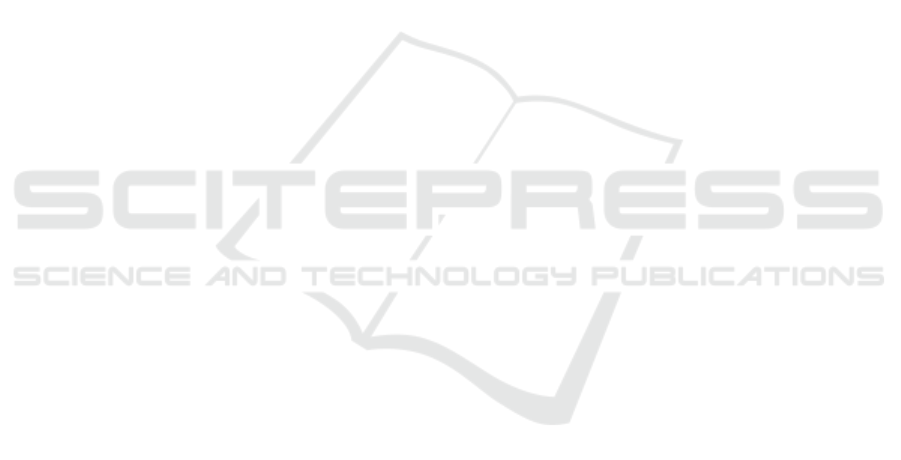
5 KNOWLEDGE TRANSFER
FROM INDUSTRY TO
ACADEMIA
The challenge of transferring best practices from the
industry to the students is at least two-fold: identify-
ing the best practices and finding a suitable vessel for
transport to the minds of students.
Sch
¨
on (1987) has studied how practitioners learn.
This arises interesting questions such as how educa-
tors learn, what is the differences in information ver-
sus knowledge; education versus training; learning
versus teaching.
5.1 Identifying Best Practices
It is a common conception that industry and academia
is two worlds with (too) few connections. So how
can academics identify the best practices? Teachers
taking sabbaticals in companies would help teachers
to gain access to this ”hidden” knowledge. Since this
knowledge is hidden or implicit (Frappaolo, 2008) it
may not be easy to identify or to articulate. Some
skills are hard to put into words, such as riding a bike
or a swing. Berry (1987) states ”The fact that much
of an expert’s knowledge is implicit or tacit in nature
is a major problem for those working in the area of
knowledge elicitation.”
Another possibility is for the university to recruit
people with professional experience from the indus-
try, both in temporary and permanent positions. The
latter requires universities to change their job can-
didate evaluation procedure to include non-academic
achievements.
5.2 Vessel for Knowledge Transfer
In most subjects, the methods to achieve learning
goals vary depending on what the goals are. One pop-
ular system for this is constructive alignment (Biggs,
1996). Transferring best practice from industry to stu-
dents is not different in this respect. However, an
important keyword here is practice. Only hearing or
reading about best practices will probably be insuf-
ficient and ineffective since a lot of this knowledge
often is hidden/implicit/tacit and of a more practi-
cal and non-theoretic nature. Sch
¨
on (1987) states “I
have come to feel that [the] only learning which sig-
nificantly influences behavior is self-discovered, self-
appropriated learning.”
Guest lectures, case studies and selected industrial
challenges are ways to achieve this kind of awareness
with the students. Likewise, a selection of carefully
crafted exercises, assignments and projects that are
closely linked to an industrial setting could help illu-
minate the importance of the best practices. However,
the scale of systems found in the industry will often be
significantly bigger than what we are able to recreate
in university laboratories. Thus, it can be hard to find
means to scale exercises in a way fitting to the univer-
sity context and at the same time bringing forward the
challenges of large scale systems.
Compacting years of industrial experience into in-
formation that students can digest in a short time is
very challenging. In an industrial setting, a task can
be difficult either because it is technically challenging
or because it has a huge volume (a lot of data, equip-
ment, tools, etc., or a lot of connections). In a teach-
ing setting the former can more easily be adapted to
the students’ competency levels through making the
industrial problems the basis for exercises with suffi-
cient guidelines etc. The latter, big volume, is harder
to copy. How could we copy a big industrial setting to
the classroom and achieve anything in a short time?
Obviously, some scaling is needed. One idea could
be to carefully design a number of closely related as-
signments given to groups of students that together
formed a single large project.
Probably, in some cases we will have to accept
that there is no shortcut to gain experience, ”you have
to walk the walk”. However, in many cases, there are
ways to accelerate the process. One important tool
could be the use of hardware-in-the-loop (HIL) simu-
lation equipment (Schlager, 2008). HIL enables stu-
dents to gain experience from controlling equipment
that is normally not possible to operate on in a uni-
versity setting. The author has experimented with us-
ing HIL in PLC teaching by employing a HIL valve
simulator (Osen, 2019). A similar approach has been
used by De Farias et al. (2019) and Shiakolas and
Piyabongkarn (2003).
6 FURTHER WORK
In order to complete this study on program structure, I
am planning to write a follow-up article on how func-
tion blocks should be designed. Thereafter it could be
useful to describe good practices on how to divide a
large project plant into sections with a focus on pro-
gramming, communications, reliability and safety.
On a more general level, it would be interesting
to research in more detail different methods to trans-
fer knowledge from the industry to the students, both
from a PLC or real-time programming perspective
and a more general computer science perspective.
CSEDU 2020 - 12th International Conference on Computer Supported Education
478