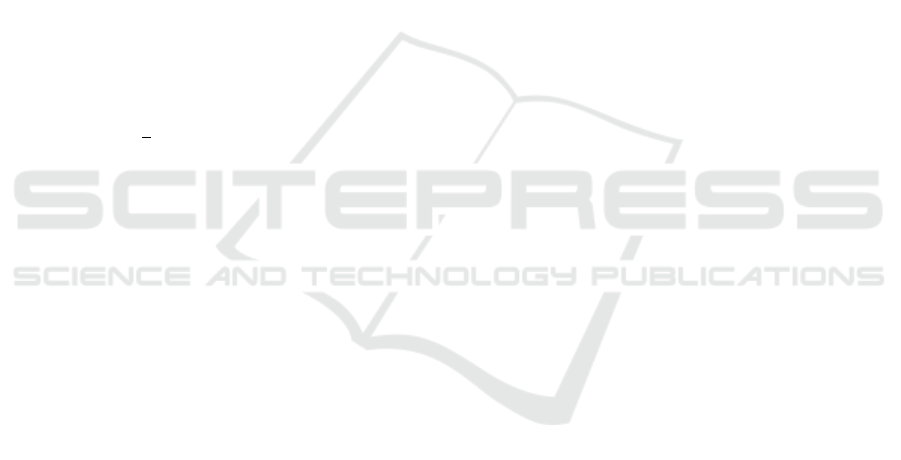
particular joints. Mechanical structure deterioration
or the deterioration of electrical parts also affects the
speed. This pathology is very difficult to detect by the
maintenance workers because it does not produce the
breakdown of the machine and, as the robot moves
at high speed, it is nearly impossible to be detected
without a specific procedure.
3.2 Experimental Test
The experimental methodology is as follows. The
clamping task is to weld the same point 6 times in
order to obtain enough time precision. The robot arm
trajectory is the same in all the movements. Then,
the clamping task is repeated 40 times in order to ob-
tain a sufficient number of samples to measure the
mean value and the standard deviation for each mini-
term. First, the welding clamp station is tested with-
out any of the pathologies hereinbefore explained.
Afterwards, a particular component with each pathol-
ogy is replaced in the station and the test is repeated.
It is important to remark that the components are in
the normal production rate. Table 1 shows the ex-
perimental result measurements of all pathologies for
each mini-term. (x, S).
4 WELDING LINE. MODELLING
AND SIMULATION
A previous section shows how the welding unit and,
machines in general, have a probabilistic behaviour.
In addition, the deterioration of the machines pro-
duces a delay in the intermediate task and/or in the
standard deviation. In this section we will analyse
how many jobs are lost in a real line due to these
pathologies. For this purpose, a real welding line in
Ford S.A. located at the Almussafes factory has been
selected. The welding line was installed in 1980. The
staff group that designed the line defined the maxi-
mum running capacity, ECR (engineering running ca-
pacity), 60 JPH. However, the plant engineers have
another maximum running capacity, that is the ERR
(engineering running rate), in this case defined in 51
JPH. And our daily production to reach is GRR (Get
Ready Requirement) our (28,9 JPH). The GRR means
market requirements, i.e. customers’ orders. Figure 6
shows the production rate of the welding line.
In a real welding line like this, there are welding
workstations where, each one of them has welding
stations working in parallel and sometimes in serial.
Each welding station makes some welding points in
the same cycle time. We can find 1, 2, 4 or at least 6
welding stations in the same workstation, where each
one of them makes up to 19 welding points, see ta-
ble 3. In our particular case, our welding line has 8
workstations where 3 are for 6 welding units, 4 with
4 welding units, and 1 for 1 welding unit. Each weld-
ing unit is modelled with robot motion, welding mo-
tion, welding task as well as the offset. Robot mo-
tion means how many seconds the robot is moved,
the welding motion and welding task mean how many
welding points the welding clamp has to perform. The
offset means how many seconds the welding station
must wait for another station to do the job.
5 WELDING LINE SIMULATION
In order to simulate the welding line, a state ma-
chine simulator is developed. There are three pos-
sible workstation states: “Working”, “Starving” and
“Blocking”, see figure 3 and figure 7. The loop is up-
dated with an incremental time of 0.01 seconds. In
the simulated welding line, there is always a job in
the first workstation, so that the blocking state can-
not happen in the first station. In addition, all the
jobs finished in the last workstation are removed, so
that the “Starving” state in the last workstation can-
not happen. The loop starts with all the stations in the
“Blocking” state.
The cycle time for each workstation is the maxi-
mum cycle time of each welding station that works in
parallel, indicating the slowest welding unit and the
bottleneck for a particular workstation. The transfer
time is added to the cycle time. This time is the time
required to transport the car from one workstation to
the next one (12 seconds), see figure 8.
The cycle time of each welding unit is computed
as shown in figure 9. A pseudo-random number based
on mean and variance is computed for each mini-
term using the experimental values of table 2. The
algorithm repeats the creation of a number as many
times as the mini-term is repeated (i.e. for 10 weld-
ing points, the algorithm will produce 10 numbers).
The offset is also added if necessary. The simula-
tion is computed with two time bases, one hour (JPH)
and one day (JPD) with an incremental time of 0.01
seconds. This simulation is repeated 50 times and
the mean and variance of the jobs produced are com-
puted. First, the simulation with any pathology is
performed. The results are for one-hour time base,
(51,1.05) JPH, similar than the ERR, and for one-day
time base, (1252, 3.09) JPD. Table 2 shows the sim-
ulation results where a particular pathology is located
in a particular welding station. Obviously, the rest of
welding units are considered without pathology.
A Novel Model to Analyse the Effect of Deterioration on Machine Parts in the Line Throughput
31