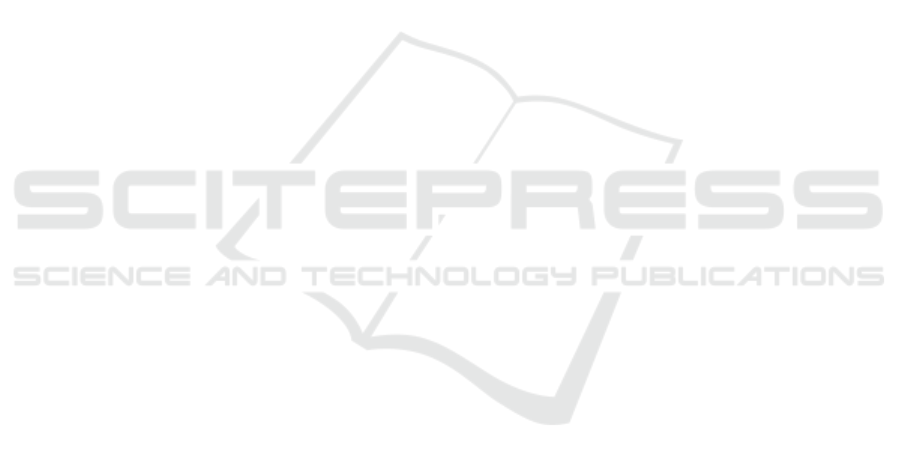
from a relational database) of a more conventional
commercial application, such as an ERP (Enterprise
Resource Planning) or a CRM (Customer Relation-
ship Management).
1.2 Big Data for Predictive
Maintenance. Making a Profit
Comes First
In general, maintenance can be classified as two main
groups: Corrective (CM) Preventive (PM) and Predic-
tive (PdM) Maintenance. CM is carried out when the
machine fails or some of the elements of the equip-
ment are damaged and must be replaced or repaired,
this element and/or part will be responsible for a fail-
ure in the entire line if the action is not executed. PM
is carried out to prevent fail, as a rutinary mainte-
nance task. However, the PM is carried out before
the equipment fails. The purpose of a PM order is to
promote continuous production of the system and/or
minimize the loss of performance. Usually, in the
industry the indicator of deterioration is constructed
through the monitoring of variables such as vibration,
temperature and noise of the machine. However, if
we want to avoid line shutdowns, it would be nec-
essary to build Big Data and place these sensors on
all machines and this would lead to exorbitant costs,
(A.K.S.Jardine et al., 2006).Therefore, there is cur-
rently no system that performs this task in real time
and for all machines, and this causes that, currently,
only specific machines are sensorized and/or that one
or more operators take measurements of the machines
“manually”, that is, they transfer the sensors from one
machine to another.
2 PREVIOUS WORKS
2.1 From the Micro-term to the
Long-term
The literature classifies the data used in the analysis
of the manufacturing process into two types, the long-
term data (long-terms) and the short-term data (short-
terms). Long-term data are used mainly for pro-
cess planning while short-term data are used mainly
for process control. There is abundant literature
that works with the analysis of long-term times, in
comparison with the literature that studies short-term
times. Following the definition of (L.Li et al., 2009),
the short-term data refer to a time not long enough
for the failure period of the machine and where the
cycle time of the machine is considered short-term
time. In (E.Garcia, 2016) the short term is redefined
in two new terms, the mini-term and the micro-term.
A mini-term can be defined as the time that a part of
the machine needs to perform its own task. This mini-
term subdivision can be selected based on a policy of
preventive maintenance or in a breakdown, in which
it could be replaced in an easier and faster way than
another sub-divided part of the machine. Also a mini-
term could be defined as a sub-division that allows us
to understand and study the machine behaviour. In
the same way, a micro-term is defined as the time in
which each part of the mini-term could be divided it-
self. This model has been published in (E.Garcia and
N.Montes, 2017).
2.2 Mini-term Degradation Path. A
Change Point
Prediction and analysis of degradation paths are im-
portant to condition-based maintenance (CBM). It is
well known that the degradation paths are non-linear.
It means that in the degradation path, a sudden change
point appears when the RUL (Remaining Useful Life)
is near the end, see (X.Zhao, 2018), (X.Zhao, 2014).
Before the change point, the component works in op-
timal conditions and after the change point the com-
ponent works in bad conditions alerting that the fail-
ure will happen soon.
The change point in the physical part of the ma-
chine components produces a similar effect in the sub-
cycle time, that is, a change point in the mini-term,
Figure 2 shows cases measured at Ford factory in Al-
mussafes. When a change point is dectected in the
mini-term, an alarm must be activated for the mainte-
nance workers to replace it, as soon as possible.
3 TOWARDS BIG DATA BASED
ON MINITERMS FOR
PREDICTIVE MAINTENANCE
The results presented in (E.Garcia et al., 2018) gener-
ated a great expectation at Ford Motor Company, be-
cause the mini-term provides a great advantage over
other sensors, it is easier and cheaper to install. It is
cheap because no additional hardware installation is
required to measure the sub-cycle time, just the use
of the PLC and sensors installed for the automated
production process, and it is easy because we only
need to code extra timers into the PLC. Therefore, the
Ford Motor Company began the implementation of
mini-terms in its Almussafes plant and for this pur-
pose the application shown in Figure 1 was devel-
ICINCO 2020 - 17th International Conference on Informatics in Control, Automation and Robotics
118