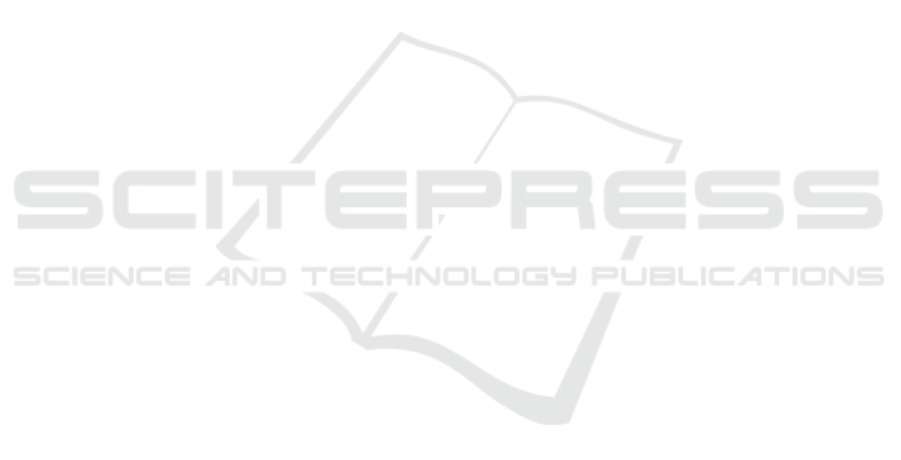
2018b; Eberhard and Ansarieshlaghi, 2019) without
investigation of the controller’s robustness on the dis-
tributed system.
The novelty of this work is, that a nonlinear feed-
back controller for high-speed trajectory tracking of a
very flexible parallel lambda robot is designed based
on the feedback linearization approach and this con-
troller consists of a position controller and a distur-
bance observer. The disturbance observer estimates
disturbances and the position controller computes the
controller input for tracking a desired trajectory by the
robot.
The disturbances on systems can be divided into
two groups, see (Chen et al., 2016), i.e., the first group
is included the disturbances that are known and mea-
surable and they can be compensated by the com-
puted feedforward input controller, the second group
is disturbances which are not measurable or measur-
ing them are very expensive. Furthermore, the second
group of disturbances needs to estimate and compen-
sate for their influences on systems. The disturbance
observer has wide application in mechatronics sys-
tems, see (Han, 2009; Chen et al., 2016; Mohammadi
et al., 2017; Liu et al., 2018), these systems needs
for high precision and high performance during doing
the desired tasks while there are disturbances affected
to the systems. These disturbances can be caused by
external disturbances, such as torques, forces during
invasive surgery (Mohammadi et al., 2017), vibra-
tions of horizontal position of a rail track, and fric-
tions of the prismatic joints (Morlock et al., 2015) or
subjected of internal model parameter as the changes
of operating conditions or external working environ-
ments and model simplification (Chen et al., 2000;
Chen, 2004). These described disturbances, external
and internal disturbances can be formulated as a vari-
able and then by disturbance observer is tried to esti-
mate and compensate them.
The disturbance observer estimates the distur-
bances that are applied to the joints and the end-
effector and then, it adapts the controlled robot to the
operating environmental conditions. The nonlinear
feedback controller consisting of the nonlinear dis-
turbance observer and position controller which they
compute the robot inputs. The designed feedback
controller is simulated on the lambda robot model.
Simulation results of the designed controller on the
lambda robot show that the end-effector tracks a tra-
jectory with high accuracy and the tracking perfor-
mance of the system under disturbances is drastically
improved compared to previous work (Ansarieshlaghi
and Eberhard, 2018b). Also, the simulation results
show that the robustness performance of the feedback
controller is increased by the designed disturbance
observer.
This paper is organized as follows: Section 2
describes the lambda robot, its components, and its
hardware setup. Section 3 consists of the modeling of
the flexible parallel lambda robot. Section 4 includes
the description of the nonlinear control, i.e., the feed-
forward controller, position controller, and nonlin-
ear disturbance observer. In Section 5, the proposed
nonlinear controller is implemented on the simulated
model and the results are discussed. Finally, the con-
clusions of the paper are presented in Section 6.
2 FLEXIBLE LAMBDA ROBOT
The lambda robot has its name coming from its phys-
ical appearance which looks like the Greek letter λ
shown in Figure 1. This robot consists of two links,
three revolute joints, and two prismatic joints. With
one of the links being shorter, roughly half the size of
the other, the characteristic appearance of the lambda
robot is created. The prismatic joints are realized with
two direct drives, each moving along their linear axis
parallel to each other. Both drives are controlled by
a servomotor. On each prismatic joint, one passive
revolute joint is fixed, providing a connection to the
links. The third revolute joint connects the end of the
short link to the middle of the long one. The long link
also has an additional mass installed at its end, which
represents an end-effector.
The robot end-effector can only move in a two-
dimensional plane, making the system planar. The
link design is very flexible. Furthermore, the robot is
characterized as a flexible planar parallel manipulator.
The drive positions and velocities of the robot are
measured with two optical encoders. Two full Wheat-
stone bridge strain gauge sets are attached to the long
flexible link to measure its deformation. The lambda
robot configuration is shown in Figure 1 has been built
in hardware, see (Burkhardt et al., 2014) at the Insti-
tute of Engineering and Computational Mechanics of
the University of Stuttgart.
3 MODELING OF THE
FLEXIBLE LAMBDA ROBOT
The modeling process of the flexible manipulator
with λ configuration is divided into three major steps.
In the first step, the flexible components of the
robot links are modeled with the linear finite element
method in the commercial finite element code ANSYS
with six hundred degrees of freedom in total. Next,
Disturbance Compensator for a Very Flexible Parallel Lambda Robot in Trajectory Tracking
395