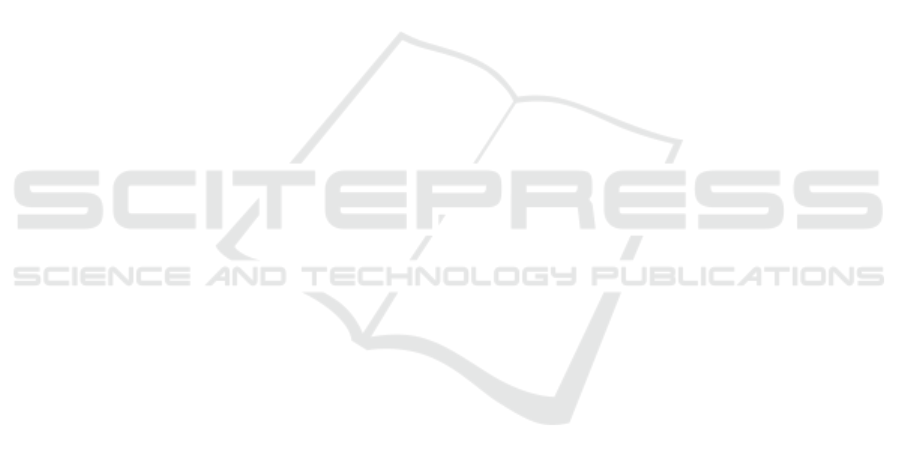
global criteria and arbitration rules that can be sat-
isfied by means of heuristic models or by solving
optimization problems. The functional level enables
to run fast simulations and get approximated results
in the early stages of system design, which provides
a good way to test and validate control strategies.
Also, architecture changes are easy and not much
time-consuming at this level. Lastly, a multi-physical
model well calibrated can provide results close to ex-
perimental data and enables to evaluate a large vari-
ety of scenarios with good accuracy. This method-
ology was applied to a thermal management system
use-case and has provided positive results. A non-
saturation criterion has been introduced in the teleo-
logical level in order to improve the resource manage-
ment with critical conditions.
A first perspective of this work is to use this three-
level abstraction modeling to optimize the global en-
ergy consumption of a system. An interesting use-
case could be a whole electric vehicle composed by
the thermal management and the power-train subsys-
tems.
Another objective is the extension of the func-
tional modeling to systems in which energy and mat-
ter flows are coupled. A use-case could be a water
recycling system, in which consumers have both mat-
ter (water) and energy (heat) needs that must be dis-
tributed between matter or energy (or both) sources.
Future work intends to develop and implement op-
timization algorithms directly in the functional model.
Lastly, the teleological level could integrate some
levels of arbitration between several missions of the
system, which would have several operating modes
optimizing different objectives.
REFERENCES
Borutzky, W. (2010). Bond Graph Methodology: Develop-
ment and Analysis of Multidisciplinary Dynamic Sys-
tem Models. Springer-Verlag London.
Brunet, J., Flambard, L., and Yazman, A. (2005). A hard-
ware in the loop (hil) model development and imple-
mentation methodology and support tools for testing
and validating car engine electronic control unit. In
International Conference on Simulation Based Engi-
neering and Studies, TCN CAE, Lecce, Italy.
Ding, P., Wang, Z., Wang, Y., and Li, K. (2020). A dis-
tributed multiple-heat source staged heating method
in an electric vehicle. Renewable Energy, 150:1010–
1018.
Fauvel, C., Claveau, F., and Chevrel, P. (2014). Energy
management in multi-consumers multi-sources sys-
tem : a practical framework. In IFAC World Congress.,
pages 2260–2266, Cape Town, South Africa.
Fiani, P., Boyer, B., Brunet, C., and Bruniquel, G. (2019).
Utilisation de la mod
´
elisation
´
energ
´
etique fonction-
nelle pour la synth
`
ese thermique des v
´
ehicules hy-
brides et
´
electriques. In SIA Simulation num
´
erique :
La simulation num
´
erique au sein de l’innovation au-
tomobile., Saint-Quentin en Yvelines, France.
Fiani, P., Chavanne, S., Taleb, L. A., and M
¨
ok
¨
ukc
¨
u,
M. (2016). Mod
´
elisation pour la conception et
l’
´
evaluation de syst
`
emes complexes. Revue Ing
´
enieurs
de l’automobile, 841.
Gross, O. and Clark, S. (2011). Optimizing electric vehicle
battery life through battery thermal management. SAE
International Journal of Engines.
M
¨
ok
¨
ukc
¨
u, M., Fiani, P., Chavanne, S., Taleb, L. A., Vlad,
C., and Godoy, E. (2017). Control architecture mod-
eling using functional energetic method: Demonstra-
tion on a hybrid electric vehicle. In 14th Interna-
tional Conference on Informatics in Control, Automa-
tion and Robotics (ICINCO), Madrid, Spain.
M
¨
ok
¨
ukc
¨
u, M., Fiani, P., Chavanne, S., Taleb, L. A., Vlad,
C., Godoy, E., and Fauvel, C. (2016). A new concept
of functional energetic modelling and simulation. In
The 9th Eurosim Congress on Modelling and Simula-
tion., Oulu, Finland.
Von Bertalanffy, L. (1968). General System Theory. George
Braziller, Inc.
Zhang, K., Li, M., Yang, C., Shao, Z., and Wang, L. (2019).
Exergy analysis of electric vehicle heat pump air con-
ditioning system with battery thermal management
system. Journal of Thermal Science, 29(2):408–422.
Zhang, Z., Wang, J., Feng, X., Chang, L., Chen, Y., and
Wang, X. (2018). The solutions to electric vehicle air
conditioning systems: A review. Renewable and Sus-
tainable Energy Reviews, 91:443–463.
Functional Model-based Resource Management: An Application to the Electric Vehicle Thermal Control
575