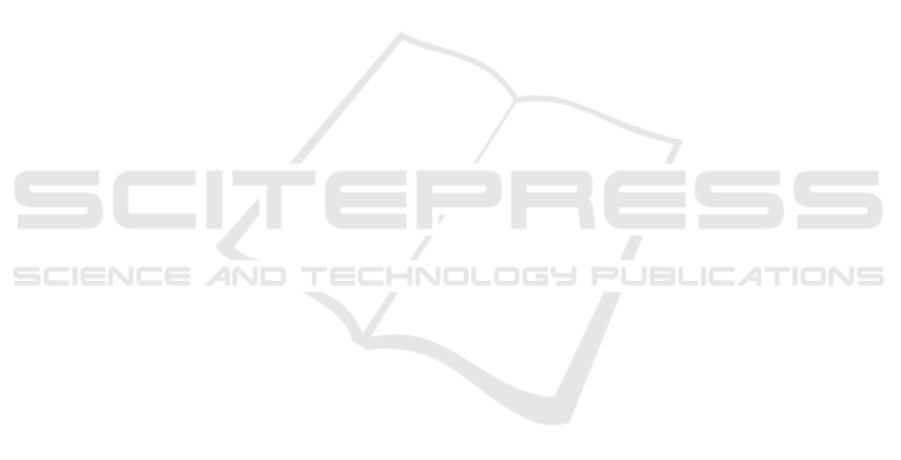
cation framework to time-independent trajectories and
user-configurable task horizons. In Proc. of IEEE Int.
Conf. on Robotics and Automation (ICRA).
Decr
´
e, W., Smits, R., Bruyninckx, H., and De Schutter, J.
(2009). Extending iTaSC to support inequality con-
straints and non-instantaneous task specification. In
Proc. of IEEE Int. Conf. on Robotics and Automation
(ICRA).
Deisenroth, M. P., Neumann, G., and Peters, J. (2013). A
survey on policy search for robotics. Foundations and
Trends in Robotics, 2:1–142.
Duan, J., Ou, Y., Xu, S., Wang, Z., Peng, A., Wu, X., and
Feng, W. (2018). Learning compliant manipulation
tasks from force demonstrations. In IEEE Int. Conf.
on Cyborg and Bionic Systems (CBS).
Kalakrishnan, M., Righetti, L., Pastor, P., and Schaal, S.
(2011). Learning force control policies for compliant
manipulation. In Proc. of IEEE/RSJ Int. Conf. on In-
telligent Robots and Systems (IROS).
Kober, J. and Peters, J. (2014). Policy search for motor
primitives in robotics. In Learning Motor Skills, pages
83–117. Springer.
Kober, J. and Peters, J. R. (2009). Policy search for motor
primitives in robotics. In Advances in Neural Infor-
mation Processing Systems (NIPS).
Leidner, D., Borst, C., Dietrich, A., Beetz, M., and Albu-
Sch
¨
affer, A. (2015). Classifying compliant manipula-
tion tasks for automated planning in robotics. In Proc.
of IEEE/RSJ Int. Conf. on Intelligent Robots and Sys-
tems (IROS).
Leidner, D. S. (2017). Cognitive reasoning for compliant
robot manipulation. PhD thesis, Universit
¨
at Bremen.
Lenz, I., Knepper, R. A., and Saxena, A. (2015). DeepMPC:
Learning deep latent features for model predictive
control. In Proc. of Robotics: Science and Systems
(RSS).
Lioutikov, R., Kroemer, O., Maeda, G., and Peters, J.
(2016). Learning manipulation by sequencing motor
primitives with a two-armed robot. In Intelligent Au-
tonomous Systems 13. Springer.
Mason, M. T. (1981). Compliance and force control for
computer controlled manipulators. IEEE Trans. on
Systems, Man, and Cybernetics, 11(6).
Mitsioni, I., Karayiannidis, Y., Stork, J. A., and Kragic, D.
(2019). Data-driven model predictive control for the
contact-rich task of food cutting. In Proc. of Int. Conf.
on Humanoid Robots (HUMANOIDS).
N
¨
agele, F., Halt, L., Tenbrock, P., and Pott, A. (2018). A
prototype-based skill model for specifying robotic as-
sembly tasks. In Proc. of IEEE Int. Conf. on Robotics
and Automation (ICRA).
Nemec, B.,
ˇ
Zlajpah, L., and Ude, A. (2017). Door open-
ing by joining reinforcement learning and intelligent
control. In Proc. of Int. Conf. on Advanced Robotics
(ICAR).
Ott, C., Mukherjee, R., and Nakamura, Y. (2010). Unified
impedance and admittance control. In Proc. of IEEE
Int. Conf. on Robotics and Automation (ICRA).
Ott, C., Mukherjee, R., and Nakamura, Y. (2015). A hybrid
system framework for unified impedance and admit-
tance control. Journal of Intelligent & Robotic Sys-
tems (JINT), 78(3-4):359–375.
Peters, J. and Schaal, S. (2006). Policy gradient methods for
robotics. In Proc. of IEEE/RSJ Int. Conf. on Intelligent
Robots and Systems (IROS).
Polydoros, A. S. and Nalpantidis, L. (2017). Survey of
model-based reinforcement learning: Applications on
robotics. Journal of Intelligent & Robotic Systems
(JINT), 86(2):153–173.
Smits, R., De Laet, T., Claes, K., Bruyninckx, H., and
De Schutter, J. (2008). itasc: A tool for multi-sensor
integration in robot manipulation. In Proc. of IEEE
Int. Conf. on Multisensor Fusion and Integration for
Intelligent Systems (MFI).
Sutton, R. S. and Barto, A. G. (2018). Reinforcement learn-
ing: An introduction. MIT press.
Theodorou, E., Buchli, J., and Schaal, S. (2010a). Learning
policy improvements with path integrals. In Proc. of
Int. Conf. on Artificial Intelligence and Statistics.
Theodorou, E., Buchli, J., and Schaal, S. (2010b). Rein-
forcement learning of motor skills in high dimensions:
A path integral approach. In Proc. of IEEE Int. Conf.
on Robotics and Automation (ICRA).
Learning to Close the Gap: Combining Task Frame Formalism and Reinforcement Learning for Compliant Vegetable Cutting
231