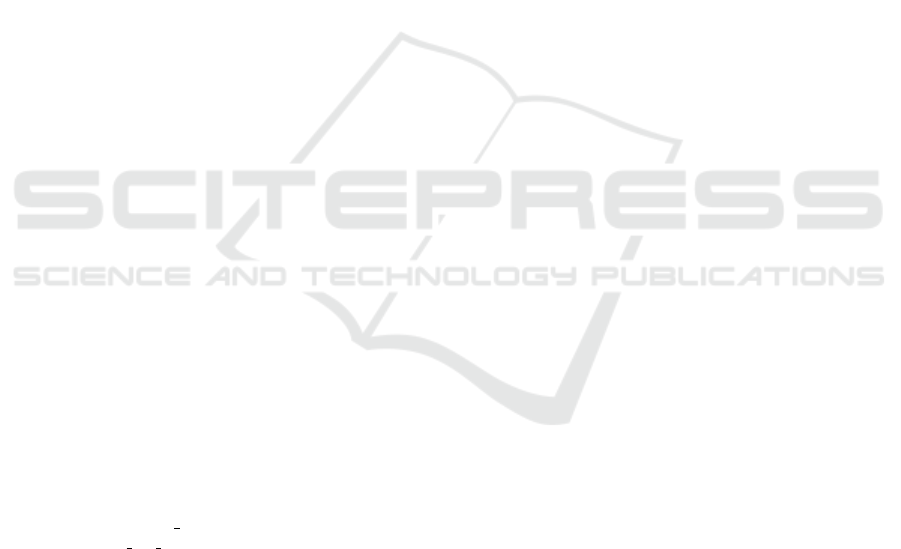
and a system design model to check for consistency,
whereas we propose a multi-step approach where we
only employ the requirements set itself for the consis-
tency checking and only add the system architecture
for verification purpose.
7 CONCLUSION
In this paper we presented an approach to support
the early validation of AUTOSAR software architec-
tures by simplifying the process of AUTOSAR tim-
ing requirements specifications. We presented an ap-
proach for checking consistency of AUTOSAR tim-
ing requirements, which improves the requirements
quality. Especially by computing the maximum set
of satisfiable timing requirements the user can easily
identify faulty model elements. We showed that the
consistency checking only takes a fraction of time in
comparison with the verification task, which has to be
performed afterwards. Thus checking consistency be-
fore verification can be very beneficial in the case of
an inconsistent requirement set, but does not signifi-
cantly slow down the whole verification process even
in the case of consistent requirements sets. In the fu-
ture we will evaluate our approach on more realistic
examples.
REFERENCES
Abdelhalim, I., Schneider, S., and Treharne, H. (2011).
Towards a Practical Approach to Check UML/fUML
Models Consistency Using CSP. In ICFEM 2011, vol-
ume 6991, pages 33–48. Springer Berlin Heidelberg.
Andr
´
e, C. (2009). Syntax and Semantics of the Clock Con-
straint Specifcation Language (CCSL). Phd., Inria In-
stitute, Sophia Antipolis.
AUTOSAR (2019). AUTomotive Open System AR-
chitecture Methodology. https://www.autosar.
org/fileadmin/user upload/standards/classic/19-11/
AUTOSAR TR Methodology.pdf.
Bauer, A., Leucker, M., and Streit, J. (2006). SALT -
Structured Assertion Language for Temporal Logic.
In ICFEM 2006, volume 4260 of LNCS. Springer.
Behrmann, G., David, R., and Larsen, K. G. (2004). A tu-
torial on uppaal. In Formal Methods for the Design of
Real-Time Systems, pages 200–236. Springer.
Beringer, S. and Wehrheim, H. (2016). Verification of
AUTOSAR Software Architectures with Timed Au-
tomata. In FMICS-AVoCS 2016, volume 9933 of
LNCS, pages 189–204. Springer.
Bjorner, N. and Phan, A.-D. (2014). vZ - Maximal Satis-
faction with Z3. In SCSS 2014, volume 30 of EPiC
Series in Computing, pages 1–9. EasyChair.
Chaochen, Z., Hoare, C., and Ravn, A. P. (1991). A Cal-
culus of Durations. Information Processing Letters,
40(5):269–276.
Derrick, J., Akehurst, D., and Boiten, E. (2002). A frame-
work for UML consistency. In UML 2002 Workshop
on Consistency Problems in UML-based Software De-
velopment, volume 2460 of LNCS, pages 182–196.
Springer.
EAST-ADL Association (2013). EAST-ADL Domain
Model Specification.
Engels, G., Heckel, R., and K
¨
uster, J. M. (2001). Rule-
Based Specification of Behavioral Consistency Based
on the UML Meta-model. In UML 2001, volume 2185
of LNCS, pages 272–286. Springer Berlin Heidelberg.
Garey, M. R., Johnson, D. S., and Stockmeyer, L. (1976).
Some simplified NP-complete graph problems. Theo-
retical Computer Science, 1(3):237–267.
Gruhn, V. and Laue, R. (2006). Patterns for Timed Prop-
erty Specifications. In Electronic Notes in Theoretical
Computer Science, volume 153, pages 117–133.
IEEE (1998). IEEE 830-1998 Recommended Practice for
Software Requirements Specifications.
Jacobs, J. and Simpson, A. (2017). On the formal interpreta-
tion and behavioural consistency checking of SysML
blocks. Software & Systems Modeling, 16(4):1145–
1178.
Kalibatiene, D., Vasilecas, O., and Dubauskaite, R. (2013).
Rule Based Approach for Ensuring Consistency in
Different UML Models. In Information Systems 2013,
volume 161 of LNBIP, pages 1–16. Springer.
Kim, J. H., Larsen, K. G., Nielsen, B., Mikucionis, M.,
and Olsen, P. (2015). Formal Analysis and Testing
of Real-Time Automotive Systems Using UPPAAL
Tools. In FMICS 2015, volume 9128 of LNCS, pages
47–61. Springer.
Klein, F. and Giese, H. (2007). Joint Structural and Tem-
poral Property Specification Using Timed Story Sce-
nario Diagrams. In FASE 2007, volume 4422 of
LNCS, pages 185–199. Springer.
Kotb, Y. and Katayama, T. (2005). Consistency Checking
of UML Model Diagrams Using the XML Semantics
Approach. In WWW 2005, pages 982–983. ACM.
Kroening, D. and Strichman, O. (2008). Decision Proce-
dures: An Algorithmic Point of View. Springer Berlin
Heidelberg.
Mahmud, N., Seceleanu, C., and Ljungkrantz, O. (2016).
ReSA Tool: Structured Requirements Specification
and SAT-based Consistency-checking. In FedCSIS
2016, pages 1737–1746. IEEE.
Mallet, F. and Simone, R. d. (2015). Correctness issues
on MARTE/CCSL constraints. Science of Computer
Programming, 106:78–92.
Mendonc¸a, M., Wasowski, A., and Czarnecki, K. (2009).
SAT-based Analysis of Feature Models is Easy. In
SPLC 2009, pages 231–240. ACM.
Mens, T., Van der Straeten, R., and Simmonds, J. (2005).
A Framework for Managing Consistency of Evolving
UML Models. In Software Evolution with UML and
XML, pages 1–30. IGI Global.
Consistency Analysis of AUTOSAR Timing Requirements
25