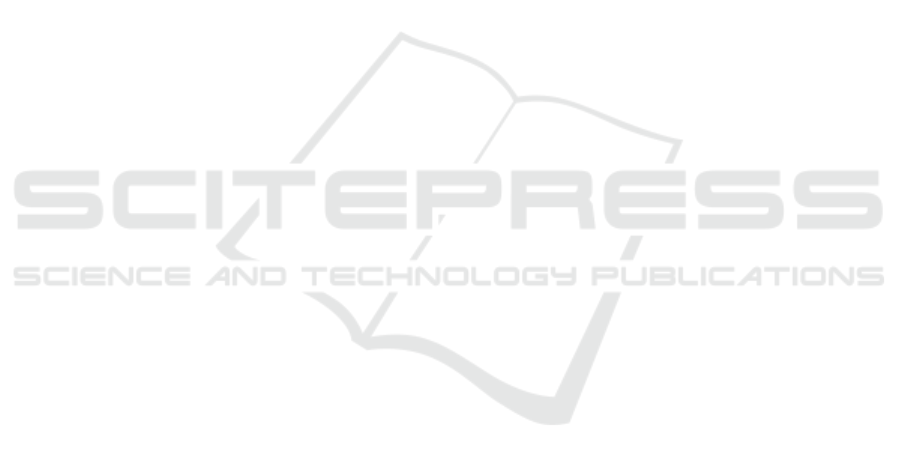
ready investigated the dynamic loads of tower cranes
when hoisting grounded loads (Maier, 2000). For the
crane analysed, this research project showed that the
dynamic factor for hoisting, according to EN 13001,
describes the loads more accurately than the specifica-
tions in the standard DIN 15018, which is now obso-
lete. However, this work provides no comparison with
the standards for crane movements involving major
displacement of the supporting structure, such as the
process of luffing or slewing.
Since the standards for mobile cranes use similar
approaches for the design, the applicability of the dy-
namic factors has been evaluated in some publications
on mobile cranes, such as (Kleeberger et al., 2014;
St
¨
olzner et al., 2018; St
¨
olzner et al., 2019). These
articles have shown that the simplified approaches of
the calculation methods currently used are often inap-
propriate for reproducing the true dynamic effects on
mobile cranes. As it can be assumed that the calcula-
tion approaches of the standards have similar deficits
for tower cranes as for mobile cranes, the dynamic
behaviour of tower cranes is analysed in more detail
below. Since the publications mentioned above show
that the greatest inaccuracies occur in the calculation
of slewing processes, this article focuses on the dy-
namic loads on tower cranes during slewing.
The nonlinear dynamic finite element method can
characterise the dynamic effects on cranes very accu-
rately. In this article, the results calculated using the
approach from the international standard ISO 8686
are evaluated by means of a comparison with the re-
sults of the nonlinear dynamic finite element calcula-
tion, as this method can be considered reliable.
Although the dynamic finite element method al-
lows exact and reliable calculations, it is very rarely
used by crane manufacturers. The main disadvantage
of this calculation method is the increased computing
effort compared to a static calculation. There is also
no reasonable way to consider the standards’ partial
safety factors in a dynamic calculation.
Alternatively, the standards permit the use of other
methods to calculate the dynamic factors. In order to
achieve a more accurate calculation of the dynamic
behaviour of tower cranes without a disproportionate
increase in computing time, a special vibration model
is presented in this publication. This new method al-
lows the dynamic factors for the slewing process to
be calculated in a more precise way than the current
methods. The applicability of the vibration model and
the calculation standard is shown for a tower crane
with different loads and load positions. In order to
assess the accuracy of the model and the standard,
several angular velocities and angular accelerations of
the tower crane are taken into account.
2 STATE of the ART
The international standard ISO 8686-1 (ISO 8686-1,
2012) defines general rules for the stress calcula-
tion of cranes. With regard to the load assumptions,
the general European standard for crane calculation
EN 13001-2 (EN 13001-2, 2014) is mostly identi-
cal to the international one. The design principles
for loads and load combinations of tower cranes are
specified in the product-specific international stan-
dard ISO 8686-3 (ISO 8686-3, 2018) and in the Eu-
ropean standard EN 14439 (EN 14439, 2010).
In the standards, the approach for considering dy-
namic loads is based on a rigid body kinetic analysis
and uses quasi-static calculation methods. In order to
take the effect of the dynamic forces into considera-
tion, the use of dynamic factors is suggested. How-
ever, the standard ISO 8686-3 also allows other val-
ues to be used for dynamic factors “when determined
by recognized theoretical analysis or practical tests”
(ISO 8686-3, 2018). The nonlinear dynamic finite el-
ement calculation and the vibration model presented
here (see Section 3) both belong to the accepted theo-
retical methods of analysis mentioned above.
To carry out the stress calculation of tower cranes,
the version of the European standard EN 14439 that
is currently valid refers to the now-obsolete stan-
dard DIN 15018 (DIN 15018, 1984) and the guide-
line FEM 1.001 (FEM 1.001, 1998). The interna-
tional standard provides fixed values for the dynamic
factors, whereas the guideline FEM 1.001 defines an-
other method of describing dynamic loads during the
horizontal movements of tower cranes. This guide-
line proposes an approach based on a two-degree-of-
freedom model, which allows the factors to be calcu-
lated depending on the crane configuration (see Sec-
tion 2.2).
In addition to the dynamic factors, both the inter-
national and the European standards prescribe the use
of partial safety factors in order to compensate for un-
certainties in the load assumptions. Since the aim of
this publication is not to evaluate safety factors but to
assess the quasi-static loads from the vibration model
and the calculation standards, no safety factors are
used. Nevertheless, the partial safety factors can be
considered in the same way as prescribed in the stan-
dards when this vibration model is used.
2.1 ISO 8686
The standard ISO 8686-3 “gives specific require-
ments and values for factors to be used at the struc-
tural calculation” (ISO 8686-3, 2018) of tower cranes.
The current draft of the product-specific European
SIMULTECH 2020 - 10th International Conference on Simulation and Modeling Methodologies, Technologies and Applications
60