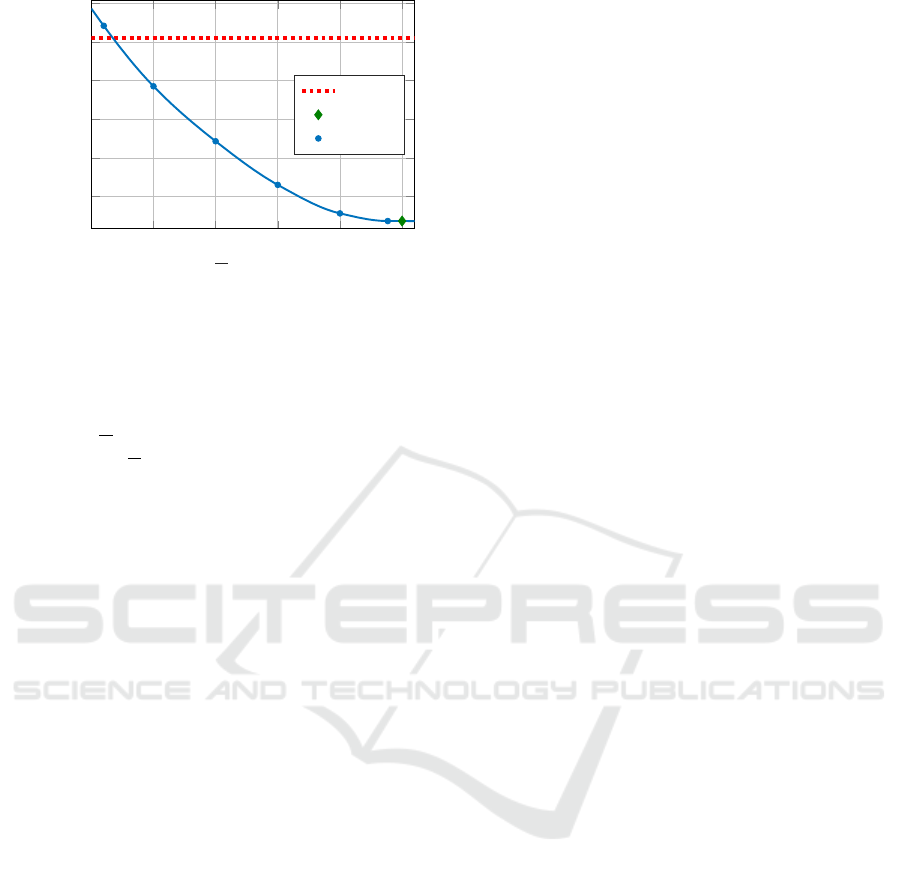
0
250 500 750
1000
1250
147
147.5
148
148.5
149
149.5
T
d
in Nm
t
f
in s
C0
C1
sample
Figure 5: Lap time over maximum torque of SLD.
ally, the increased vehicle weight and inertia due to
the SLD, implemented according to (Sedlacek et al.,
2020b), is detrimental for cornering. The benefit of
lateral drive torque allocation outweighs this disad-
vantage for T
d
> 87.3Nm, whereas lap time reduces
with increasing T
d
. Since for the current track and ve-
hicle setup |T
d
| ≤ 1193Nm holds, lap time reductions
due to the SLD only occur up this threshold value.
However, this result strongly depends on the consid-
ered track and vehicle setup.
5 CONCLUDING REMARKS
A novel OCP-modelling approach for a broad class
of semi-active actuators has been presented. The pro-
cedure transforms the originally nonconvex set dic-
tated by the passivity constraint into multiple con-
vex sets. However, this convexification requires an
extra input and generally a higher number of con-
straints. The method has been applied to compute
minimum-lap-time trajectories for a vehicle with rear-
wheel drive and SLD at the rear axle. The OCP
has been solved using Hermite-Simpson collocation
implemented in an open-source framework. Com-
pared to a vehicle with open differential instead of
the SLD, lap time is greatly reduced by 2.37 seconds
or 1.59% with lap time benefits primarily occurring
when exiting corners. Although the overall OCP re-
mains nonconvex for the considered application, the
presented convexification measure is a first step to-
wards a fully convex OCP for such vehicles which
we will address in the future. Considering our pre-
vious work (Sedlacek et al., 2020b; Sedlacek et al.,
2020a), the proposed method will be used to com-
pare different powertrain topologies for vehicles with
combustion engine or electric machines while simul-
taneously identifying the respective optimal passive
vehicle setups. A detailed experimental comparison
of the proposed modelling-method with the existing
methods presented in section 3.2.4 is subject of future
work.
REFERENCES
Betts, J. T. (2010). Practical Methods for Optimal Control
and Estimation Using Nonlinear Programming. So-
ciety for Industrial and Applied Mathematics, second
edition.
Bianco, N. D., Bertolazzi, E., Biral, F., and Massaro, M.
(2019). Comparison of direct and indirect methods for
minimum lap time optimal control problems. Vehicle
System Dynamics, 57(5):665–696.
Boyd, S. and Vandenberghe, L. (2004). Convex Optimiza-
tion. Cambridge University Press, Cambridge, sev-
enth edition.
Cheli, F., Pedrinelli, M., Resta, F., Travaglio, G., Zanchetta,
M., and Zorzutti, A. (2006). Development of a new
control strategy for a semi-active differential for a
high-performance vehicle. Vehicle System Dynamics,
44(sup1):202–215.
Dunning, I., Huchette, J., and Lubin, M. (2017). Jump:
A modeling language for mathematical optimization.
SIAM Review, 59(2):295–320.
Gillespie, T. (1992). Fundamentals of Vehicle Dynamics.
SAE International.
Kelly, D. (2008). Lap time simulation with transient vehicle
and tyre dynamics. PhD thesis, Cranfield University.
Kelly, M. (2017). An introduction to trajectory optimiza-
tion: How to do your own direct collocation. SIAM
Review, 59(4):849–904.
Kim, Y., Kwon, C., Moon, H., Kim, K., Cho, J., and Kong,
K. (2018). Optimization of semi-active pneumatic ac-
tuators for an exoskeleton robot for running. 2018
15th International Conference on Ubiquitous Robots
(UR), pages 119–124.
Kr
¨
uger, W. (2000). Integrated design process for the de-
velopment of semi-active landing gears for transport
aircraft. PhD thesis, University of Stuttgart.
Limebeer, D., Perantoni, G., and Rao, A. (2014). Optimal
control of formula one car energy recovery systems.
International Journal of Control, 87(10):2065–2080.
Limebeer, D. J. N. and Perantoni, G. (2015). Optimal con-
trol of a formula one car on a three-dimensional track-
part 2: Optimal control. Journal of Dynamic Systems,
Measurement, and Control, 137(5).
Perantoni, G. and Limebeer, D. J. (2014). Optimal control
for a formula one car with variable parameters. Vehi-
cle System Dynamics, 52(5):653–678.
Poussot-Vassal, C., Savaresi, S. M., Spelta, C., Sename, O.,
and Dugard, L. (2010). A methodology for optimal
semi-active suspension systems performance evalua-
tion. In 49th IEEE Conference on Decision and Con-
trol (CDC), pages 2892–2897.
Savaresi, S. M., Poussot-Vassal, C., Spelta, C., Sename, O.,
and Dugard, L. (2010). Semi-Active Suspension Con-
trol Design for Vehicles. Elsevier, first edition.
Convexification of Semi-activity Constraints Applied to Minimum-time Optimal Control for Vehicles with Semi-active Limited-slip
Differential
23