. IEEE.
Henia, R., Hamann, A., Jersak, M., Racu, R., Richter, K.,
and Ernst, R. (2005). System level performance anal-
ysis – the symta/s approach. IEE Proceedings – Com-
puters and Digital Techniques, 152(2):148–166.
IBM Software (2019). Ibm rational rhapsody de-
veloper. https://www.ibm.com/software/products/en/
ratirhap. Accessed Nov 2019.
Iyenghar, P., Huning, L., and Pulvermueller, E. (2020).
Early synthesis of timing models in autosar-based au-
tomotive embedded software systems. In 8th Interna-
tional Conference on Model-Driven Engineering and
Software Development.
Iyenghar, P., Noyer, A., Engelhardt, J., Pulverm
¨
uller, E.,
and Westerkamp, C. (2016). End-to-end path delay
estimation in embedded software involving heteroge-
neous models. In 11th IEEE Symposium on Industrial
Embedded Systems, SIES, 2016, pages 183–188.
Iyenghar, P. and Pulvermueller, E. (2018). A model-driven
workflow for energy-aware scheduling analysis of iot-
enabled use cases. IEEE Internet of Things Journal,
5(6):4914–4925.
Kim, J. H., Kang, I., Kang, S., and Boudjadar, A.
(2016). A process algebraic approach to resource-
parameterized timing analysis of automotive software
architectures. IEEE Transactions on Industrial Infor-
matics, 12(2):655–671.
Klobedanz, K., Kuznik, C., Thuy, A., and Mueller,
W. (2010). Timing modeling and analysis for
AUTOSAR-based software development: a case
study. In Proceedings of Conference on Design, Au-
tomation and Test in Europe, pages 642–645. Euro-
pean Design and Automation Association.
Kusano, K. D. and Gabler, H. (2011). Method for estimat-
ing time to collision at braking in real-world, lead ve-
hicle stopped rear-end crashes for use in pre-crash sys-
tem design. SAE International Journal of Passenger
Cars – Mechanical Systems, 4(1):435–443.
Mubeen, S., Nolte, T., Sj
¨
odin, M., Lundb
¨
ack, J., and
Lundb
¨
ack, K.-L. (2019). Supporting timing analy-
sis of vehicular embedded systems through the refine-
ment of timing constraints. Journal of Software and
Systems Modeling, 18:36–69.
Noyer, A., Iyenghar, P., Engelhardt, J., Pulvermueller, E.,
and Bikker, G. (2016a). A model-based framework
encompassing complete workflow from specification
until validation of timing requirements in embedded
software systems. Software Quality Journal, pages 1–
31.
Noyer, A., Iyenghar, P., Pulvermueller, E., Engelhardt, J.,
and Bikker, G. (2016b). Coupling of timing prop-
erties for embedded realtime systems using a hybrid
ENASE 2020 - 15th International Conference on Evaluation of Novel Approaches to Software Engineering
488